Flux e-Machine Toolbox: Coupling component
Introduction
To achieve a Flux e-Machine Toolbox coupling, it is necessary to generate a coupling component from the modeled Flux project previously prepared. There are several prerequisites to respect in the construction of the Flux project to ensure this coupling.
Preparation of the Flux project
Here are the prerequisites:
- Coupling available only in transient magnetic with 3-Phase circuit.
- I/O parameter piloted by a scenario, called SPEED and used in mechanical set in rotation with imposed speed.
- I/O parameter defined by formula, called POS_INI and used in mechanical set in rotation for the time position t=0s.
- A parameter with geometric type for the definition of the pole number.
- No need to define a solving scenario, Flux e-Machine Toolbox will do it automatically when running a test.
- For the Iron losses computation, it is mandatory to use non conducting
laminated magnetic regions for the Rotor and the Stator (valid for 2D and 3D
and for Skew since FeMT 2021).Note: For FeMT versions prior to 2021, in Skew, the non conducting laminated magnetic regions were not available. It was advised to use non conducting magnetic regions.
- For the Iron Losses computation, it is highly recommended to define a material with losses model, assigned to non conducting laminated magnetic regions.
- It is mandatory to define in the application the transient initialization option to initialized by static computation in order to be able to compute the losses directly on the first period and to limit the number of steps to compute.
- Since FeMT 2021, designs where the section represented in Flux contains
multiple magnetic poles are supported. You can represent all types of
machines, and in particular the fractional slot winding machines which have
different periodicities in the stator winding and in the rotor.Warning: There is a limitation in 3D and in Skew: At the present time, it is not possible to represent a complete machine, at least one periodicity is required.Note: For FeMT versions prior to 2021, there was a limitation: only one magnetic pole section had to be represented. All the information had to be contained in one pole pitch.
Coupling component
The coupling component is necessary to ensure the transfer of information of the Flux project to Flux e-Machine Toolbox. This component is a file *.FEMT.
To access the generation of the coupling component, click on the menu Solving and click on Generate component for Flux e-Machine Toolbox coupling:
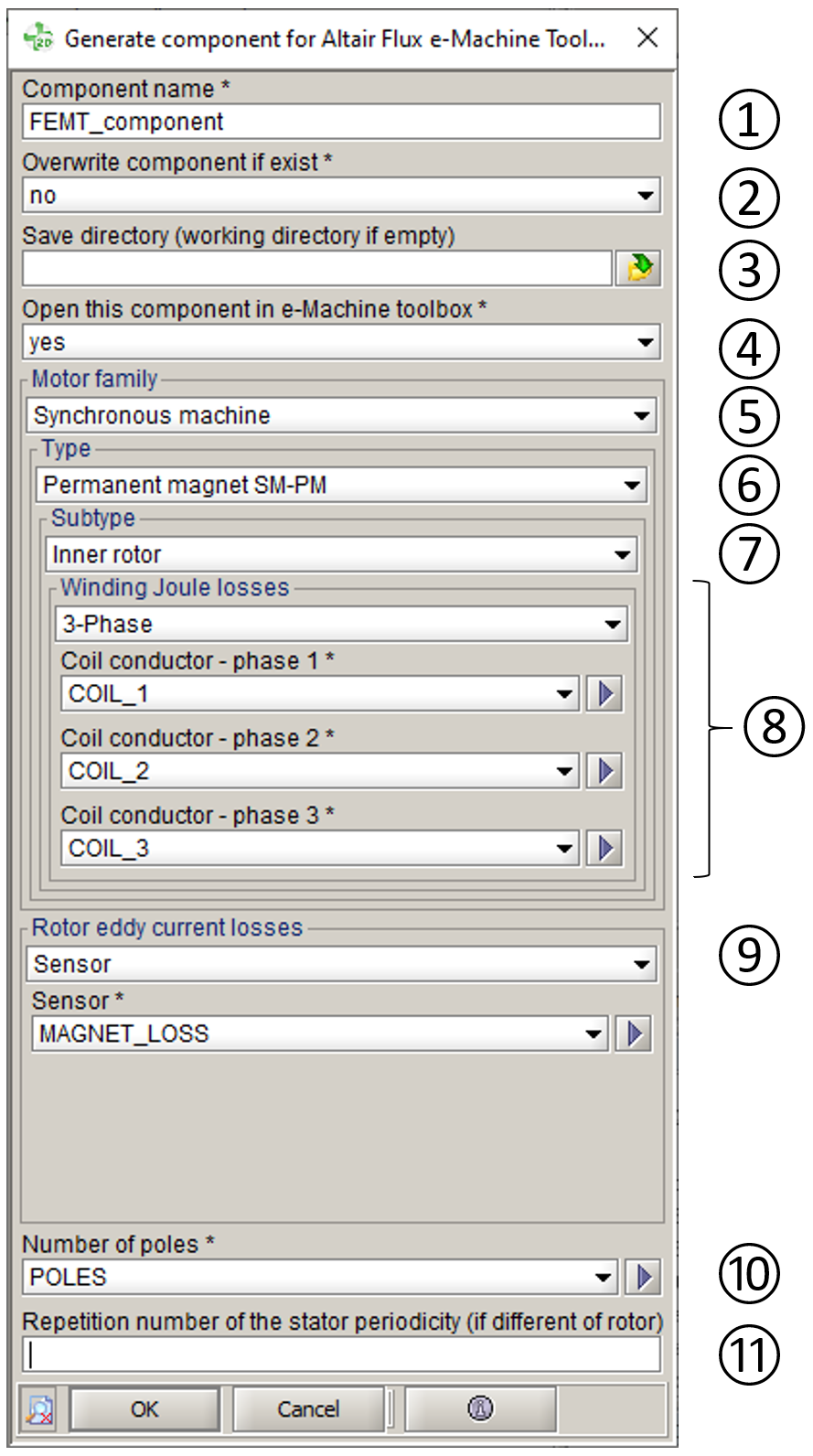
- Name of the component saved in a directory Name_of_the_component.FEMT
- Overwrite or not the component if it already exists
- Save directory of the component (by default it's the current working directory)
- Choice to launch or not Flux e-Machine Toolbox after the generation of the component and open the generated component
- Motor family (only one available for the moment, Synchronous machine)
- Motor type (only one available for the moment, Permanent magnet SM-PM)
- Motor Sub-type (Outer rotor or Inner rotor)
- Information needed to compute stator winding Joule losses
- Number of phases (3 phases only available for the moment)
- The coil conductor of each phase
- Information needed to compute Rotor Eddy current losses
- Either a previously defined sensor, which computes Eddy current losses on magnet rotor regions
- Or the list of regions on which the rotor Eddy current losses must be computed (a sensor will be created automatically)
- Or the list of solid conductors on which the rotor Eddy current losses must be computed
- Number of poles of the electrical machine (a geometric parameter is mandatory)
- Repetition number of the stator periodicity (if it is different from the rotor one)
Generated files
By generating the XXX.FEMT coupling component a XXX.FEMT directory is created in which there are:
- The saved Flux project project.FLU
- A directory tests in which tests run in Flux e-Machine Toolbox will be stored
- A file config.xml that contains all the information needed for the computation of perfomance mapping of the studied machine