Engine Error Messages
MASS OR ENERGY ERROR DUE TO CONTACT
**WARNING MINIMUM TIME STEP 0.248E-04 IN INTERFACE 11(DTMIN= 0.2500E-04)
REMOVED SECONDARY NODE 63086879 FROM INTERFACE
MESSAGE ID : 206
** RUN STOPPED : ENERGY ERROR LIMIT REACHED
*** NODE WITH HIGHEST MASS CHANGE
In several cases, the simulation can fail with ERROR termination because too much mass is added to maintain a constant time step for the contact.
- Time step is constant when /DT/NODA/CST, /DT/NODA/CST2 or /DT/INTER/CST are used.
- Interface time step is
computed as
Stiffness increases in function of the penetration .
Figure 1.As the penetration in the contact increases, stiffness increase leads mass to be increased to maintain time step constant.
Figure 2.
Figure 3.For example, the tire stack up against the rigid barrier. Behind the tire, the brake disk (or caliber) compresses the tire against the barrier. The global contact is not stiff enough and leads to large penetrations.- Stiffness increased
- Mass is added to maintain time step constant
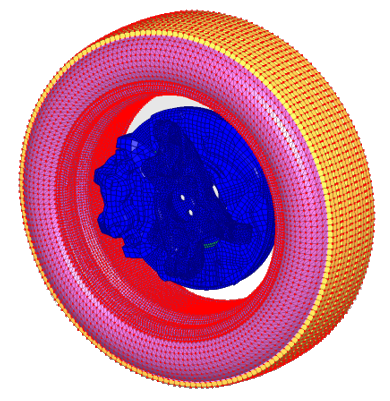
Figure 4. Local contact
Contact between two rigid parts is possible with interface TYPE7 and TYPE11 or TYPE19. The main issue is that it will generate deep penetrations in the contact, which can lead to mass being added to maintain the timestep to the value specified in /DT/NODA/CST or /DT/NODA/CST2.
- Switch at least one of the parts to deformable
- Add a local contact with a higher gap and stiffness
MASS OR ENERGY ERROR DUE TO HIGH DISTORTION
*** NODES WITH HIGHEST VELOCITY
*** NODES WITH HIGHEST MASS CHANGE
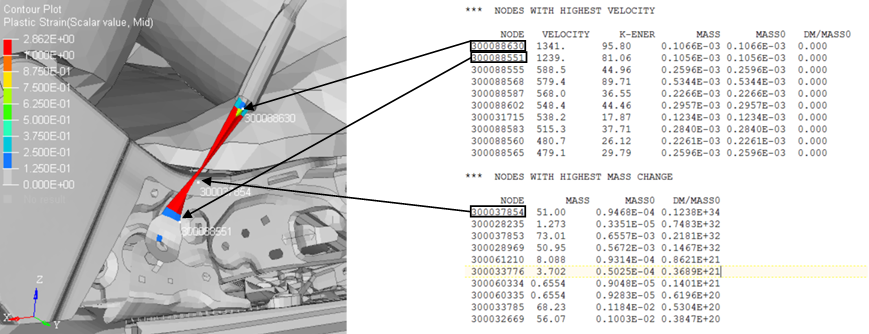
Figure 5.
- Define proper strain failure
- Material may be incorrect (unit system) or type (plastic instead of steel, yield point is too low…)
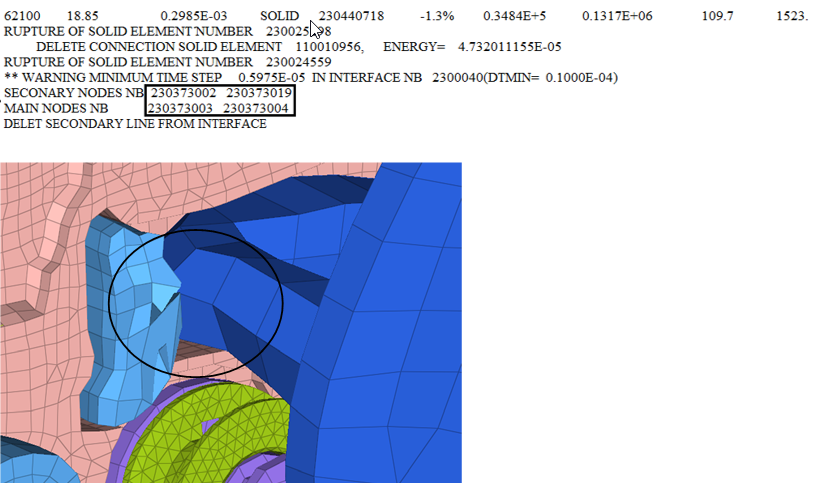
Figure 6.
Initially, there is an intersection that generates the local distortion. To resolve this issue, correct the intersection and define proper strain failure in the material.
RIGID BODY BECOMES UNSTABLE
WARNING ID : 542
** WARNING RIGID BODY INERTIA
DESCRIPTION :
-- RIGID BODY ID : 713264
-- RIGID BODY TITLE : NULL
UNPHYSICAL INERTIA :
PRINCIPAL INERTIA 150.0050404753 IS CREATER THAN THE SUM
OF THE 2 OTHER ONES 0.60340391378794E-02 + 0.3645995262784E-02
When the rigid body inertia is not physical, the rigid body can become unstable. When the rigid body inertia is not physical, Radioss will print the warning in the Starter.
- The rigid body becomes unstable and is propelled at a very high speed in the vehicle
- The rigid secondary nodes are still in the global contact and will generate unrealistic deformation
- Numerical issues as the impact velocity is very high (>1500 m/s)
Correct the unphysical rigid body inertia.
NEGATIVE INERTIA OR STIFFNESS
NEGATIBE INERTIA ON NODE ID=823767293

Figure 7.
WARNING ID: 345
** WARNING : CHECK TIED INTERFACE
DESCRIPTION :
-- INTERFACE ID : 557392358
-- INTERFACE TITLE : CONNECTION.37
8238684 2 823767497 823767293 823767296 823767504 -1.279664112565 -0.9934883789504 0.7066172931858

Figure 8.
- Remove the nodes that project outside the closest main segment from the interface TYPE2
- Translate the nodes so that they do not project outside the segment anymore
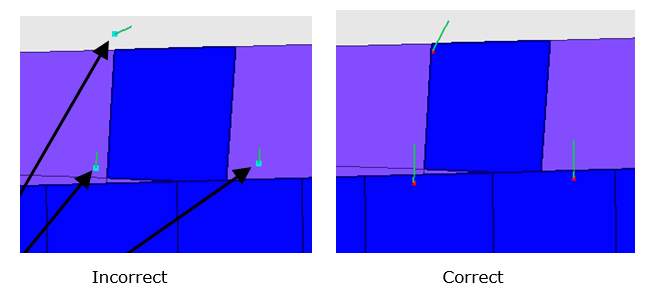
Figure 9.