Tutorial: Polymer Coextrusion
Set up and run a coextrusion analysis.
Open the Tutorial Model
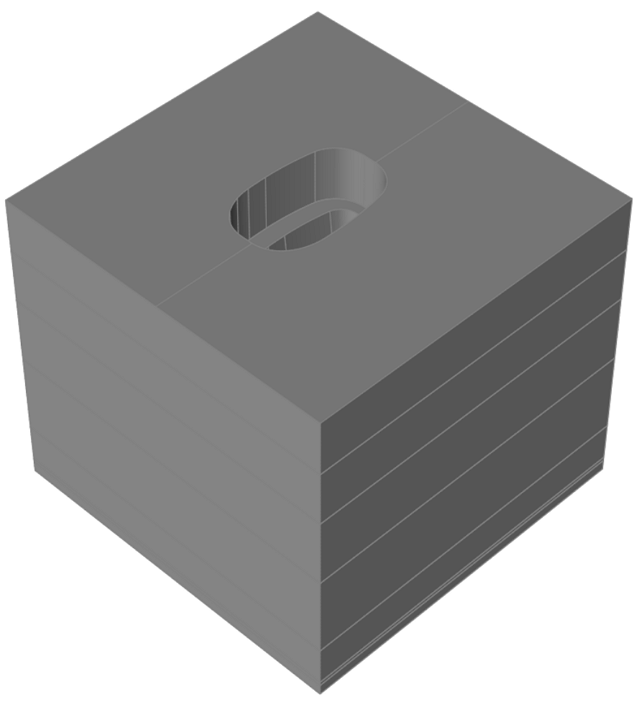
Orient the Model
Extract Flow Volume
Delete Unwanted Solids
Select Materials
- EXXON_PAXON_AB50_003
- HF_PC_LEXAN_GE
Specify Process Data: Inlets
-
Click the Inlet icon.
-
Zoom in to the first Inlet Region of the Polymer Melt.
-
Select the first inlet face. Specify the inlet conditions:
-
Zoom in to the second Inlet Region of the Polymer Melt.
-
Select the second Inlet face. Specify the inlet conditions:
- Right-click and mouse through the check mark to exit, or double-right-click.
Organize Solids Into Polymer Layers
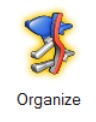
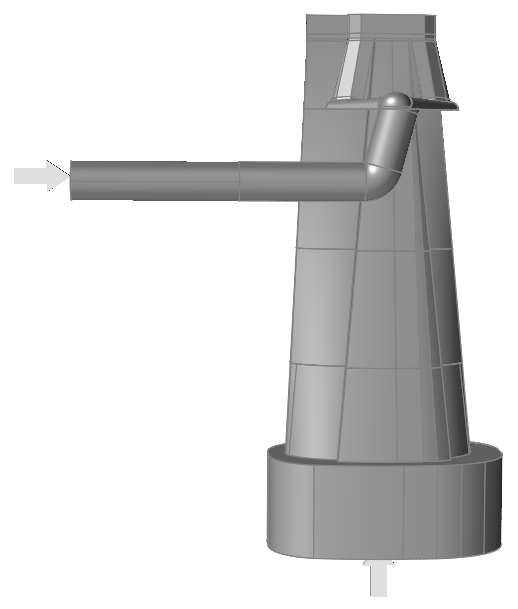
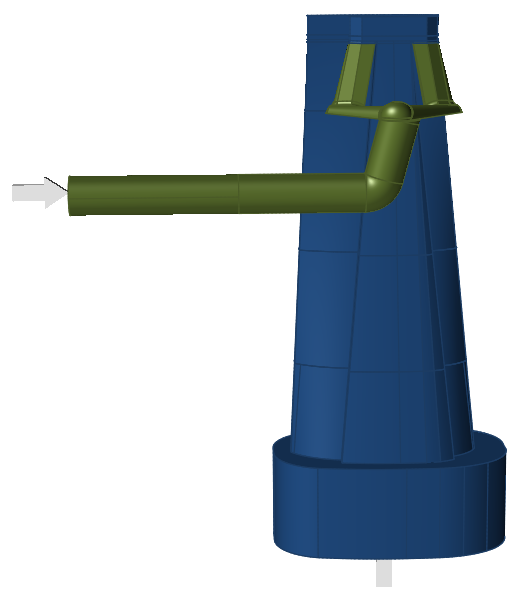
Cut Land
Create Profile Solids
Save Model
Submit the Job for Simulation
-
Click the Analysis icon.
-
Specify the parameters of the analysis process.
- Click Run.
Monitor Job Status
View Simulation Results
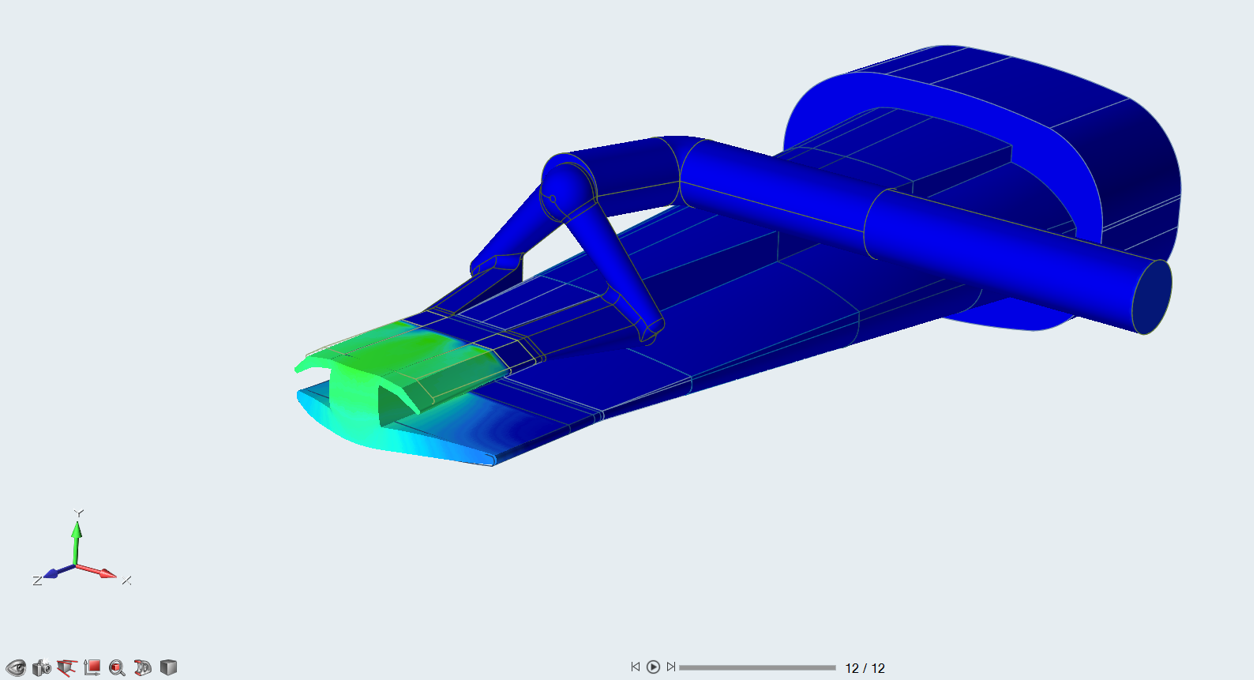
Figure 1. Velocity
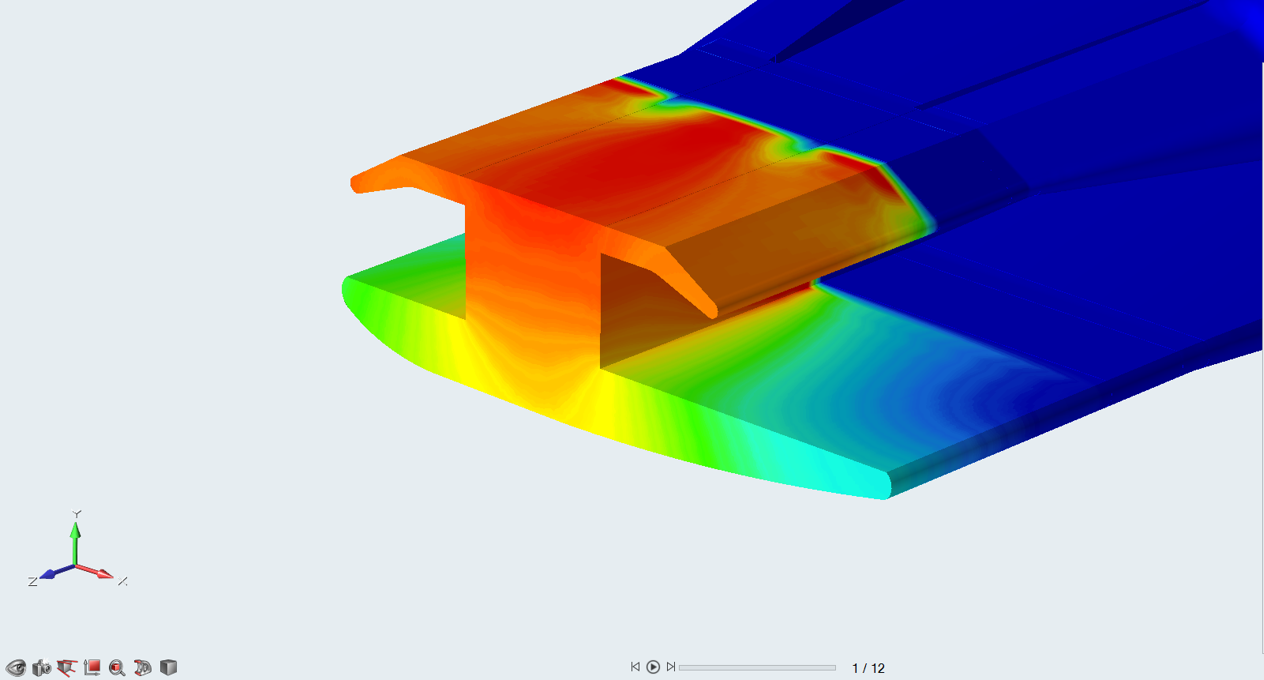
Figure 2. Velocity - Die Exit
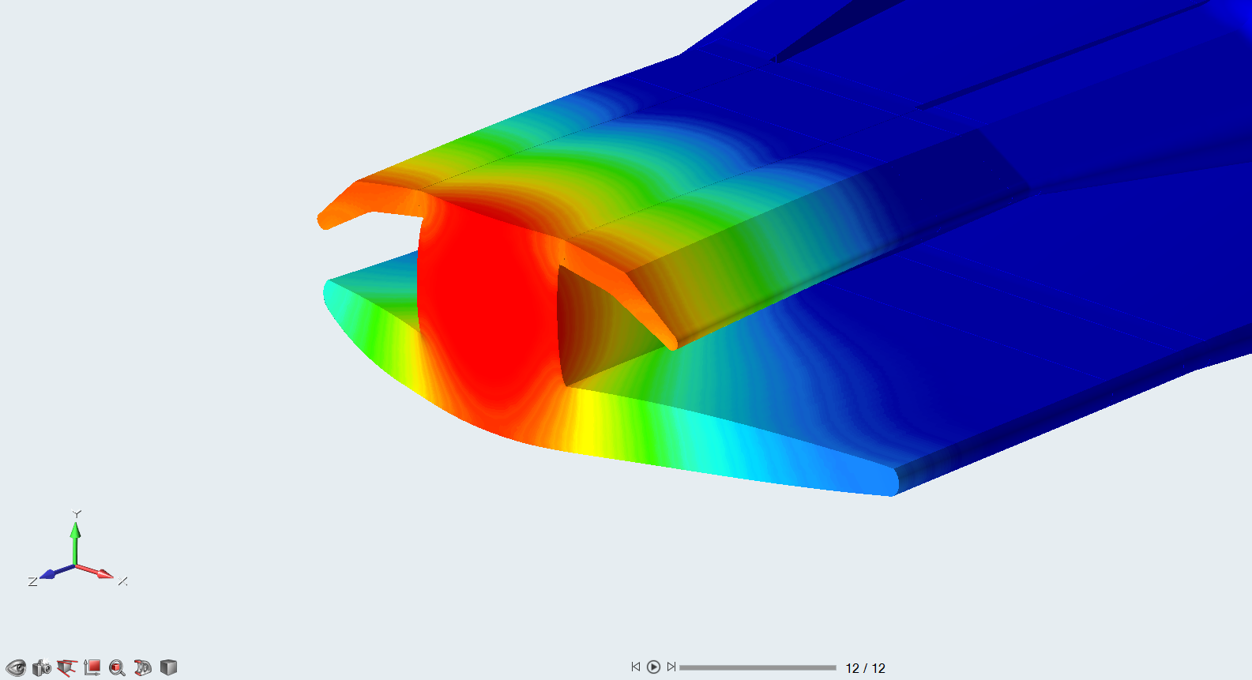
Figure 3. Deformation
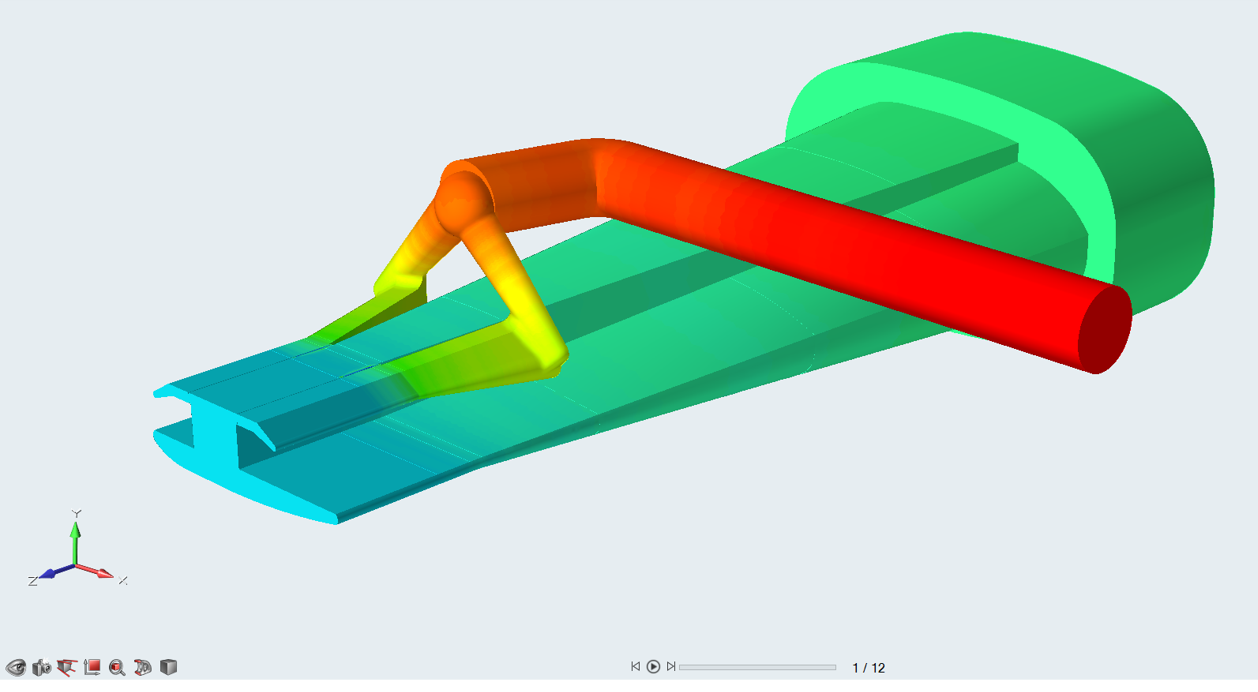
Figure 4. Pressure
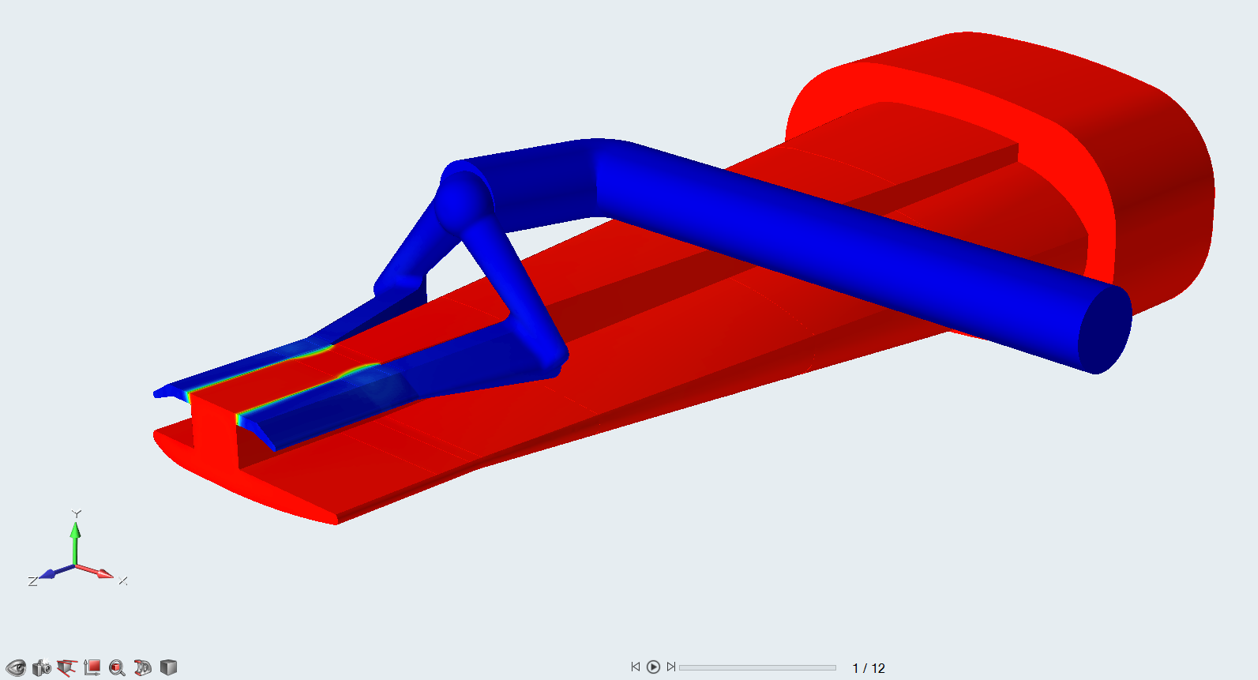
Figure 5. Temperature
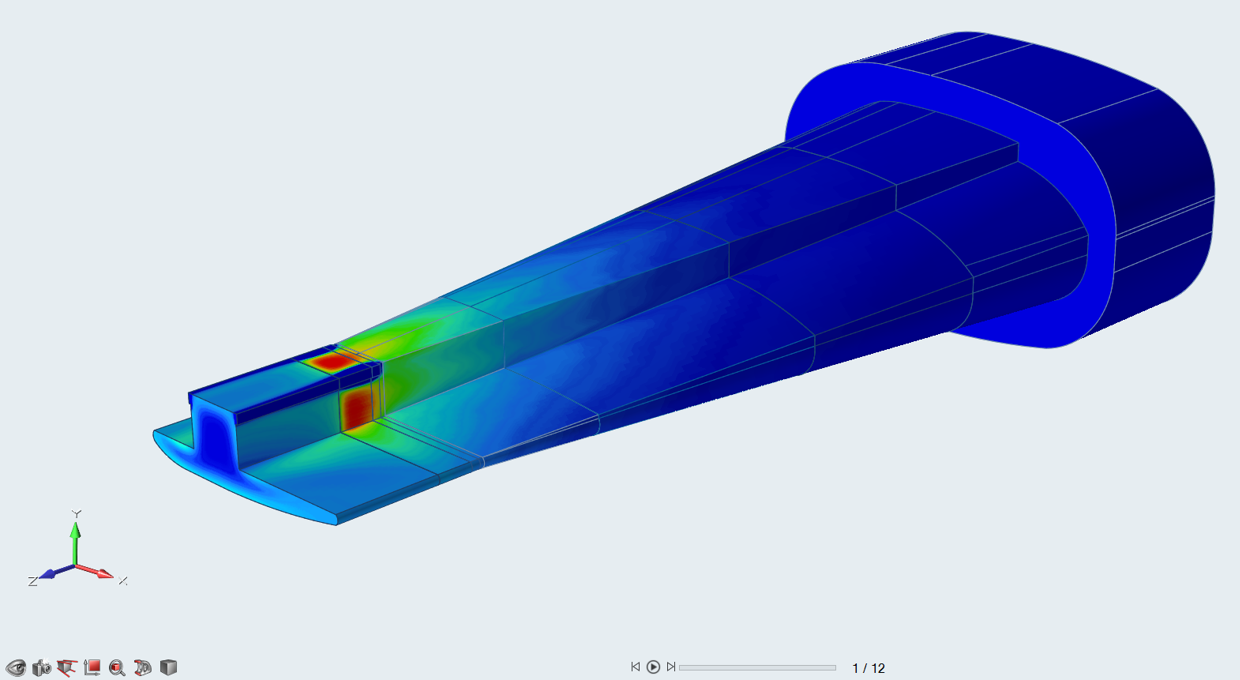
Figure 6. Temperature - Polymer Layer 1
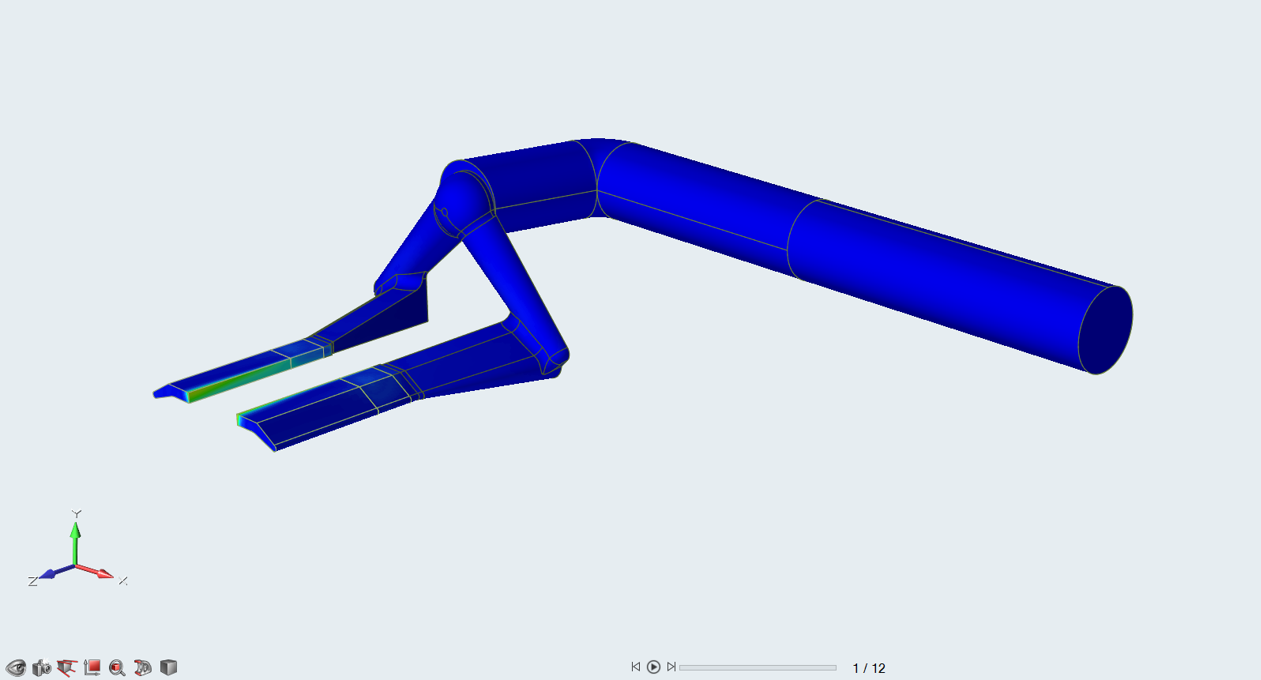
Figure 7. Temperature - Polymer Layer 2
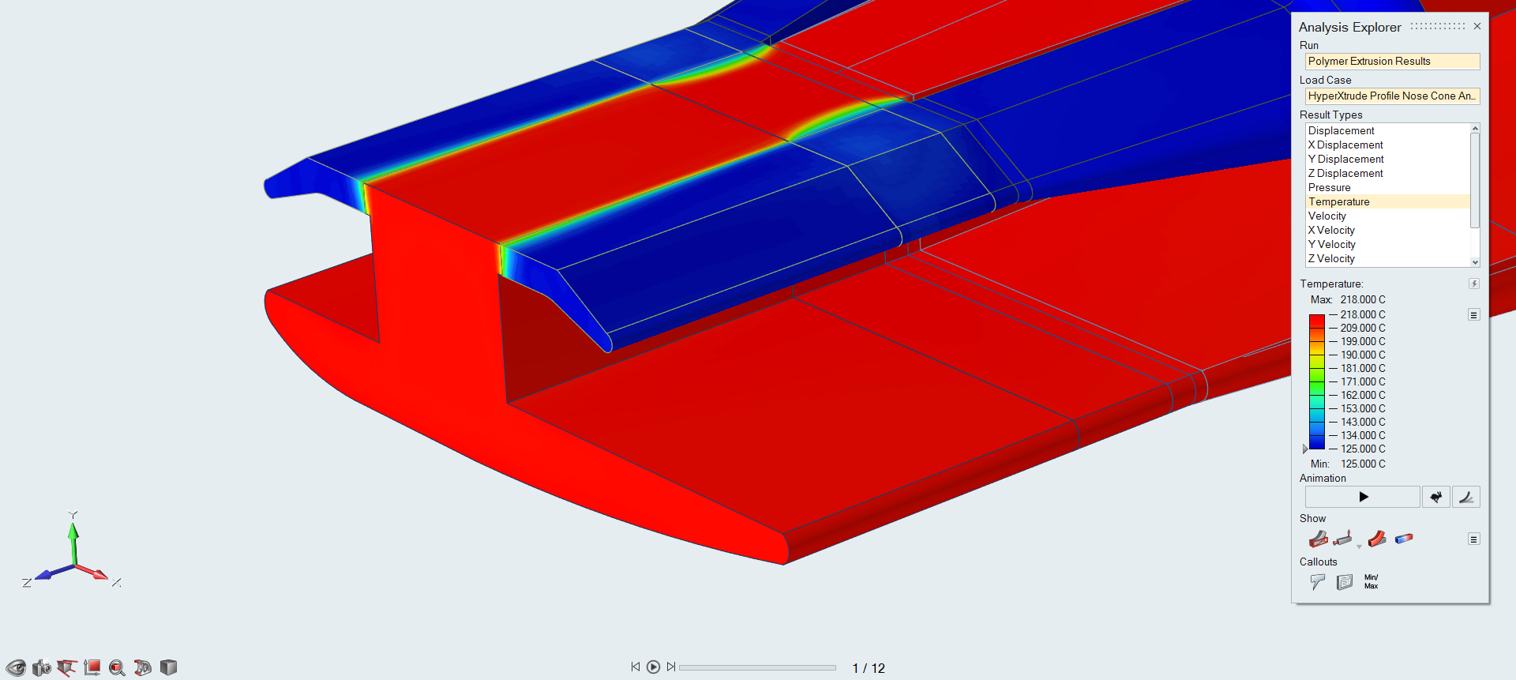
Figure 8. Temperature - Die Exit
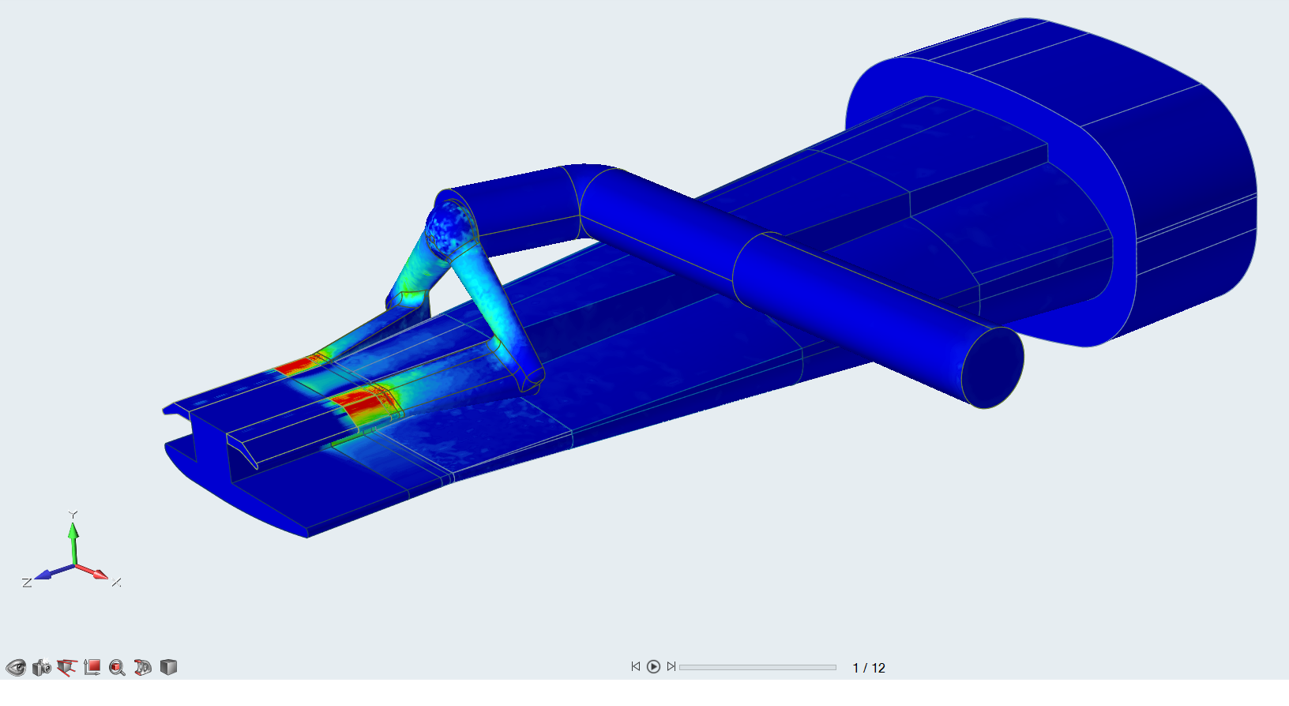
Figure 9. Strain Rate
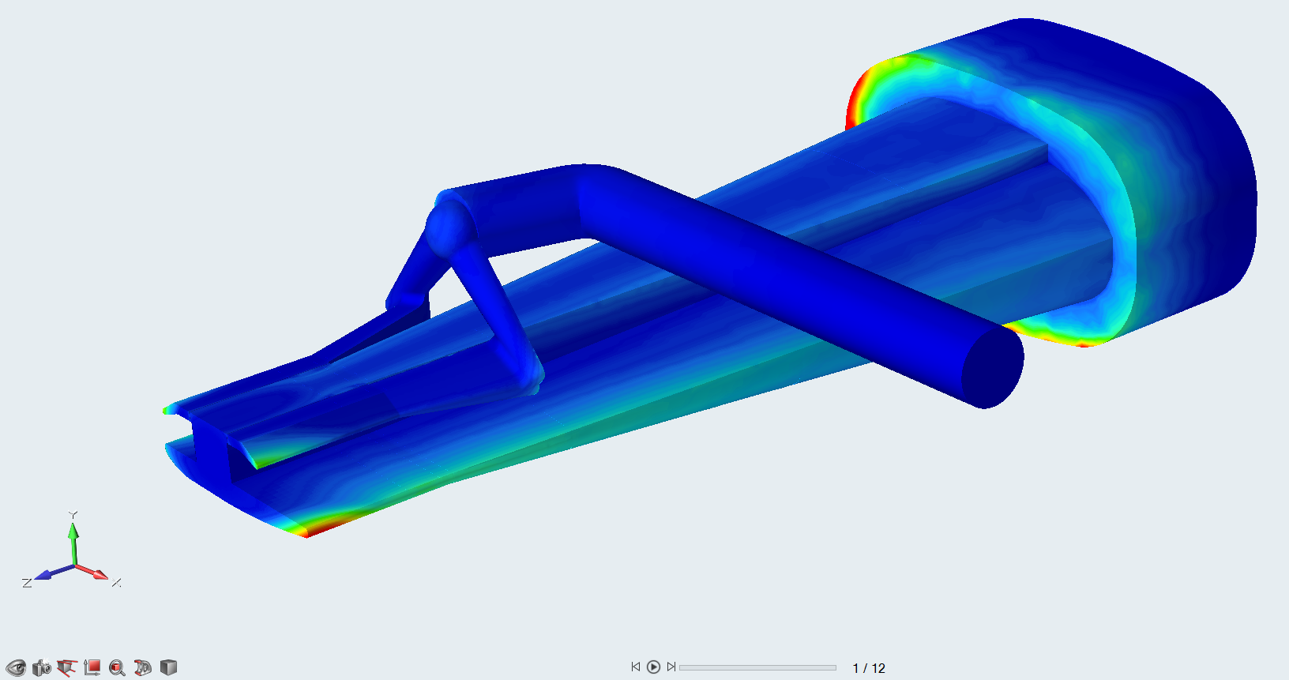
Figure 10. Residence Time
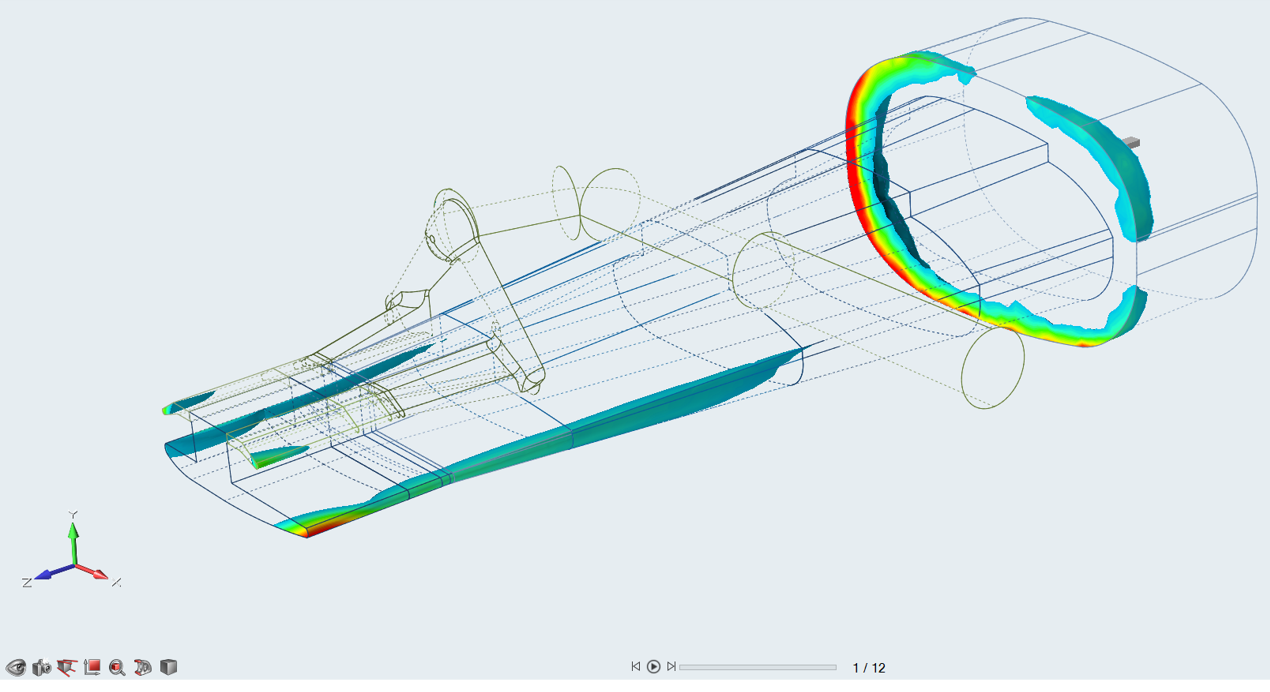
Figure 11. Residence Time