OS-T: 1500 Nonlinear Implicit Analysis of Bending of a Plate
This tutorial demonstrates nonlinear large displacement analysis in OptiStruct by simulating the bending of a plate under constant pressure.
A comparison with linear analysis results is also provided to illustrate the requirement of conducting a nonlinear large displacement analysis. This tutorial considers nonlinear geometric effects (large displacements) and elastoplastic material.
For static analysis, the energy equation reduces to F=Ku, wherein we solve for the unknown displacements (u). In Nonlinear Large Displacement analysis, the stiffness (K) may be a function of material, geometry, and boundary conditions. Therefore, an incremental-iterative approach is utilized to calculate the unknown displacements.
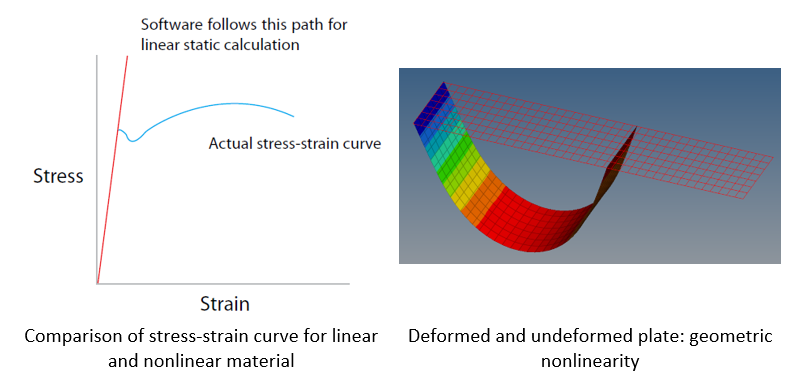
Figure 1.
The analysis considers both geometric and material nonlinearity. The geometric nonlinearity is considered because of the large displacements observed in the geometry. Besides, the resultant stress exceeds the yield stress limit, which implies that material does not conform to a linear stress-strain behavior and plastic effects begin to be observed.
The model description is as follows:
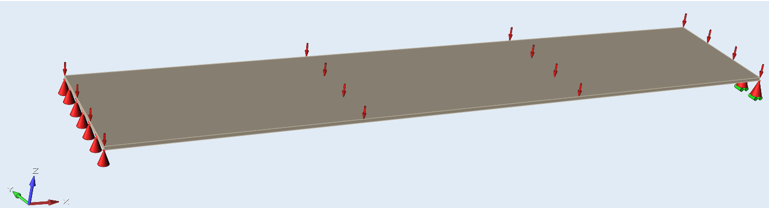
Figure 2. Representation of Constraints and Pressure Load on the Plate
- Units
- Length: mm
- Length
- 1000 mm
- Width
- 200 mm
- Thickness
- 4.0 mm
- Material
- Steel, elastoplastic
- Initial Density
- 7.86e-9 t/mm3
- Young's modulus (E)
- 200000 MPa
- Poisson coefficient
- 0.29
- Yield stress
- 100.0 MPa
- Tangent modulus
- 20000.0 MPa
- Imposed pressure
- 0.02 MPa, applied normal to the plate
- Create plastic material and corresponding shell property
- Set up boundary conditions and imposed load
- Set up nonlinear and linear analysis
- Submit job and view results
Launch HyperMesh and Set the OptiStruct User Profile
Import the Model
Set Up the Model
Update Material
Update Property
Create Boundary Conditions
Create Uniform Pressure
- In the Model Browser, right-click and select .
- For Name, enter LC_IMPLOAD.
- Click Color and select a color from the color palette.
- For Card Image, select None.
- From the Analysis page, click pressures and toggle create.
- Switch entity selector to elems and select all elements.
- Click on the toggle next to magnitute= and switch pressure defintion method to constant vector.
- For magnitude, enter -0.02.
- For load types, select PLOAD as the load type.
- Click .
Define Nonlinear Analysis Parameters
Create Output Parameters Control
Define Output Control Parameters
- From the Analysis page, select control cards.
- Click GLOBAL_OUTPUT_REQUEST.
- For DISPLACEMENT, ELFORCE, OLOAD, STRESS, and STRAIN, set Option to Yes.
- Click return twice to go to the main menu.
Activate Large Displacement Nonlinear Analysis
Create Nonlinear Static Analysis Subcase
In this step, a linear and nonlinear load case are created, both with the same boundary conditions and imposed load.
Submit the Job
- plate.html
- HTML report of the analysis, providing a summary of the problem formulation and the analysis results.
- plate.out
- OptiStruct output file containing specific information on the file setup, the setup of your optimization problem, estimates for the amount of RAM and disk space required for the run, information for each of the optimization iterations, and compute time information. Review this file for warnings and errors.
- plate.h3d
- HyperView binary results file.
- plate.stat
- Summary, providing CPU information for each step during analysis process.
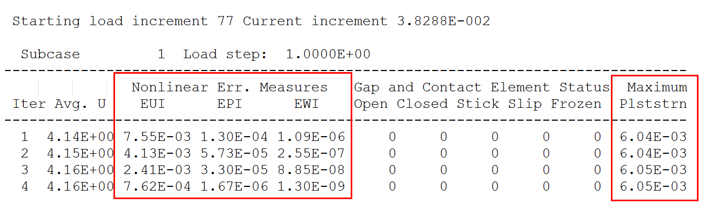
Figure 11.