One Degree of Freedom Spring Elements (TYPE4)
- Spring only
- Dashpot (damper) only
- Spring and dashpot in parallel
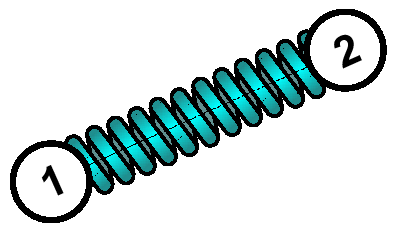
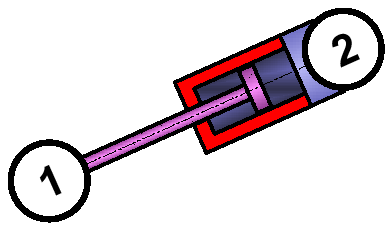
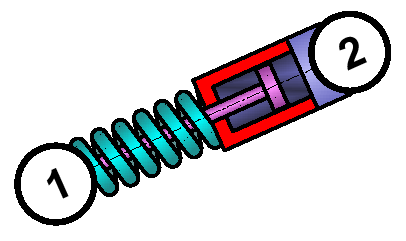
No material data card is required for spring elements. However, the stiffness and equivalent viscous damping coefficient are required. The mass is required if there is any spring translation.
- Linear Stiffness
- Nonlinear Stiffness
- Nonlinear Elasto-Plastic Stiffness
- Linear
- Nonlinear
A spring may also have zero length. However, a one DOF spring must have 2 nodes.
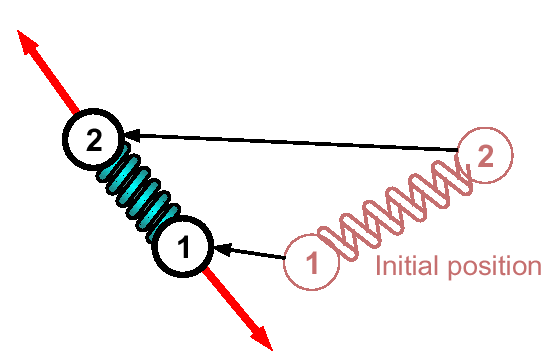
Time Step
The time of a spring element depends on the values of stiffness, damping and mass.
The critical time step ensures that the stability of the explicit time integration is maintained, but it does not ensure high accuracy of spring vibration behavior. Only two time steps are required during one vibration period of a free spring to keep stability. However, if true sinusoidal reproduction is desired, the time step should be reduced by a factor of at least 5.
If the spring is used to connect the two parts, the spring vibration period increases and the default spring time step ensures stability and accuracy.
Linear Spring
Function number defining .
N1=0
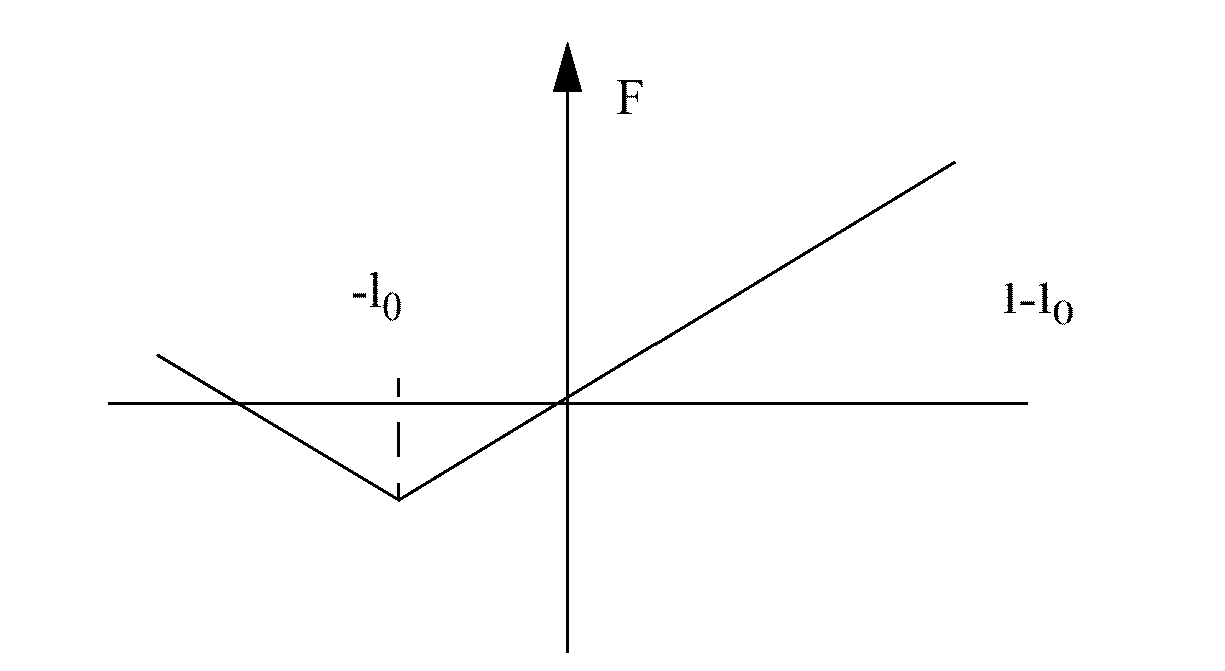
Nonlinear Elastic Spring
Hardening flag
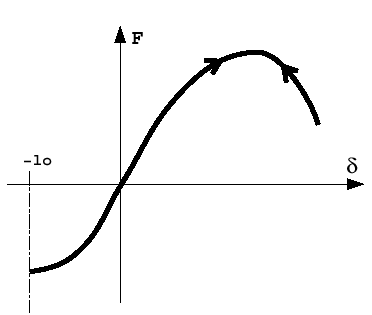
Nonlinear Elasto-plastic Spring: Isotropic Hardening
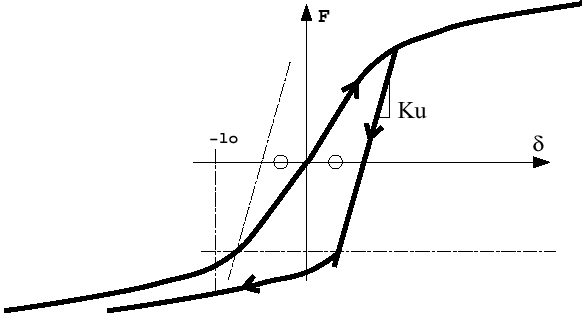
Nonlinear Elasto-plastic Spring: Decoupled Hardening
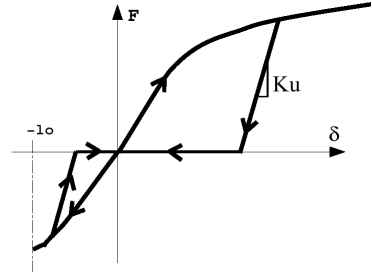
Nonlinear Elasto-plastic Spring: Kinematic Hardening
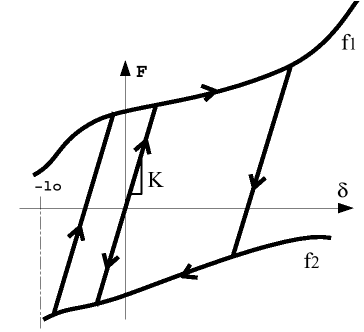
Nonlinear Elasto-plastic Spring: Nonlinear Unloading
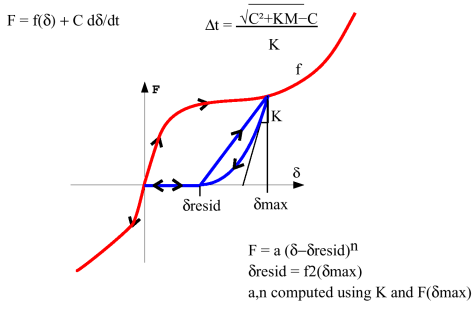
Nonlinear Dashpot
- Mass, .
- A function defining the change in force with respect to the spring displacement. This must
be equal to unity:
- A function defining the change in force with spring displacement rate,
- The hardening flag in the input must be set to zero.
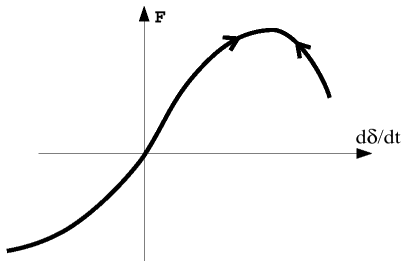
Nonlinear Viscoelastic Spring
- Mass,
- Equivalent viscous damping coefficient
- A function defining the change in force with spring displacement
- A function defining the change in force with spring displacement rate
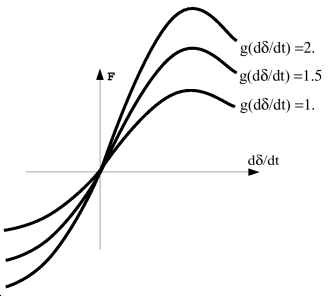