Morph Constraints
Morph constraints are a powerful tool that can be used to restrict the movement of nodes during morphing operations.
The following types of constraints can be applied to any node: fixed, cluster, along vector, on plane, along line, on surface, and on elements. Whenever a handle is moved that influences a node which is constrained, the node is moved according to the handle perturbation and is then projected back onto the feature to which it is constrained. This allows the nodes to slide across vectors, lines, planes, surfaces, and meshes, to remain fixed when handles are moved, or to move as a cluster along with other nodes. You may also constrain nodes where handles are located which, in effect, constrains the handles. When a perturbation is applied to a constrained handle, the handle are moved along the constraint feature regardless of the applied perturbation. This means that if you apply a translation in the x direction on a handle that is constrained along a vector x - y = 0, the handle moves along both the x and y axes.
There are also morph constraints that can be applied to domains, such as the smooth constraint, which applies spline-based smoothing along the constrained edge domains, and model constraints, which allow you to set a given parametric target, such as length, angle and mass, and have HyperMorph adjust the model to meet that target. These constraints as well as bounded and set distance options for the node constraints are described more fully in the panel help.
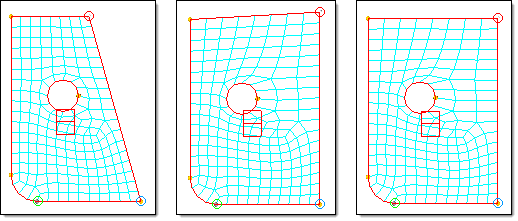
Figure 1. Control Handle Positions with Morph Constraints. The angle of the lower right corner is changed from 74 to 90 degrees using the alter dimensions (angle) operation. The middle frame shows the result with no constraints. The frame on the right shows the result with the node in the upper right corner constrained to move along a vector that lies along the top edge.
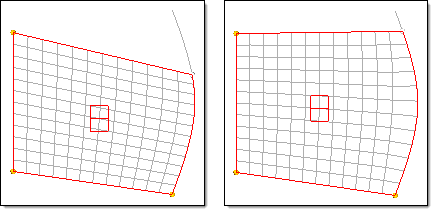
Figure 2. Nodes Tracking a Line During Morphing. The nodes along the right edge domain are constrained to the line. When the handle is moved, it and the other constrained nodes move along the line.
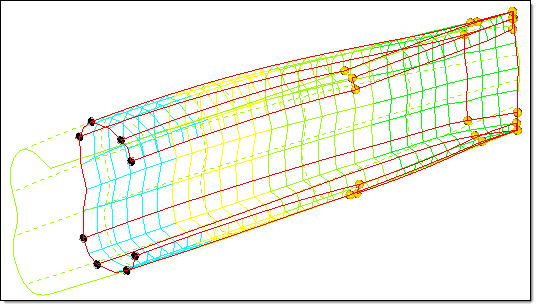
Figure 3. Morph after Mapping to Surface. All mapped nodes are automatically constrained to the surface. When the handles are translated, the nodes are moved along the surface a distance corresponding to the applied handle perturbations. If the handles were also part of the map to geom operation, they too will be moved along the surface regardless of the applied perturbation. In this example, the handles were translated linearly. HyperMorph automatically placed the handles back on the surfaces after applying the translation so that the constraint was obeyed.