Frequency Response Process
Setup a frequency response analysis with a series of step-by-step process templates.
These process templates prompt you to enter generic engineering data, and once the data is available, automatically create frequency response analysis loadcases and associated solver cards. The templates share a set of common process steps that are only described the first time they are used.

Figure 1.
Setup a Normal Model Process
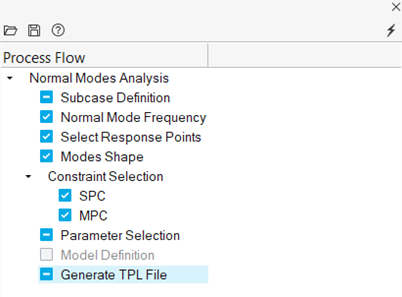
Figure 2.
-
From the NVH Tools ribbon, click the
Normal modes tool.
Figure 3.A normal modes analysis process template is loaded and opens in the Process Flow browser.
-
In the Subcase Definition task, create a new subcase or edit an existing
subcase.
-
Create or edit a subcase.
- To create a new subcase, edit the optional subcase label and click Add.
- To edit an existing subcase, highlight an existing subcase in the list box, edit the optional subcase label and click Update.
- Once input to the task is complete, click Run Task to proceed.
Figure 4. -
Create or edit a subcase.
-
In the Normal Mode Frequency task, define Normal Mode Frequency.
-
Enter normal modes extraction parameters, such as Min. and Max.
frequency, or the number of modes desired.
In most cases, only input for the Max. frequency field is needed. When left blank, the Min. frequency is interpreted as 0 (Hz.), and the No. of modes is however many found between 0 and the Max. frequency. This task gives you separate control over modal extraction in the structural and fluid domains.
- Once input to the task is complete, click Run Task to proceed.
Figure 5. -
Enter normal modes extraction parameters, such as Min. and Max.
frequency, or the number of modes desired.
-
In the Select Response Points task, select response points for output.
- Select a Response type, such as Displacement.
-
Use the Entity selector to select nodes, a node set, or tags to be
included in a particular response set.
You can add or delete multiple response sets from the list using the Add row and Delete row icons to the right of the list.
Figure 6. - Under Output data format, select the complex frequency response data format (real/imaginary or magnitude/phase).
- Under Output file format, select the output file format (h3d, punch, or op2).
- Once all the required responses have been defined, click Run Task to proceed.
Figure 7. -
In the Constraint selection, SPC task, select the boundary condition of the
frequency response analysis.
- You can select existing SPCs by checking the corresponding box under the Active column, or click Create SPC to go to the Constraints panel and define a new SPC.
- Once the boundary condition has been fully defined, click Run Task to proceed.
-
In the Constraint selection, MPC task, select MPC equations to turn on for the
frequency response analysis.
-
Select MPCs.
- NVH user profile: There are two options for managing MPCs, the Analysis Manager and the Process Manager. If you select the Analysis Manager, the Select subcase option and the MPCs list are disabled. If you select the Process Manager, after you select a subcase you can then select existing MPCs by checking the corresponding box under the Active column.
- HyperMesh user profile: The Analysis Manager option is not available, and the MPCs can only be managed through the Process Manager.
- Once the MPC equations have been selected, click Run Task to proceed.
-
Select MPCs.
-
In the Parameter Selection task, select typical solution parameters, such as
title, singular point constraints, and so on.
- Check all boxes under the Active column to activate the desired solution option.
- Once the parameters have been selected, click Run Task and a Process Manager message box pops up informing you that the process has come to an end.
- Click Yes to close the template, or No to review or edit the process steps.
Figure 8. -
In the Generate TPL file task, generate and save the parameters defined in a
standard template file at your selected location.
In the Analysis Manager, the generated template file can be selected as loadcase and solver decks can be exported for normal modes analysis.
Figure 9.
Setup CMS SE Generatin Process
The CMS SE Generation process template helps you generate a CMS SuperElement (SE) modal model from a finite element based model.
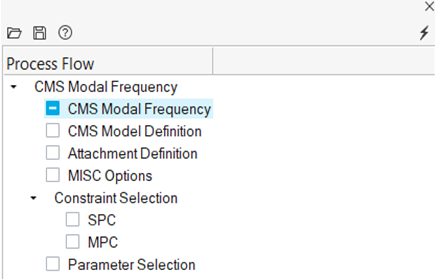
Figure 10.
- From the NVH Tools ribbon, click the arrow next to the Normal modes tool and select CMS SE.
-
In the CMS Modal Frequency step, define the CMS modal frequency.
-
For CMS method, select a type of CMS SE.
- Choose Craig-Bamption (CBN) to create a fixed boundary Craig-Bamption (CBN) CMS superelement.
- Choose GM - general modal method to create a mixed (free-free or fixed) boundary (GM - general modal method) CMS superelement.
-
Define the modes to be included by specifying either the upper
frequency or the number of modes, as well as Spoint starting IDs to be
assigned to the modes.
The Spoint ID fields are auto filled with the first available ID provided by the HyperMesh database. Each mode added to the CMS SE will be assigned a Spoint ID sequentially from the starting ID, and the total number of Spoint IDs actually used will be the same as the number of modes found.
- Fluid modes, as well as fluid-structure coupling matrix can be included in the CMS SE by selecting the Coupled fluid-structure SE checkbox, and providing the above mentioned frequency and Spoint ID definition for the fluid modes.
- Once the task has been completed, click Run Task to proceed.
Figure 11. -
For CMS method, select a type of CMS SE.
-
In the CMS Modal Definition task, specify what recovery information is to be
stored in the CMS SE.
- Select a set of elements, for which the keyword Plotel is a valid specification, or a set of grids.
- To exclude/include rigid elements from the recovery set, select the Rigid checkbox.
- Once the model recovery set has been defined, click Run Task to proceed.
Figure 12. -
In the Attachment Definition task, specify attachment point sets.
- Both fixed and free-free attachments can be specified for a mixed (GM) CMS SE, while only fixed attachments can be specified for a fixed (CBN) CMS SE.
- Once the attachment set has been defined, click Run Task to proceed.
Figure 13. -
In the MISC Options task, specify structural damping and fluid-structure
coupling options.
-
You can specify a global material damping to be assigned to all
structural parts, or select the option of No
damping to avoid adding any damping globally if damping
has been specified at the material level for all components.
Note:
Global modal viscous damping or global fluid damping cannot be stored in a CMS SE, but can be applied in assembly (residual) runs using the CMS SE as a component.
- For fluid-structure coupling, choose Solver auto-search driven by the ACMODL card, or Akusmod which assumes that coupling is provided in a binary file named ftn.70.
Figure 14. -
You can specify a global material damping to be assigned to all
structural parts, or select the option of No
damping to avoid adding any damping globally if damping
has been specified at the material level for all components.
-
In the Parameter Selection task, select typical solution parameters, such as
title, singular point constraints, and so on.
- Check all boxes under the Active column to activate the desired solution option.
- Once the parameters have been selected, click Run Task and an Process Manager message box pops up informing you that the process has come to an end.
- Click Yes to close the template, or No to review or edit the process steps.
Figure 15.
Setup CDS SE Generation Process
Generate a CDS SuperElement (SE) from a finite element based model.
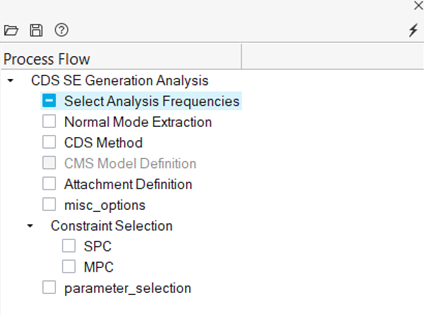
Figure 16.
- From the NVH Tools ribbon, click the arrow next to the Normal modes tool and select CDS SE.
-
In the Select Analysis Frequencies task, enter the frequencies for which
response solution is needed.
-
Define the frequency set.
- To define the min, max, and a linear step, select Frequency range. For Incr type, select Linear and then fill in the required fields.
- To define min, max, and a number of increments with logarithmic spacing, select Frequency range. For Incr type, select Logarithmic and then fill in the required fields.
- To define an arbitrary list of frequencies, select Frequency list and enter a list of arbitrary frequencies.
-
Click Update.
A frequency set entry is created in the list box to the left. You can add additional frequency sets, or delete one from the list using the Add row and Delete row icons to the right of the list.
- Once the frequency set(s) have been defined, click Run Task to proceed.
Figure 17. -
Define the frequency set.
-
In the Normal Mode Extraction task, the default frequencies filled in are based
on the max. frequency you filled in for the previous step.
-
Modify the values based on the specific requirements of the case under
study.
These values are merely the suggested values based on general use cases.
- Click Run Task to proceed.
Figure 18. -
Modify the values based on the specific requirements of the case under
study.
-
In the CDS Method task, define the CDS method.
-
For CDS method, select a type of CDS SE.
Currently only the BME method is available.
- To store transfer functions in CDS superelement, select the Store transfer functions in CDS superelement checkbox.
- To generate a CMS-SE modal model result file after solving, select the Export CMS superelement file checkbox.
- Click Run Task to proceed.
Figure 19. -
For CDS method, select a type of CDS SE.
-
In the CMS Model Definition task, specify which
recovery information is to be stored in the CMS SE.
Restriction: This task is only activated when the Export CMS superelement file checkbox is selected.
- Select a set of elements, for which Plotel is a valid specification, or a set of grids.
- To include or exclude rigid elements from the recovery set, select the Rigid checkbox.
- Once the model recovery set has been defined, click Run Task to proceed.
Figure 20. -
In the Attachment Definition task, specify attachment point sets.
- Both fixed and free-free attachments can be specified for a mixed (GM) CMS SE, while only fixed attachments can be specified for a fixed (CBN) CMS SE.
- Once the attachment set has been defined, click Run Task to proceed.
Figure 21. -
In the MISC Options task, specify structural damping and fluid-structure
coupling options.
-
You can specify a global material damping to be assigned to all
structural parts, or select the option of No
damping to avoid adding any damping globally if damping
has been specified at the material level for all components.
Note:
Global modal viscous damping or global fluid damping cannot be stored in a CMS SE, but can be applied in assembly (residual) runs using the CMS SE as a component.
- For fluid-structure coupling, choose Solver auto-search driven by the ACMODL card, or Akusmod which assumes that coupling is provided in a binary file named ftn.70.
Figure 22. -
You can specify a global material damping to be assigned to all
structural parts, or select the option of No
damping to avoid adding any damping globally if damping
has been specified at the material level for all components.
-
In the Parameter Selection task, select typical solution parameters, such as
title, singular point constraints, and so on.
- Check all boxes under the Active column to activate the desired solution option.
- Once the parameters have been selected, click Run Task and an Process Manager message box pops up informing you that the process has come to an end.
- Click Yes to close the template, or No to review or edit the process steps.
Figure 23.
Setup Unit Input Frequency Response Process
Set up subcases with unit inputs. In practice, this is common to generate vibration and noise sensitivity results.
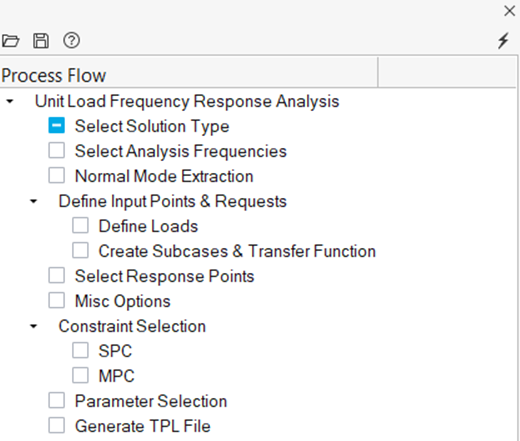
Figure 24.
- From the NVH Tools ribbon, click the arrow next to the Normal modes tool and select Unit input frequency response.
-
In the Select Solution Type task, select a solution method.
- Select either the Direct Frequency Response solution method, or the Modal Frequency Response solution method. For large problems involving more than a few frequencies, the modal solution is typically the most efficient solution.
- Click Run Task to proceed.
-
In the Select Analysis Frequencies task, enter the frequencies for which
response solution is needed.
-
Define the frequency set.
- To define the min, max, and a linear step, select Frequency range. For Incr type, select Linear and then fill in the required fields.
- To define min, max, and a number of increments with logarithmic spacing, select Frequency range. For Incr type, select Logarithmic and then fill in the required fields.
- To define an arbitrary list of frequencies, select Frequency list and enter a list of arbitrary frequencies.
-
Click Update.
A frequency set entry is created in the list box to the left. You can add additional frequency sets, or delete one from the list using the Add row and Delete row icons to the right of the list.
- Once the frequency set(s) have been defined, click Run Task to proceed.
Figure 25. -
Define the frequency set.
-
In the Normal Mode Extraction task, the default frequencies filled in are based
on the max. frequency you filled in for the previous step.
-
Modify the values based on the specific requirements of the case under
study.
These values are merely the suggested values based on general use cases.
- Click Run Task to proceed.
Figure 26. -
Modify the values based on the specific requirements of the case under
study.
-
In the Define Input Points & Requests, Define Loads task, define what type
of load is applied.
The first four types are only applicable for structural nodes, and the last one for fluid nodes.
- For Load type, select Force, Enforced motion (displacement, velocity, or acceleration), or Acoustic source.
-
Use the Nodes selector to select nodes, a node set, or tags in the
modeling window, then click
Add.
The table on the left hand side is populated with additional degree of freedom (DOF) checkboxes.
-
You can make a single or multiple row selection within the table, and
then right-click to access the DOF row selection options. Alternatively,
make a single or multiple row selection within the table, and then
right-click to access the column selection options.
All selected DOFs will be checked to indicate locations and directions where unit input are to be applied.
-
Click
Run Task to proceed.
One loadcase will be created for each DOF indicated.
Figure 27. -
In the Define Input Points & Requests, Create Subcases & Transfer
Function task, select to output transfer function between input points.
Of particular interest are driving point (response taken at the same point as input) transfer functions, which are commonly used as a measure for local dynamic stiffness, or full matrix (all possible pairs of input point combinations) output, which is sometimes used as input for FRF based substructuring analysis.
It is also possible to create new subcase groups of input to be used in individual subcases. New subcase groups can be added by clicking the Add Group icon. You can make a single or multiple row selections within the table, and then select the newly created Subcase group and click Update. All input dofs belonging to one subcase group will be used as simultaneous excitations in one subcase.
Figure 28. -
In the Select Response Points task, select response points for output.
- Select a Response type, such as Displacement.
-
Use the Entity selector to select nodes, a node set, or tags to be
included in a particular response set.
You can add or delete multiple response sets from the list using the Add row and Delete row icons to the right of the list.
Figure 29. - Under Output data format, select the complex frequency response data format (real/imaginary or magnitude/phase).
- Under Output file format, select the output file format (h3d, punch, or op2).
- Once all the required responses have been defined, click Run Task to proceed.
Figure 30. -
In the Misc Options task, select from the damping options that are available,
including the global modal viscous damping on the structure side, and global
material and viscous damping on the fluid side.
Figure 31. -
In the Constraint selection, SPC task, select the boundary condition of the
frequency response analysis.
- You can select existing SPCs by checking the corresponding box under the Active column, or click Create SPC to go to the Constraints panel and define a new SPC.
- Once the boundary condition has been fully defined, click Run Task to proceed.
Figure 32. -
In the Constraint selection, MPC task, select MPC equations to turn on for the
frequency response analysis.
- Select existing MPCs by checking the corresponding box under the Active column.
- Once the MPC equations have been selected, click Run Task to proceed.
-
In the Parameter Selection task, select typical solution parameters, such as
title, singular point constraints, and so on.
- Check all boxes under the Active column to activate the desired solution option.
- Once the parameters have been selected, click Run Task and an Process Manager message box pops up informing you that the process has come to an end.
- Click Yes to close the template, or No to review or edit the process steps.
Figure 33. -
In the Generate TPL file task, generate and save the parameters defined in a
standard template file at your selected location.
- Choose Full deck TPL to access the file that has
all of the parameters for the complete unit load FRF process manager. In the
Analysis Manager, the generated template file can be selected as loadcase
for the Solution type Full deck TPL and solver decks can be exported for the
unit FRF.
Figure 34. - Choose Loads Only TPL to access the file that
contains only the parameters for the loadcase portion of the unit load FRF
process manager. In the Analysis Manager, the generated template file can be
selected as the loadcase for the Solution type Frequency Response and solver
decks can be exported for general FRF.
Figure 35.
- Choose Full deck TPL to access the file that has
all of the parameters for the complete unit load FRF process manager. In the
Analysis Manager, the generated template file can be selected as loadcase
for the Solution type Full deck TPL and solver decks can be exported for the
unit FRF.
Setup Random PSD Frequency Response Process
Perform random frequency response analysis.
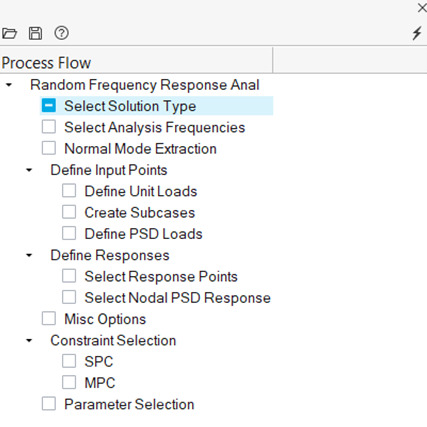
Figure 36.
- From the NVH Tools ribbon, click the arrow next to the Normal modes tool and select Random PSD frequency response.
-
In the Select Solution Type task, select a solution method.
- Select either the Direct Frequency Response solution method, or the Modal Frequency Response solution method. For large problems involving more than a few frequencies, the modal solution is typically the most efficient solution.
- Click Run Task to proceed.
-
In the Select Analysis Frequencies task, enter the frequencies for which
response solution is needed.
-
Define the frequency set.
- To define the min, max, and a linear step, select Frequency range. For Incr type, select Linear and then fill in the required fields.
- To define min, max, and a number of increments with logarithmic spacing, select Frequency range. For Incr type, select Logarithmic and then fill in the required fields.
- To define an arbitrary list of frequencies, select Frequency list and enter a list of arbitrary frequencies.
-
Click Update.
A frequency set entry is created in the list box to the left. You can add additional frequency sets, or delete one from the list using the Add row and Delete row icons to the right of the list.
- Once the frequency set(s) have been defined, click Run Task to proceed.
Figure 37. -
Define the frequency set.
-
In the Normal Mode Extraction task, the default frequencies filled in are based
on the max. frequency you filled in for the previous step.
-
Modify the values based on the specific requirements of the case under
study.
These values are merely the suggested values based on general use cases.
- Click Run Task to proceed.
Figure 38. -
Modify the values based on the specific requirements of the case under
study.
-
In the Define Input Points, Define Unit Loads task, define what type of load is
applied.
The first four types are only applicable for structural nodes, and the last one for fluid nodes.
- For Load type, select Force, Enforced motion (displacement, velocity, or acceleration), or Acoustic source.
-
Use the Nodes selector to select nodes, a node set, or tags in the
graphics window, then click Add.
The table on the left hand side is populated with additional degree of freedom (DOF) checkboxes.
-
You can make a single or multiple row selection within the table, and
then right-click to access the DOF row selection options. Alternatively,
make a single or multiple row selection within the table, and then
right-click to access the column selection options.
All selected DOFs will be checked to indicate locations and directions where unit input are to be applied.
-
Click
Run Task to proceed.
One loadcase will be created for each DOF indicated.
Figure 39. -
In the Define Input Points, Create Subcases task, select to output transfer
function between input points.
Of particular interest are driving point (response taken at the same point as input) transfer functions, which are commonly used as a measure for local dynamic stiffness, or full matrix (all possible pairs of input point combinations) output, which is sometimes used as input for FRF based substructuring analysis.
It is also possible to create new subcase groups of input to be used in individual subcases. New subcase groups can be added by clicking the Add Group icon. You can make a single or multiple row selections within the table, and then select the newly created Subcase group and click Update. All input dofs belonging to one subcase group will be used as simultaneous excitations in one subcase.
Figure 40. -
In the Define Input Points, Define PSD Loads task, input the NxN 2 dimensional
PSD matrix (here N is the number of subcases whose response are used in the
random PSD calculations.
- The diagonal cells are used to define auto PSD terms, and the off diagonal cells are used to define cross PSD terms. For cross PSD, only the bottom triangle of the matrix needs to be defined. To input a PSD term, click one of the cells, and then specify the real and imaginary scaling factor and the frequency table.
-
Once the PSD matrix input is
completed, click Run Task to
proceed.
Figure 41.
-
In the Define Responses, Select Response Points task, select response points
for output.
- Select a Response type, such as Displacement.
-
Use the Entity selector to select nodes, a node set, or tags to be
included in a particular response set.
You can add or delete multiple response sets from the list using the Add row and Delete row icons to the right of the list.
Figure 42. - Under Output data format, select the complex frequency response data format (real/imaginary or magnitude/phase).
- Under Output file format, select the output file format (h3d, punch, or op2).
- Once all the required responses have been defined, click Run Task to proceed.
Figure 43. -
In the Define Responses, Select Nodal PSD Response task, define the response
points and DOFs to be output.
Response points and DOFs can be output into the following formatted files: XYPUNCH, XYPLOT, and XYPEAK.
-
Select a response type and then select nodes, set of nodes, or tags,
and then click Add.
The list box is populated to allow you to further the selection to a set of DOFs.
Figure 44. -
For each DOF, select the output formats.
Figure 45. - Once the PSD response selection is completed, click Run Task to proceed.
-
Select a response type and then select nodes, set of nodes, or tags,
and then click Add.
-
In the Misc Options task, select from the damping options that are available,
including the global modal viscous damping on the structure side, and global
material and viscous damping on the fluid side.
Figure 46. -
In the Constraint selection, SPC task, select the boundary condition of the
frequency response analysis.
- You can select existing SPCs by checking the corresponding box under the Active column, or click Create SPC to go to the Constraints panel and define a new SPC.
- Once the boundary condition has been fully defined, click Run Task to proceed.
Figure 47. -
In the Constraint selection, MPC task, select MPC equations to turn on for the
frequency response analysis.
- Select existing MPCs by checking the corresponding box under the Active column.
- Once the MPC equations have been selected, click Run Task to proceed.
-
In the Parameter Selection task, select typical solution parameters, such as
title, singular point constraints, and so on.
- Check all boxes under the Active column to activate the desired solution option.
- Once the parameters have been selected, click Run Task and an Process Manager message box pops up informing you that the process has come to an end.
- Click Yes to close the template, or No to review or edit the process steps.
Figure 48.
Setup General Frequency Response Process
Run Task loads at multiple DOFs simultaneously with arbitrary magnitude and delay (relative phase).
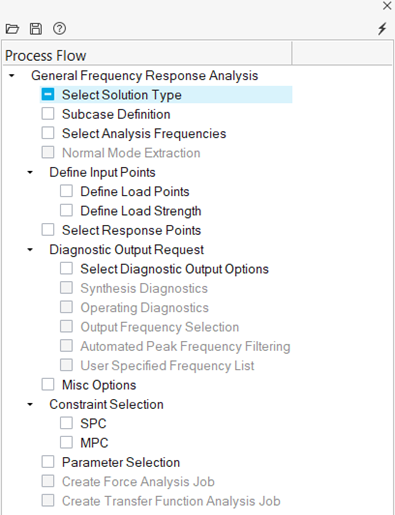
Figure 49.
- From the NVH Tools ribbon, click the arrow next to the Normal modes tool and select General frequency response.
-
In the Select Solution Type task, select a solution method.
- Select either the Direct Frequency Response solution method, or the Modal Frequency Response solution method. For large problems involving more than a few frequencies, the modal solution is typically the most efficient solution.
- Click Run Task to proceed.
-
In the Subcase Definition task, create a new subcase or edit an existing
subcase.
-
Create or edit a subcase.
- To create a new subcase, edit the optional subcase label and click Add.
- To edit an existing subcase, highlight an existing subcase in the list box, edit the optional subcase label and click Update.
- Once input to the task is complete, click Run Task to proceed.
Figure 50. -
Create or edit a subcase.
-
In the Select Analysis Frequencies task, enter the frequencies for which
response solution is needed.
-
Define the frequency set.
- To define the min, max, and a linear step, select Frequency range. For Incr type, select Linear and then fill in the required fields.
- To define min, max, and a number of increments with logarithmic spacing, select Frequency range. For Incr type, select Logarithmic and then fill in the required fields.
- To define an arbitrary list of frequencies, select Frequency list and enter a list of arbitrary frequencies.
-
Click Update.
A frequency set entry is created in the list box to the left. You can add additional frequency sets, or delete one from the list using the Add row and Delete row icons to the right of the list.
- Once the frequency set(s) have been defined, click Run Task to proceed.
Figure 51. -
Define the frequency set.
-
In the Normal Mode Extraction task, the default frequencies filled in are based
on the max. frequency you filled in for the previous step.
-
Modify the values based on the specific requirements of the case under
study.
These values are merely the suggested values based on general use cases.
- Click Run Task to proceed.
Figure 52. -
Modify the values based on the specific requirements of the case under
study.
-
In the Define Input Points, Define Load Points task, define what type of load
is applied.
The first four types are only applicable for structural nodes, and the last one for fluid nodes.
- For Load type, select Force, Enforced motion (displacement, velocity, or acceleration), or Acoustic source.
-
Use the Nodes selector to select nodes, a node set, or tags in the
modeling window, then click
Add.
The table on the left hand side is populated with additional degree of freedom (DOF) checkboxes.
-
You can make a single or multiple row selection within the table, and
then right-click to access the DOF row selection options. Alternatively,
make a single or multiple row selection within the table, and then
right-click to access the column selection options.
All selected DOFs will be checked to indicate locations and directions where unit input are to be applied.
-
Click Run
Task to proceed.
One loadcase will be created for each DOF indicated.
Figure 53. -
In the Define Input Points, Define Load Strength task, define frequency
dependent load strength and delay for individual subcases or DOFs in one
subcase.
- For subcase based definition, once the subcase is selected, select a DOF
row from the list box, and then add load strength frequency tables in either
real/imaginary or magnitude/phase form.Delay or phase relative to a reference input DOF can optionally be specified as well. Loading strength can be defined manually, with external files in csv/text format and also universal (.unv) files from external data acquisition tools such as LMS and B&K. Import the .csv/text or universal file, select the relevant loading strength and click Save to define it. You can select one of the radio buttons on the right to control how the definitions provided are filled into various rows. It is also possible to go back to the Subcase Definition panel by clicking the Create Subcase icon to add new subcases or edit existing subcases. If subcases are added or edited, then you will be redirected to the Select Analysis Frequencies task to repeat all the steps prior to defining load strengths. If subcases are not edited then you will come back to the Define Load Strength task.
Figure 54. - For DOF based definition, once the DOF is selected, select a subcase row
from the list and follow the same process described in the above section.
With this option it is not possible to add or edit subcases.
Figure 55.
- For subcase based definition, once the subcase is selected, select a DOF
row from the list box, and then add load strength frequency tables in either
real/imaginary or magnitude/phase form.
-
In the Select Response Points task, select response points for output.
Response selection can be global or subcase specific.
-
Select a Response type, such as Displacement.
Figure 56. -
Use the Entity selector to select nodes, a node set, or tags to be
included in a particular response set.
You can add or delete multiple response sets from the list using the Add row and Delete row icons to the right of the list.
Figure 57. - Under Output data format, select the complex frequency response data format (real/imaginary or magnitude/phase).
- Under Output file format, select the output file format (h3d, punch, or op2).
- Once all the required responses have been defined, click Run Task to proceed.
Responses selected for the global subcase are by default available for other individual subcases. Additional responses can be added and used for an individual subcase. It is also possible to add duplicate response types to any individual subcase, in addition to those in the global subcase. In this case a separate response set will be created for that subcase which will be a union of entities in global and individual subcases.
Figure 58. -
Select a Response type, such as Displacement.
-
In the Diagnostic Output Request, Select Diagnostic Output Options task,
control if diagnostic outputs are to be generated.
- Select No to generate diagnostic output requests and the process will go directly to the Miscellaneous Options task. Select Yes to request diagnostic output only at selected response peaks.
- Click Run Task to proceed.
Figure 59. -
In the Select Diagnostic Output Request, Synthesis Diagnostics task, select the
Synthesis diagnostic type which presents a breakdown (participation factors) to
the response, such as modal participations.
This type will be output only at the peak frequencies of the corresponding response DOF. The selection of the Synthesis diagnostic type can be Global or Subcase Specific.
- First select the subcase, either Global or Individual Subcase.
-
Select response DOFs by clicking Response
points.
In a case of individual subcases the list of responses will be a union of response entities for Global and Individual Subcase. There is a specific option of Attachment points on control volume in Auto TPA and Traditional TPA. In Auto TPA you can select a connection node set. The elements attached to connection nodes are automatically segregated into Non-Rigid Element set (CONEL) and Rigid Element set (CONREL) based on the element type. In Traditional TPA, you can create a node set at which attachment forces are to be calculated in the assembled state.
Figure 60.
Figure 61. -
Click Run
Task to invoke the Create Transfer Function
Analysis Job task.
This will delete all the created entities, and entities related to unit transfer functions are created. This allows you to export the solver deck or submit a job related to the second step of TPA for calculating transfer function in Control Volume through the Analysis Manager.
Figure 62.
-
In the Select Diagnostic Output Request, Operating Diagnostics task, select the
Operating diagnostic type which is not response specific, such as ODS animation
or energy.
Output in this case will be generated at the super set of the peak frequencies of all selected response DOFs. In this case the selection of operating diagnostic type can be global or subcase specific.
Figure 63. -
In the Select Diagnostic Output Request, Output Frequency Selection task,
control to select frequency at which diagnostic output is to be requested.
- Select Automated Peak Frequency Filtering to customize options used to define response peak frequencies through the PEAKOUT card.
- Select User Specified Frequency List to enter a list of frequencies for each subcase, which will be referenced by a OFREQ card in a separate diagnostic output subcase.
-
In the Select Diagnostic Output Request, Automated Peak Frequency Filtering
task, select the customized options specific for structural and acoustic
responses to be used for selected response peak frequencies.
-
Select customized options.
Frequency selection for this option can also be global or subcase specific. The PEAKOUT card specified for the Global subcase is also used for those subcases for which a separate PEAKOUT card is not specified. For those subcases where specific peak frequency selection control is needed, a separate PEAKOUT card should be specified with appropriate parameters.
Figure 64. -
Specify a single threshold value or a frequency table.
Only peaks above the threshold are retained in the search process as candidates.
-
Specify the number of peaks (default =5) per response DOF to be kept in
the peak frequency set.
Figure 65.
-
Select customized options.
-
In the Select Diagnostic Output Request, User Specified Frequency List task,
specify a list of frequencies at which diagnostic output is requested.
This definition is subcase specific. For subcases where a Frequency List is entered in the Select Analysis Frequencies task, the same frequency list values are automatically entered by default.
Figure 66. -
In the Misc Options task, select from the damping options that are available,
including the global modal viscous damping on the structure side, and global
material and viscous damping on the fluid side.
Figure 67. -
In the Constraint selection, SPC task, select the boundary condition of the
frequency response analysis.
- You can select existing SPCs by checking the corresponding box under the Active column, or click Create SPC to go to the Constraints panel and define a new SPC.
- Once the boundary condition has been fully defined, click Run Task to proceed.
Figure 68. -
In the Constraint selection, MPC task, select MPC equations to turn on for the
frequency response analysis.
- Select existing MPCs by checking the corresponding box under the Active column.
- Once the MPC equations have been selected, click Run Task to proceed.
-
In the Parameter Selection task, select typical solution parameters, such as
title, singular point constraints, and so on.
- Check all boxes under the Active column to activate the desired solution option.
- Once the parameters have been selected, click Run Task and an Process Manager message box pops up informing you that the process has come to an end.
- Click Yes to close the template, or No to review or edit the process steps.
Figure 69.