Refinement Zones for Passenger Vehicles
This section explains the resolution best practice for passenger-type vehicles. The recommendations are divided into:
- General best practices
- Hatchbacks/Compacts
- Sedans/Coupes
- SUVs/Vans
- Pickup Trucks
Far field element size and used refinement levels
The simulation uses Refinement Levels (denoted RL), in which the cell size is halved each time the RL increases. This increases the cell count in each direction by a factor of two, and thus a factor 8 in 3d space. As each halved cell also doubles the time-step count per same physical time, the total computational load for a section by increasing the RL level is a factor 16. The far field element size (unit m) defines the largest element size in the model and is set in the .xml file or the inside the VWT. All additional mesh controls are defined relative to the far field size.
With a recommended far field voxel size set to 0.192 meters (192 mm), the following refinement levels will suffice for external aerodynamic simulations:
- RL 0: 192 mm
- RL 1: 96 mm
- RL 2: 48 mm
- RL 3: 24 mm
- RL 4: 12 mm
- RL 5: 6 mm
- RL 7: 1.5 mm
- RL 8: 0.75 mm
Please note that RL6 (3mm) is the Refinement Level that will be used on the whole vehicle for standard passenger vehicles, with local detailing sometimes at a higher RL than that. Therefore, RL6 and RL7 are important reoccurring Refinement Levels.
Types of refinement
- Refinement boxes
- Custom refinement zones
- Offset refinement zones
- Overall offset
- Offset per part
Refinement boxes are axes aligned and defined by minimum and maximum length in each direction (x,y,z).
Custom zones are defined using a closed part in the .stl geometry file, with resolution set inside that part. Please note that these custom zones need to be present in the main .stl file that contains the vehicle. Also note that if the custom zones are not defined but the part is present in the .stl file, any custom zone part will be regarded as having a solid wall. It is therefore important to check that all custom zones are properly defined in the .xml deck or in VWT.
Offset zones are defined using an offset length and Resolution Level. Please note that ultraFluidX will generate a minimum of 4 voxels regardless of the offset length setting. If no part is assigned for an offset, it will be applied to all solid surfaces. If a part is assigned, the offset will only be applied to that particular surface. An offset instance can have multiple parts, and a part can have multiple offsets overlaid on each other. The finest RL setting will have precedence in that case, so if multiple layers are build up with decreasing RL, the coarser ones will need to be defined with an additional offset length of all underlying higher RLs. For example if one wants 4 layers of 1.5mm RL7 and 12 layers of 3mm RL6 on top, the offset lengths would be 4*1.5=6mm for RL7 and 6mm+12*3mm=42mm for RL6.
In the sections below, these 3 types of Refinement will be used to capture relevant physics around the vehicle.
Note that all passenger car sections use versions of the DrivAer model for showing the resolutions (source TUMunich, https://www.mw.tum.de/en/aer/research-groups/automotive/drivaer/, allowance of usage greatly appreciated).
Vehicle refinement for outer regions (RL 1 through 3)
This sections goes through the resolution setup in steps, working inward from the outermost resolution.
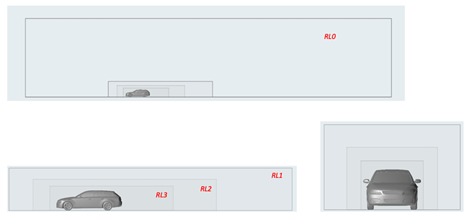
Figure 1. Outer domain RL0 and the first 3 RLs indicated on the DrivAer Estate model
It is recommended that RL1 is at least:
- X: 3 car lengths downstream, 1 car length upstream of the vehicle
- Y: at least one vehicle width off to the sides
- Z: at least one vehicle height above the vehicle
RL2 and RL3 are scaled down from there. It is recommended that RL3 end one car length behind the vehicle.
Refinement zones closer to the vehicle (RL4 and RL5)
Near the vehicle further, RL4 and RL5 are defined to capture:
- the underbody flow
- the wake
- the wheels
- the upstream boundary layer (in case of a VWT floor with a defined BL suction location)
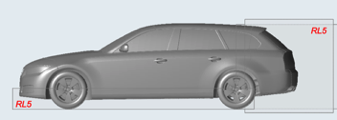
Figure 2. First two zones of interest to capture using RL5
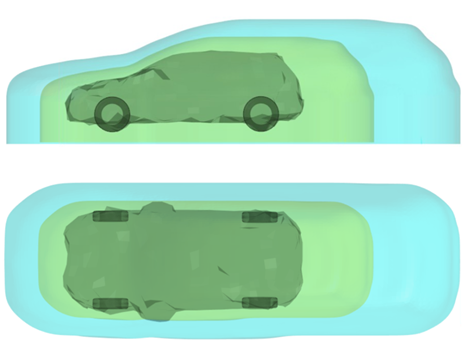
Figure 3. RL4 (blue) and RL5 (green) custom zones based on scaled wraps around a vehicle
VWT floor refinements
In the case of wind tunnel modeling, optional belts and a boundary layer suction location are present. In order to adequately capture the flow development in those regions, resolution needs to be placed correctly.
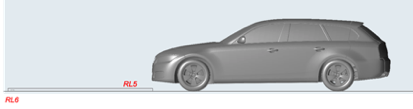
Figure 4. Resolution placement for the boundary layer suction device
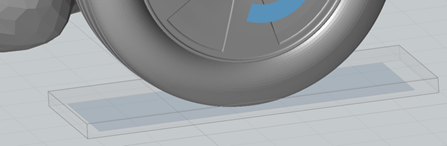
Figure 5. Refinement RL6 boxes around wheel belts
Custom refinements
In order to capture complex regions of high shear and separated flow, specific custom refinements are recommended around parts of the vehicle.
The recommended zones include (but not limited to):
- Nose of vehicle
- Air dams/spoilers
- Cowls
- A-pillar vortices
- Mirror wakes
- Wheels
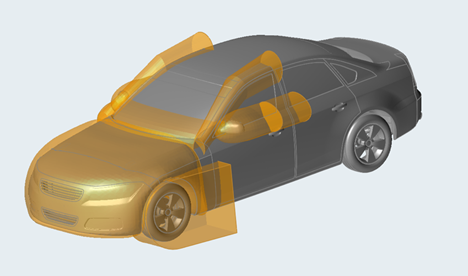
Figure 6. Example of custom refinement zones around the vehicle for capturing flow details
In the sections below, each custom refinement zone will be explained in detail.
- Mirror custom refinement
- The mirror needs special attention and two refinement zones need to be created. First, start by wrapping the mirror with a 12 mm convex wrap. Move the wrap rearward 100 mm and wrap the two wraps with a 12 mm convex wrap then scale this wrap by 105%. This will be a refinement zone of level RL6. Repeat the process by scaling the first mirror wrap by 120% and copying the wrap rearward 1.0 m and wrapping them with a 12 mm convex wrap. This wrap will become a resolution zone of RL5.
- Nose custom refinement
- Select the nose region and add surfaces in order to close the region. Loose wrap around the region, scaling and extruding down to the floor. This covers the engine bay and some wakes. It is recommended to set to RL5 (6mm) to capture the engine bay and the surrounding flow.
- Cowl and A-pillar custom region
- Create a simplified shape that generously covers any cowl vortex and separation/reattachment on the windscreen. RL6 is recommended.
Offset refinements
Now that separated flow regions are covered using custom zones and/or boxes, offsets regions are used to capture the boundary layer flow in regions of interest.
As mentioned, offset regions can be general on all parts (when no specific part is indicated) or on separate sections. The offsets are used to set resolution in the boundary layers on the vehicle in order to capture the necessary physics. As boundary layers are growing over the vehicle, you see more placement of resolution on the upwind parts of the vehicle, where boundary layers are typically thinner. Also, separations and the effects of pressure gradients are important. Therefore, one will also see placement of resolution on parts that (possibly) separate, and rounded corners where large pressure gradients occur.
- General offset refinement on whole body
- As a starting point, for the general offset, 4 voxels (4x3mm=12mm) of
RL6 is recommended on the whole vehicle. Please note that in case of
scaling the far-field resolution, the offset distance needs to be scaled
to match 4 voxels again. This is true for both general and part
offsets.
Figure 7. Whole body offset on all parts: RL6 4 voxels - Specific part offsets
- Next, specific part offsets need to be defined. The following regions are recommended for extra offset refinement:
Wheels and tires
Parts that rotate are identified as wheels. There are two methods currently available to describe rotation in ultraFluidX. They are:
- Rotating walls
- Moving Reference Frame (MRF)
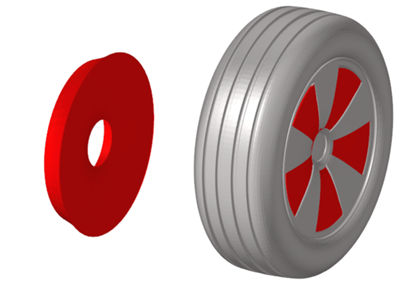
Figure 11. MRF zone created and its position with respect to the wheel spokes
Special preparations for fully treaded, deformed tires
Standard best practice is to use non-treaded tires that are undeformed, and intersect with the ground plane, with longitudinal stripes (axisymmetric) remaining in the part.
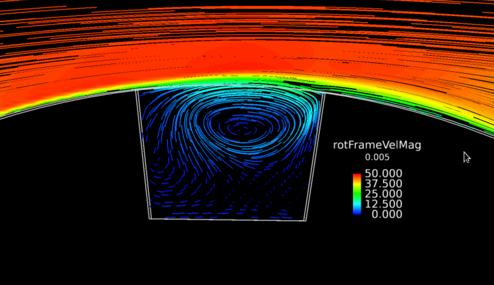
Figure 12. Example cavity flow when transformed in a rotating coordinate frame
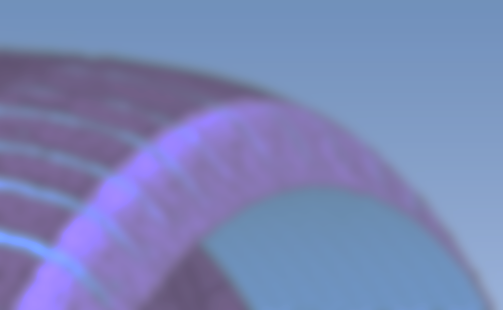
Figure 13. Optional MRF (light blue) in tire treads, not needed in base Best Practice
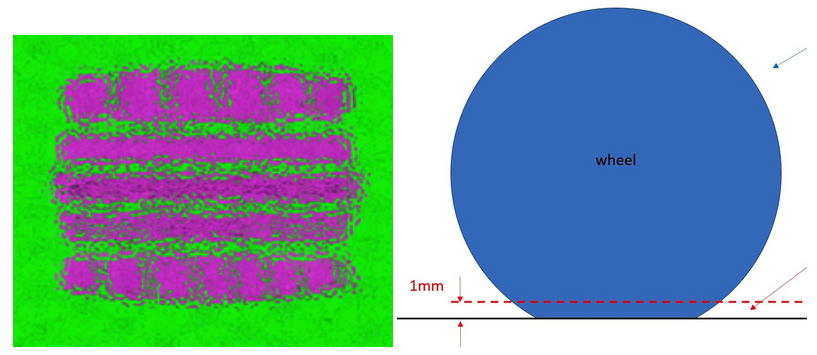
Figure 14. Deformed tire interface patch for special tire studies
Porous media and cooling flow
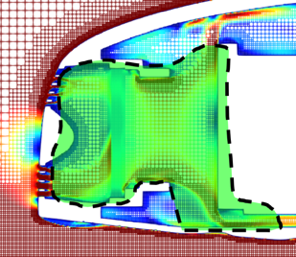
Figure 15. Cooling flow region in RL5, shown on DrivAer model
A minimum number of 6 voxels is recommended across the thickness of any porous media, where possible. Therefore, the cooling pack itself would often receive a box refinement of RL6 tight around the pack.
Strategy for Large-Eddy Simulations
- Introduction
-
ultraFluidX employs physics based modeling using a two-way coupled system, where the shear stress of the wall model projected onto the surface is continuously being matched with a shear force in the bulk flow. This provides a more accurate model versus one-way coupling, where the shear forces are based on modeled parameters. For thin boundary layers, where the resolution is too large to capture the small vortices, there are two techniques used to more accurately model the appropriate physics. These are as follows:
- Wall model variants per part
- Vortex generator to initiate turbulent eddies
- Background for usage
- ultraFluidX is a Large-Eddy Simulation solver
that provides details of the flow, including the flow in the boundary
layers. Changes to the two-way coupled model are needed where thin upstream
boundary layers occur on curved regions, and the resolution in terms of
voxels over boundary layer thickness is low. Typical regions on automotive
vehicles are listed in order of importance:
- Mirrors
- Nose and front bumper
- Leading edges of tires
Figure 16.
Wall Model Variants
- Application: Mirrors
- The mirrors typically have a high curvature and thin boundary layers
before separating over the cover edge. To model the correct physics on
the mirror, a wall model variant is specified on the mirror part. The
wall model variant on the mirrors uses the one-way coupled model instead
of the default two-way coupled model. The one-way coupled model is more
robust in predicting the flow and drag when there is not enough
resolution and length to develop the boundary layer fluctuations.
Figure 17.
Turbulence Generator
- Application: Nose and front bumpers
- The nose and bumper of an automotive vehicle includes a stagnation area
and a developing boundary layers around the curvature of the bumper and
nose. This area creates the upstream conditions for the rest of the
vehicle. In order to aid the development of the boundary layer, the
usage of a turbulence generator is recommended. The turbulence generator
needs to be close to the stagnation region to create turbulence in the
thin boundary layers in the form of randomized vortices. A box
resolution zone of RL6 is set around the turbulence generator that
covers approximately 10mm upstream of the generator and 300mm downstream
to cover the bumper curvature.The turbulence generator can be placed based on the external dimensions of the vehicle:
- x direction: 24mm upstream from the xmin location
- y direction: + and -80% of the width/2 in y direction (as defined from the symmetry line)
- z direction: 10% to 60% of the height in z (as defined from the ground)
Figure 20.
Consideration for Specific Vehicle Types
Considerations for Hatchbacks/Compacts/Estates
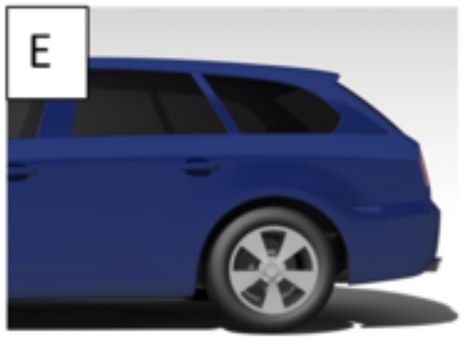
Figure 23. Estate (E) models are examples of mentioned geometry types in this section
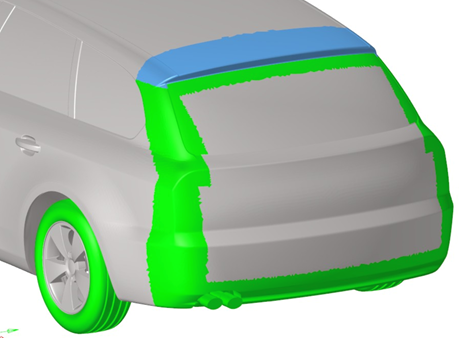
Figure 24. RL7 regions on the tail end of hatchbacks, compacts, or estates. Resolution is placed in zones where separation is bound to happen, all around the base. Note the special consideration for any spoiler element (in blue).
Note that the base does not need to be in RL7, which saves elements. Also, the RL7 region extends past the separation edge as mentioned before. The shape of the RL7 region might not span a single part, but can wrap sections of adjacent parts, as well. In the figure above for example, part of the rear glass is included in the region. Often taillights are in this zone. It is recommended to place the whole taillight unit in the RL7 region.
Considerations for Sedans/Coupes/Fastbacks
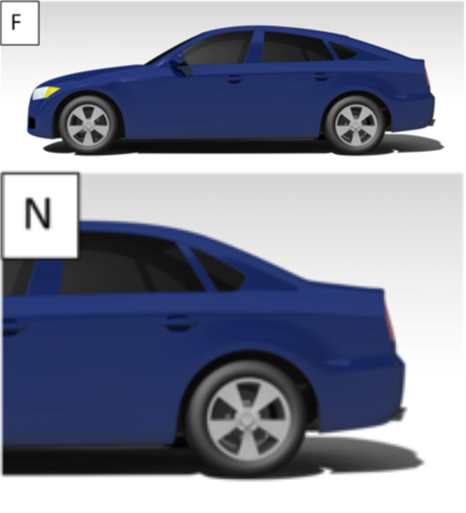
Figure 25. Fastback (F) and Notchback (N) models are examples of mentioned geometry types in this section
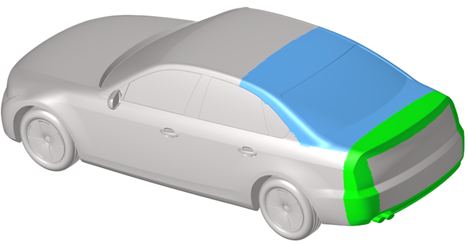
Figure 26. RL7 regions for consideration, known separation edges (green), adverse thickening boundary layers (blue). For cleanliness of the image, the other high resolution regions on the vehicle are not indicated (including rear tires).
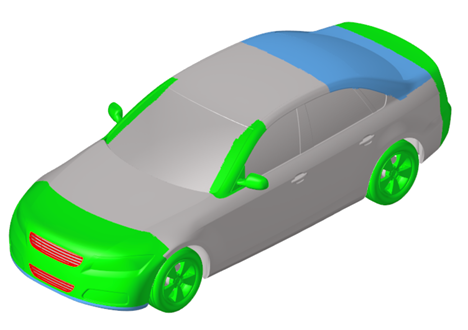
Figure 27. Complete offset strategy for the DrivAer sedan model
Considerations for SUVs/Pickup Trucks/Vans
- Refinement zones
- Due to the increased sizes typically of SUVs/pickups/vans, the far-field resolution might need to be increased to have a reasonable cell count for the simulation. RL6 is 3mm on passenger cars, 3.2mm or 3.5mm RL6 is recommended depending on the size. For a 3.2mm setup for example, the resolution regions would look like this:
- Custom refinement cowl/A-pillar/mirrors
- When windscreens are more upright, a separation can occur upstream on the hood. Make sure that the cowl custom refinement region is enlarged to capture this phenomenon. A-pillar vortices and mirror wakes can be larger, enlarge the refinement regions and blend with overlap with the cowl and mirror wake regions.
- Truck beds
- Truck beds can have complex flows in them, where the flow from the cab interacts with the tailgate. It is recommended to add a region of RL5 surrounding the whole truck bed. Both the cab end, top of the tailgate area and sides of the truck around the taillights should have RL7 refinements as defined before (4x RL7 + 12x RL6), as the separation. The shear layer at the end of the cab should be captured in an RL6 custom refinement region for about 30cm, as well as the volume around the top of the tailgate.
In conclusion: General Mesh Setup for Passenger Cars
Based on the described best practice, a vehicle of 100-250 million voxels is created, depending on the vehicle details. A typical runtime of around 8 hours on Nvidia 8x V100 GPUs is estimated for 4 seconds of physical time using this scheme.