In this tutorial, you will learn how to:
• | Load Moldex3D/Shell user profile |
• | Load a HyperMesh file containing geometry of a part |
• | Extract midsurface from the part geometry |
• | Assign property card(s) to the part |
• | Inspect mesh quality and thickness contour |
• | Define melt entrance boundary condition |
• | Export the model as a Moldex3D MSH file |
The model files for this tutorial are located in the file mfs-1.zip in the subdirectory \HyperMold\Moldex3D\MX_0010. See Accessing Model Files.
To work on this tutorial, it is recommended that you copy this folder to your local hard drive where you store your HyperXtrude data, for example, “C:\Users\Moldex3D\” on a Windows machine. This will enable you to edit and modify these files without affecting the original data. In addition, it is best to keep the data on a local disk attached to the machine to improve the I/O performance of the software.
2. | On the Preferences menu, click User Profiles. |
3. | In the Application field, select Manufacturing Solutions. |
4. | Select HyperMold and Moldex3D/Shell. |
|
1. | From the File menu, click Open. |
2. | Browse to the file MX_0010.hm. |
|
1. | Click Geometry > Create > Midsurfaces > Auto. |
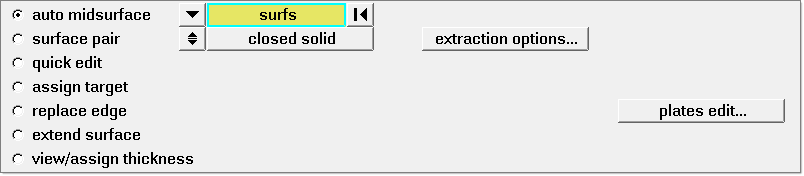
2. | Click the yellow surfs button and select displayed from the extended selection menu. |
3. | Click extract to create the midsurface. |
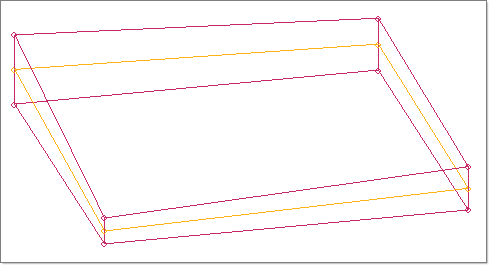
4. | Click return to close the panel. |
|
1. | Click Mesh > Create > 2D AutoMesh. |
2. | From the graphics area, select the midsurface. |
3. | In the element size field, enter 0.5. |
4. | Click mesh to create the mesh. |
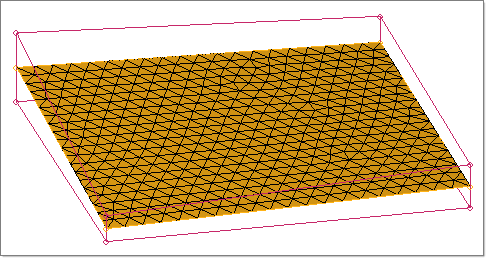
5. | Click return twice to exit the panels. |
|
1. | In the Utility menu, under the Model Setup section, click Create Property Cards. A new macro page is displayed. |
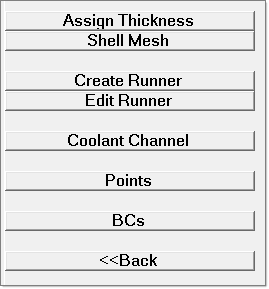
2. | Click Assign Thickness. The Extract/Assign Cavity Thickness dialog appears. |
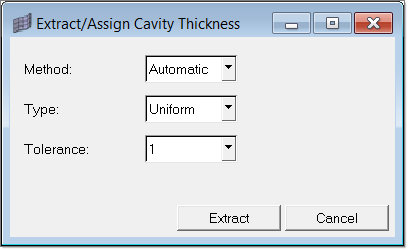
3. | Keep the default values and click Extract. A surface selection panel is displayed. |
4. | In the graphics area, select the midsurface and click proceed. The thickness is computed and a property card is assigned for each element. A contour plot appears in the graphics area that shows the distribution of element thicknesses. |
5. | Click return to close the panel. |

6. | Click Back to return to the main Utility menu. |
|
1. | On the Utility menu, click Diagnostics. A new macro page is displayed. |
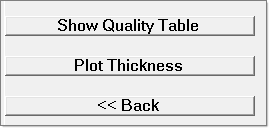
2. | Click Show Quality Table to see the mesh quality. |
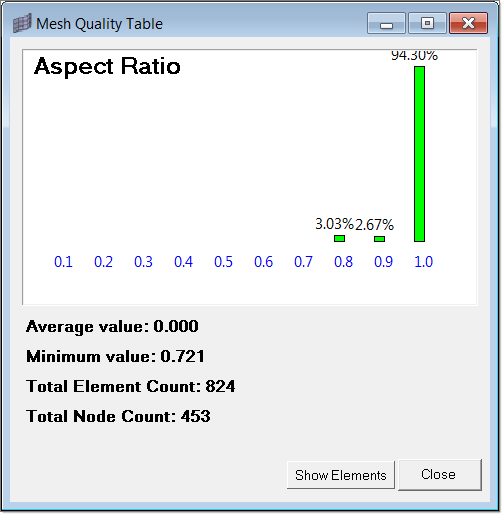
3. | Click Show Elements to see elements based on their Aspect Ratio values. |
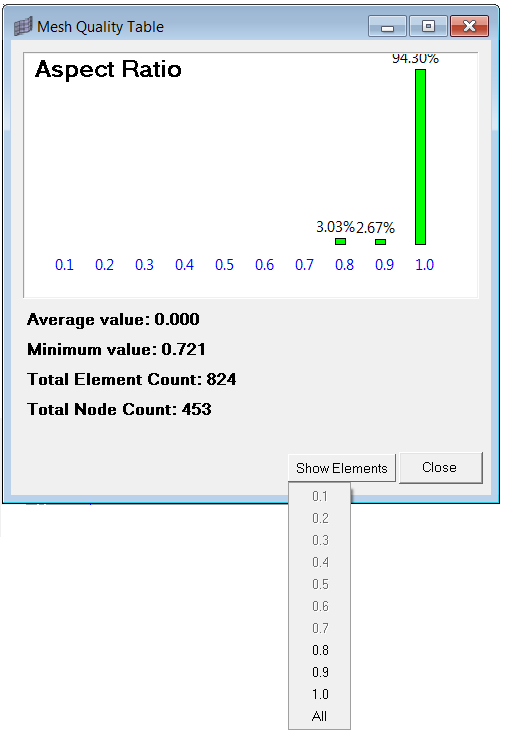
4. | Click Cancel to close the dialog. |
5. | In the Utility menu, click Plot Thickness to see the thickness contour. |
6. | Click return to close the panel. |
7. | Click Back to return to the main Utility menu. |
|
1. | From the Utility menu, click Create Property Cards. |
2. | Click BCs. A panel to select node(s) appears. |
3. | Select a node on the part from the graphic area and click proceed. The Create Boundary Condition dialog will appear. |
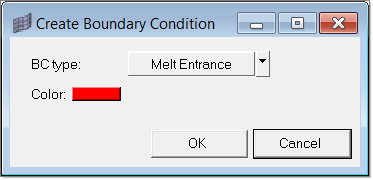
4. | Select Melt Entrance for BC type and click OK. Notice the boundary condition created on the selected node. When you apply the melt entrance directly on the mesh, the direction of the load vector created depends on the direction of the normal. However, this should not matter in the simulation. |
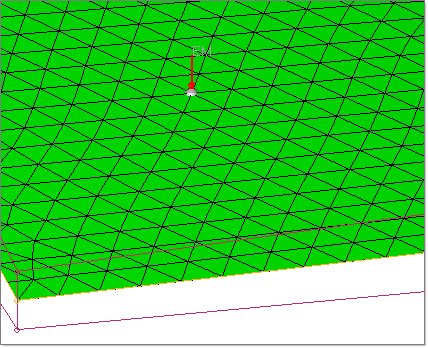
5. | Click Back to return to the main Utility menu. |
|
1. | On the Utility menu, click Export. A new tab called Moldex3D MSH Export displays. |
2. | In the File: field, specify the file path and name to write the MSH file, and click Export. The status of export is shown in the status bar at the bottom. |
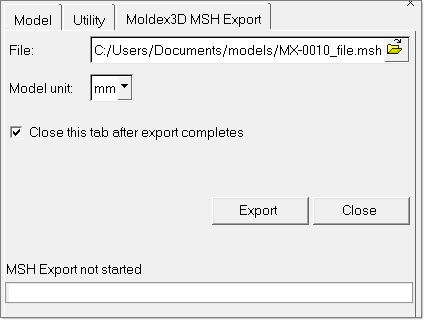
|
1. | Load the exported MSH file in Moldex3D solver. |
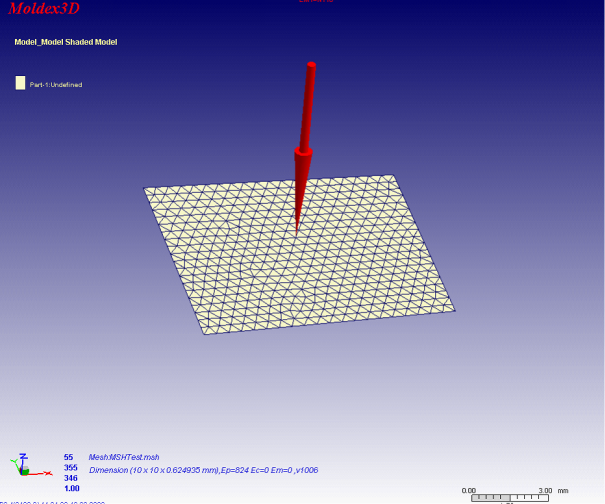
2. | Solve the model and post-process. |
|
Return to Moldex3D Tutorials