General
The General option in the tree browser provides basic details and displays the entire model in the Help section. It is necessary for all the property files.
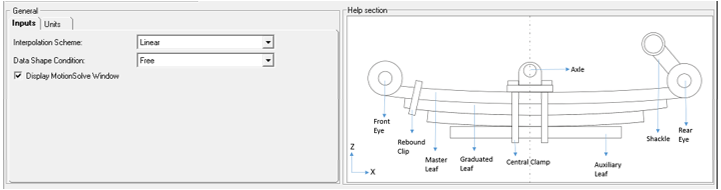
Inputs
- Interpolation Scheme
- Defines the type of interpolation that is needed for the leaf profile.
- Data Shape Condition
- The Leaf Spring Builder builds leaf springs from two different kinds of
profile inputs or shape conditions.
- Free Shape Condition: In Free Shape
condition, an assembled leaf pack is generated. The leaf spring is
created with the center bolt represented as a fixed joint. The input
profiles of the leaves for this option will be the profiles as in a
leaf stack.Note: The leaf pack is assembled in the pack but is NOT installed in a vehicle, in other words, it is not deformed by the vehicle weight.Figure 2. Spring in Free Shape
- Pre-Assembly: In Pre-assembly, you have
individual leaf profiles for each leaf. These individual leaf
profiles can be bolted together with the assembling load. The
following image shows how the data of leaves are collected. If the
free shape data of each leaf is available, it is preferable to
create the leaf pack using this option.Figure 3. Spring in Pre-assembly Position
- Design Assembly: In Design Assembly, an
assembled and loaded leaf spring pack is generated. You have an
assembled leaf spring pack installed in the vehicle with the actual
vehicle loads on it. The leaf spring will be generated with bolt
(Fixed Joint) and design load stored in the beam elements. The input
profiles for this option will be the leave profiles extracted from a
bolted and loaded leaf stack. See Assembled and Loaded Leaf Spring for additional
information.Figure 4. Spring in Free ShapeFigure 5. Spring in Design Assembly
- Free Shape Condition: In Free Shape
condition, an assembled leaf pack is generated. The leaf spring is
created with the center bolt represented as a fixed joint. The input
profiles of the leaves for this option will be the profiles as in a
leaf stack.
Shape Measurements
The Leaf Spring Builder creates MotionView MDL leaf spring models which are only as good as the leaf shapes input entered in the software. Therefore, accurately measuring the leaf shapes in the required coordinate system is important. The coordinate system, its origin and orientation need to follow certain rules to be useful in creating a leaf-spring from the Leaf Spring Builder.The following sections describe the coordinate systems and measurement methods for the Free and Pre-Assembly shape conditions.
The coordinate systems and measurement methods for Design and Free are the same as discussed below.
- Measuring a Leaf Spring in Free Shape
- In Free Shape, the leaves are already assembled into a pack, but not
installed in the vehicle. All of the leaves together form a single unit.
In this condition, the measurements need to be made in a consistent
coordinate system only. Also, it is necessary to input a correct Leaf
Reference Location under the Axle tab. The Leaf Reference Marker will be
created at this location.Figure 6. Leaf Reference Location in Axle Component Properties
- Unacceptable Selections:
-
Figure 11. Unacceptable selection-1Figure 12. Unacceptable selection-2Figure 13. Unacceptable selection-3Figure 14. Unacceptable selection-4
Measuring a Leaf Spring in Pre-Assembly Shape
Leaves in the Pre-Assembly Shape condition are measured as independent entities. A common coordinate system needs to be chosen for all the leaves. The Leaf Builder takes an additional input called Bolt Location in the Pre-Assembly Shape condition, which is used to line up the leaves along a common vertical axis before they are bolted together in a MotionSolve simulation to create the assembled leaf pack.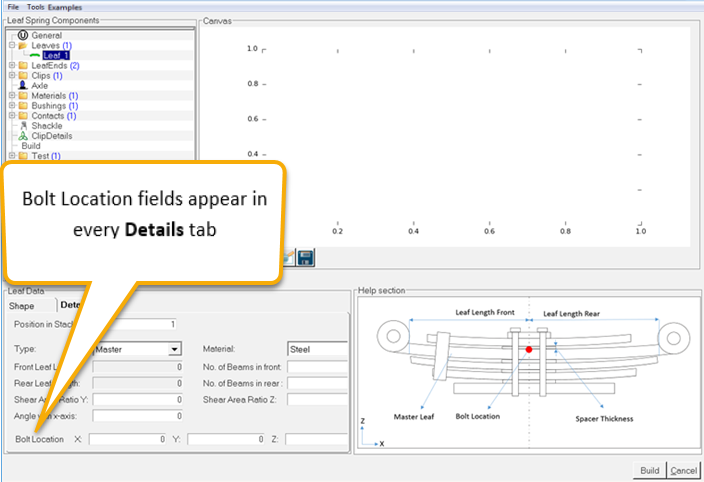
- Acceptable Selections:
- The bolt hole axis of each leaf must be parallel to every other leaf and
and to the Z-axis. The vertical locations of each leaf will be offset by
MotionSolve during assembly, such that
there is no contact between leaves.Figure 16. Acceptable Selection for Pre-Assembly-1Figure 17. Acceptable Selection for Pre-Assembly-2Figure 18. Acceptable Selection for Pre-Assembly-3
- Unacceptable Selection:
-
Figure 19. Unacceptable Selection for Pre-Assembly-1
Leaf Reference Marker
The Leaf Reference Marker (henceforth referred to as LRM in this section) is the coordinate system in which all the points of the leaf profiles are created in MotionView. To move/orient a leaf spring, you can simply move and/or reorient the LRM.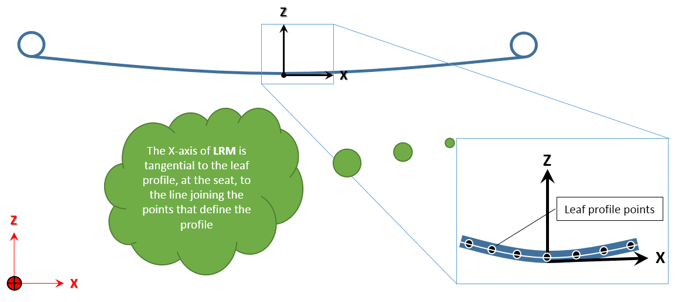
- Free Shape: Leaf Reference Location as input by the user, Top leaf center for Underslung spring and Bottom leaf center for Overslung spring.
- Pre-Assembly Shape: Top leaf bolt location for Underslung spring and Bottom leaf bolt location for Overslung spring.
The Leaf Builder uses the Leaf Reference Marker-origin (location) as the point where the Axle is attached.
General Inputs for Leaf Property File (*lpf)
$---------------------------------------GENERAL_INPUTS
[GENERAL_INPUTS]
CURVEFITTING = 'LINEAR'
DIRECTORY = 'C:\USERS\NG\DESKTOP'
DISPMSOLVEWINDOW = 'TRUE'
NOOFLEAVES = 4.0
NOOFREBOUNDCLIP = 0.0
OUTPUTFILELABEL = 'TEST_LEAF_1'
SHAPECONDITION = 'DESIGN'
Attributes | Type | Valid Value | Required |
---|---|---|---|
Directory | String | Directory path | Yes |
noOfLeaves | Integer | 1, 2, 3... | Yes |
curveFitting | String | Linear Quadratic Cubic |
Yes |
noOfReboundclip | Integer | 1, 2, 3... If there are none, then “ZERO” has to be mentioned. |
Yes |
shapeCondition | String | 'FREE' 'PRE_ASSEMBLY' |
Yes |
outputFileLabel | String | File_label | Yes |
dispMsolveWindow | String | 'TRUE, 'FALSE'' | Yes |
Units
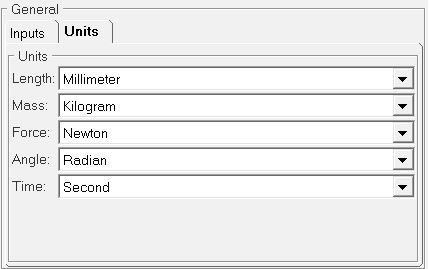
Units for Leaf Property File (*lpf)
$---------------------------------------------------------UNITS
[UNITS]
(BASE)
{LENGTH FORCE ANGLE MASS TIME}
MILLIMETER NEWTON RADIAN KILOGRAM SECOND