Beam Elements (TYPE3)
Radioss uses a shear beam theory or Timoshenko formulation for its beam elements.
- No cross-section deformation in its plane.
- No cross-section warping out of its plane.
With these assumptions, transverse shear is taken into account.
This formulation can degenerate into a standard Euler-Bernoulli formulation (the cross section remains normal to the beam axis). This choice is under user control.
Local Coordinate System
The properties describing a beam element are all defined in a local coordinate system.
This coordinate system can be seen in Figure 1. Nodes 1 and 2 of the element are used to define the local X axis, with the origin at node 1. The local Y axis is defined using node 3, which lies in the local XY plane, along with nodes 1 and 2. The Z axis is determined from the vector cross product of the positive X and Y axes.
The local Y direction is first defined at time t=0 and its position is corrected at each cycle, taking into account the mean rotation of the X axis. The Z axis is always orthogonal to the X and Y axes.
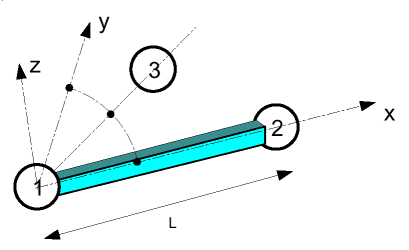
Beam Element Geometry
- A
- Cross section area
- Ix
- Area moment of inertia of cross section about local x axis
- Iy
- Area moment of inertia of cross section about local y axis
- Iz
- Area moment of inertia of cross section about local z axis
Minimum Time Step
Where,
c is the speed of sound: √E/ρ,
a=12min(√min(4,1+b12)⋅F1,√b3⋅F2),
F1=√1+2d2−√2d
F2=min(F1,√1+2ds2−√2ds)
b=AL2max(Iy,Iz)
d=max(dm,df)
ds=d⋅max(1,√12b⋅√1+12E56Gb(1−Ishear))
Beam Element Behavior
- Membrane or axial deformation
- Torsion
- Bending about the z axis
- Bending about the y axis
Membrane Behavior
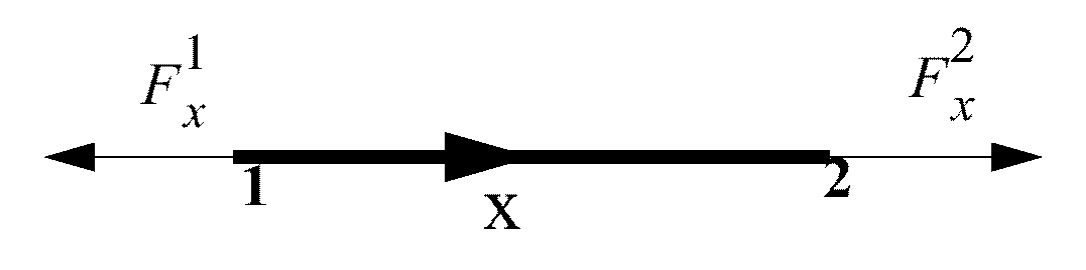
- E
- Elastic modulus
- l
- Beam element length
- υx
- Nodal velocity in x direction
Torsion
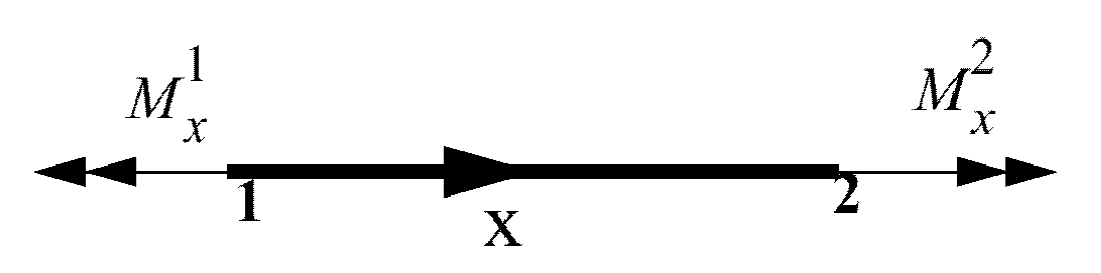
- G
- Modulus of rigidity
- ˙θx
- Angular rotation rate
Bending About Z-axis
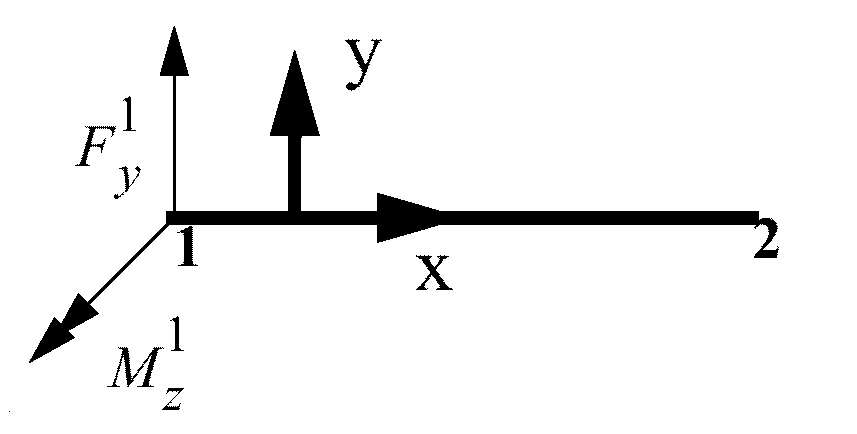
Where,
ϕy=144(1+v)Iz5Al2,
υ is the Poisson's ratio.
The factor ϕy takes into account transverse shear.
Bending About Y-axis
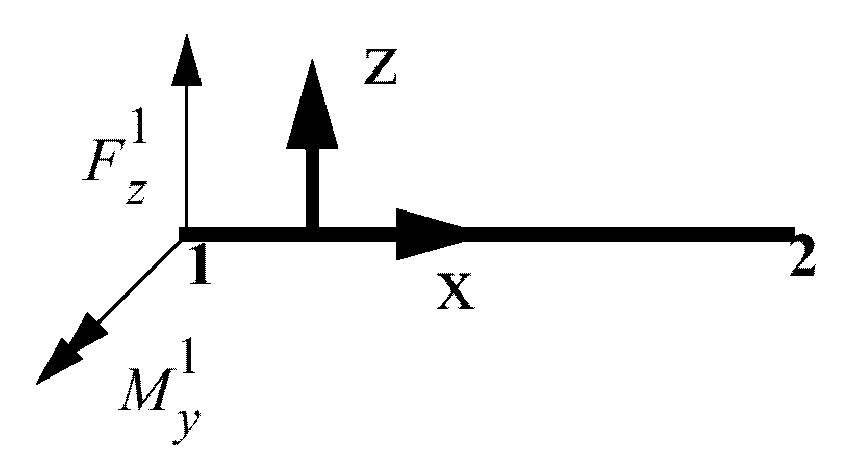
Where, Φz=144(1+ν)Iy5Al2.
Like bending about the Z axis, the factor Φz introduces transverse shear.
Material Properties
- Elastic
- Elasto-plastic
Elastic Behavior
The elastic beam is defined using material LAW1 which is a simple linear material law.
The cross-section of a beam is defined by its area A and three area moments of inertia Ix, Iy and Iz.
Elasto-plastic Behavior
A global plasticity model is used.
However, this model also gives good results for the circular or ellipsoidal cross-section. For tubular or H cross-sections, plasticity will be approximated.