/FAIL/BIQUAD
In Radioss, /FAIL/BIQUAD is the most user-friendly failure model for ductile materials. It uses a simplified, nonlinear strain-based failure criteria with linear damage accumulation.
The failure strain is described by two parabolic functions calculated using curve fitting from up to 5 user input failure strains.
- aa , bb , cc , dd , ee , and ff
- Parabolic coefficients
- xx
- Stress triaxiality
- f1(x)f1(x) and f2(x)f2(x)
- Plastic failure strain
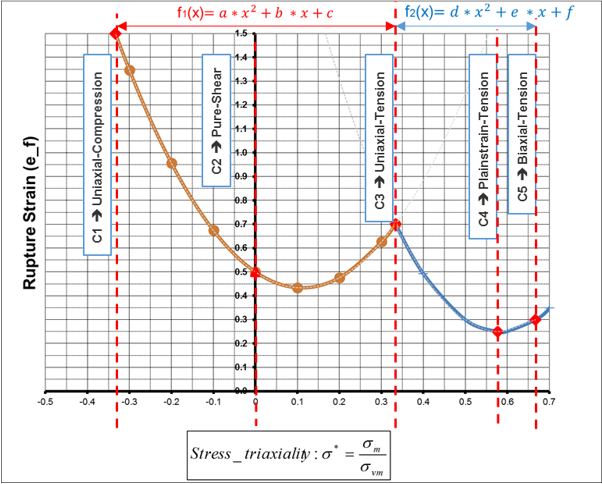
Bi-Quadratic FAILURE
--------------------
c1. . . . . . . . . . . . . . . . . . .= 0.2419E+00
c2. . . . . . . . . . . . . . . . . . .= 0.1900E+00
c3. . . . . . . . . . . . . . . . . . .= 0.1585E+00
c4. . . . . . . . . . . . . . . . . . .= 0.1437E+00
c5. . . . . . . . . . . . . . . . . . .= 0.1394E+00
COEFFICIENTS OF FIRST PARABOLA
-----------------------------
a . . . . . . . . . . . . . . . . . . .= 0.9180E-01
b . . . . . . . . . . . . . . . . . . .= -0.1251E+00
c . . . . . . . . . . . . . . . . . . .= 0.1900E+00
COEFFICIENTS OF SECOND PARABOLA
-----------------------------
d . . . . . . . . . . . . . . . . . . .= 0.3753E-01
e . . . . . . . . . . . . . . . . . . .= -0.9483E-01
f . . . . . . . . . . . . . . . . . . .= 0.1859E+00
- c1
- Plastic failure strain in uniaxial compression
- c2
- Plastic failure strain in shear
- c3
- Plastic failure strain in uniaxial tension
- c4
- Plastic failure strain in plane strain tension
- c5
- Plastic failure strain in biaxial tension
M-Flag Input Options
- M-Flag=0, User-defined Test Data
For this case, you must enter c1-c5 which represents the plastic failure strain for the 5 different stress states. Ideally this data would be obtained from test or the material supplier.
- M-Flag=1-7, Predefined
Material DataIf failure strain data is not available, you can pick from 7 predefined materials. Figure 2 shows the plastic strain at failure curves for the 7 materials.Note: The predefined values are supplied for early design exploration and it is your responsibility to verify that their material has the same properties.Figure 2. Predefined Material Failure Curves
- M-Flag=99, Plastic Failure Strain Ratio
Input, r1-r5The last input method is to enter the plastic failure strain in uniaxial tension, c3, and plastic failure strain ratios for the other four stress states. These ratios are defined as:
- r1
- Failure plastic strain ratio, Uniaxial Compression (c1) to Uniaxial Tension (c3), so c1=r1⋅c3c1=r1⋅c3
- r2
- Failure plastic strain ratio, Pure Shear (c2) to Uniaxial Tension (c3), so c2=r2⋅c3c2=r2⋅c3
- r4
- Failure plastic strain ratio, Plane Strain Tension (c4) to Uniaxial Tension (c3), so c4=r4⋅c3c4=r4⋅c3
- r5
- Failure plastic strain ratio, Biaxial Tension (c5) to Uniaxial Tension (c3), so c5=r5⋅c3c5=r5⋅c3
Using this method, it is easy to change the failure curve by adjusting the single plastic failure strain in uniaxial tension value, c3.Figure 3. Changes in Plastic Failure Strain Curve. by increasing the uniaxial tension failure, c3, with the same failure plastic strain ratios
Default Behavior
- In case the material failure behavior is unknown, c1 to c5 are set to 0.0 and the mild steel behavior (M-Flag=1) is used.
- If only the tensile failure value is known, c3 is defined ( c1=c2=c4=c5=0.0c1=c2=c4=c5=0.0 ). The mild steel behavior is used and scaled by the user-defined c3 value.
- In case the material behavior is known, M-Flag is defined and c3 can be used to adjust the failure model according to the expected tensile failure. The selected material behavior is scaled by the user-defined c3 value.
- For all other cases, all c1 to c5 are intended to be defined and default value of 0.0 is used.
Element Failure Treatment
- DD
- Damage
- ΔεpΔεp
- The change in plastic strain of the integration point
- εfεf
- Plastic failure strain for the current stress triaxiality
In shell elements after an integration point reaches D=1D=1 , the integration point’s stress tensor is set to zero. The element fails and is deleted when the ratio of through thickness failed integration points equals P_thickfail. In solid elements, the element is deleted when any integration point reaches D=1D=1 .
Plane Strain as Global Minimum
The S-Flag=2 option can be used to force the global minimum of the plastic failure strain curve to occur at the plane strain stress triaxiality location, c4. This is accomplished by splitting the second equation into 2 separate quadratic sub-functions.
Modeling Material Instability (Localized Necking)
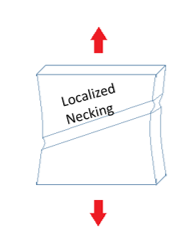
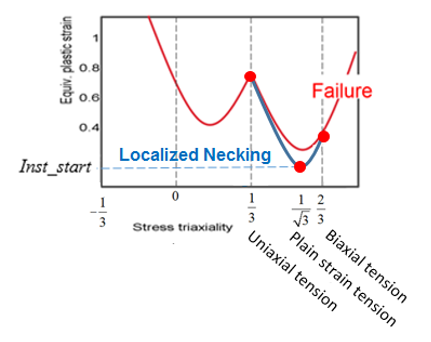
When using S-Flag=1 or 2, the damage accumulation begins once the plastic strain reaches in failure curve (red in Figure 6).
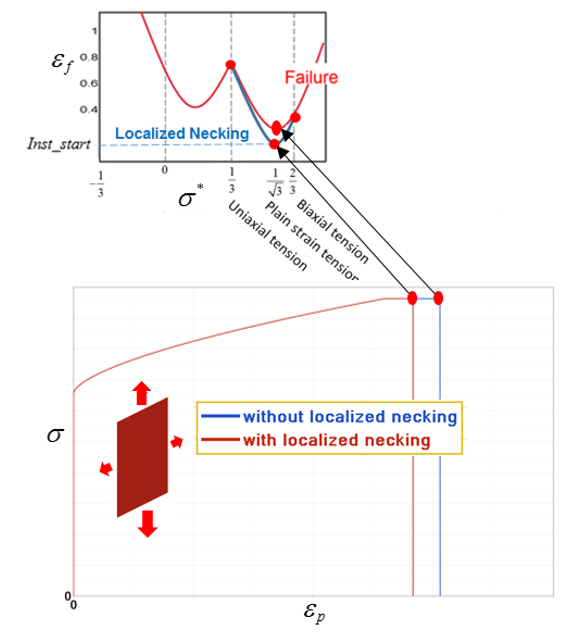
Perturbation of the Failure Limit
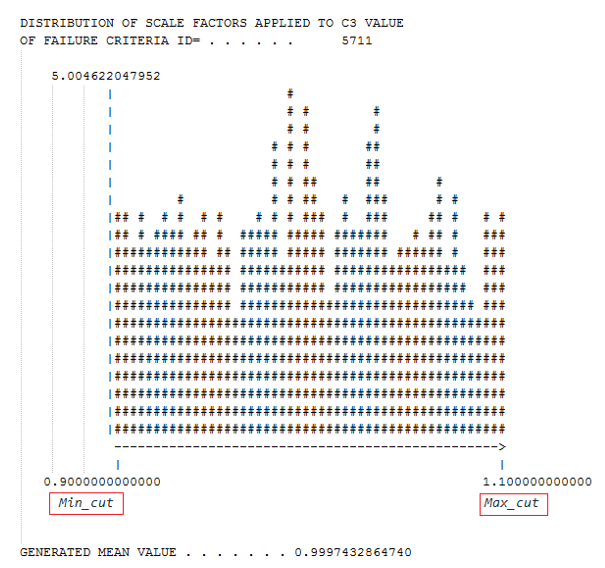
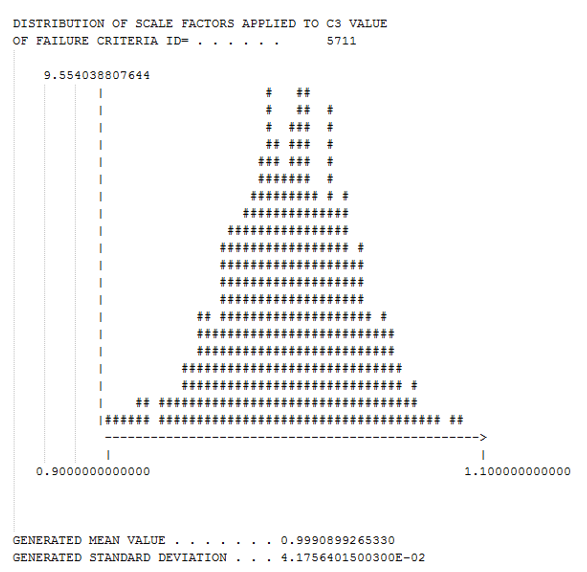
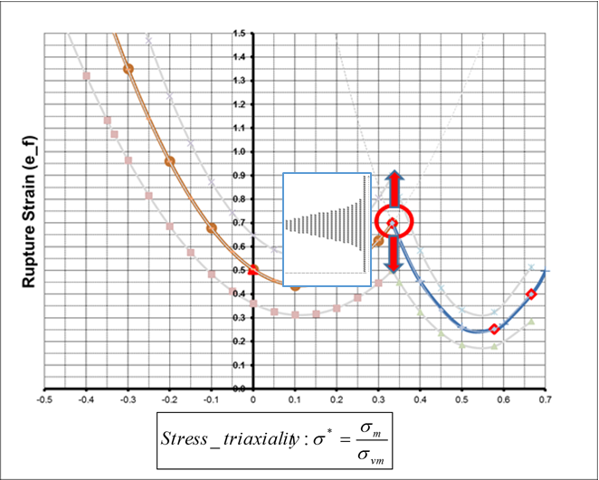