Repair and Sew Faces
The Repair and Sew Faces Tool attempts to repair any problems in the faces of the part and then tries to sew them into a solid or sheet part.
The tool will perform the following actions:
- heal the input faces
- pre-process the faces for sewing by identifying and removing those that are invalid due to bad trimming curves
- identify and remove sliver faces from the part
- sew the faces
- post-process the resulting part by sewing up remaining thin gashes
- construct new faces to fill any holes caused by missing geometry that were removed during the pre-processing stage.
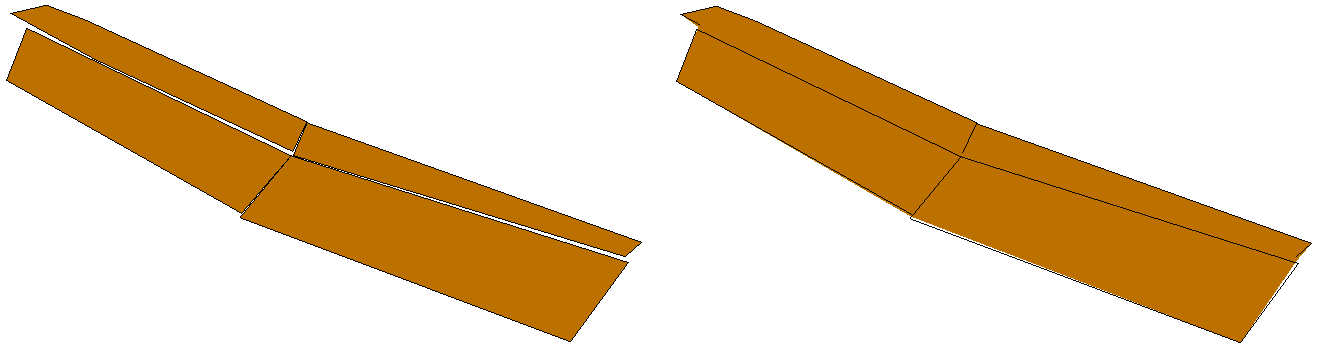
On the Transform tab in the
Repair group, click the Repair and sew faces icon.
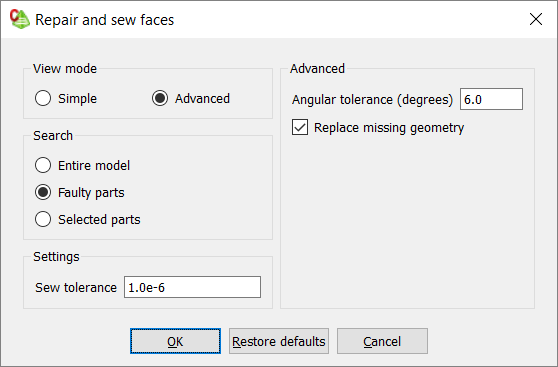
- Sew tolerance
- The supplied tolerance is used as the tolerance when sewing the sheets.
Advanced settings
- Angular tolerance (degrees)
- The tangent change angle in degrees above which G11 discontinuities will be removed by splitting rather than smoothing.
- Replace missing geometry
- The tool attempts to generate surface geometry for faces that will cap holes in the resulting body. If the resultant body has closed circuits of laminar edges that appear to bound a missing face, the tool attempts to generate a surface to span the gap (bounded by the edges) and make a capping face from it.
1
A surface can be composed of several
NURBS surfaces known as patches. These patches should be fitted together in a way that the
boundaries are invisible. This is mathematically expressed by the concept of geometric
continuity. One of the options to establish geometric continuity is by means of Tangential
continuity (G1). It requires the end vectors of two curves or surfaces to be parallel which
eliminates sharp edges.