Multi Volume Meshing (Sequential)
If the flow domain is split into several parts and each part is meshed independently, you need to ensure that the mesh is consistent/matching at the interfaces.
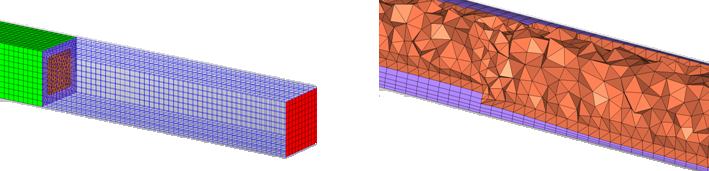
Figure 1.
View new features for Engineering Solutions 2022.1.
Engineering Solutions is a modeling and visualization environment for NVH, Squeak and Rattle Director, Crash, CFD, and Aerospace using best-in-class solver technology.
Discover Engineering Solutions functionality with interactive tutorials.
Noise, Vibration and Harshness (NVH) is an important vehicle attribute that directly affects the customer experience.
Use Squeak and Rattle Director tool to create evaluation lines, evaluate them and optimize the interfaces to eliminate squeak and rattle issues.
The Crash application offers a tailored environment in HyperWorks that efficiently steers the Crash CAE specialist in CAE model building, starting from CAD geometry and finishing with a runnable solver deck in Radioss, LS-DYNA and PAM-CRASH 2G.
HyperWorks offers high quality tools for CFD applications enabling the engineer to perform modeling, optimization and post-processing tasks efficiently.
Engineering Solutions offers a wide range of tools enabling you to perform CFD modeling in an efficient manner.
The CFD user profile provides an environment tailored to the needs of a CFD analyst to perform all pre-processing steps in an efficient way.
The CFD Mesh tab on the Utility menu provides shortcuts to commonly used panels and to specific tasks used for CFD analysis and optimization.
The following is a general guideline for CFD modeling.
The following options are available from the Geometry menu.
Engineering Solutions offers several meshing algorithms for lines/edges (1D), surfaces (2D) and volumes (3D) which can be accessed via the Mesh menu.
The Line Mesh panel allows you to create a chain of one dimensional elements such as beams along a line.
Engineering Solutions has a centralized plate and shell mesh generation tool called the Automeshing Secondary panel. Most of the element creation panels use this module, which supplies as much automated assistance as possible.
Engineering Solutions provides several CFD volume meshing schemes to generate high quality grids in an automated manner.
Use the CFD Tetramesh panel to generate hybrid grids, containing hexa/penta/tetra elements in the boundary layer and tetra elements in the core or fare field.
Local remeshing of a tetramesh can become necessary if baffles have to be included in an existing mesh or if the mesh has to be refined locally.
If the flow domain is split into several parts and each part is meshed independently, you need to ensure that the mesh is consistent/matching at the interfaces.
Create a hex-core mesh inside any arbitrary volume defined by a surface mesh consisting of 2D first order elements: tria3 and quad4.
The Curvilinear Hex Core meshing tool is designed for tube style systems, for example exhaust tubes, in which a centerline of the geometry can be generated easily.
The Wind Tunnel Mesh button on the Utility menu opens the Wind Tunnel Meshing function.
Create pyramids on the outer quad faces of components/collectors containing 3D/volume elements, or on 2D quad elements in which case pyramids are created on the side of the quads’ normals.
Mesh quality can be checked using the Check Elems panel. The Check Elems panel allows you to verify the basic quality of your elements and to verify the geometric qualities of those elements.
Use the Tetra Mesh Optimization to improve the quality of a tetra mesh with respect to several element criteria.
The Adaptive Wrapper is a useful utility to get a clean, water tight shell mesh out of 2D mesh containing several intersecting parts and small gaps which do not need to be modeled.
This section describes the basic ideas of Engineering Solutions's morphing technology and how it can be combined with HyperStudy and a CFD solver to perform automated design or optimization studies.
HyperView is a powerful CFD post-processor which can import result data from all major CFD solvers (AcuSolve, CFD++, Fluent, and so on) via the EnSight format.
Essential utility tools developed using HyperWorks-Tcl.
Solver interfaces supported in Engineering Solutions.
A solver interface is made up of a template and a FE-input reader.
Support provided by the CAD readers and writers.
Browsers supply a great deal of view-related functionality by listing the parts of a model in a tabular and/or tree-based format, and providing controls inside the table that allow you to alter the display of model parts.
Panels contains pre-processing and post-processing tools.
Create, edit, and cleanup geometry.
Different types of mesh you can create in HyperWorks.
Create connections between parts of your model.
Create, organize and manage parts and subsystems.
Perform automatic checks on CAD models, and identify potential issues with geometry that may slow down the meshing process using the Verification and Comparison tools.
Overview of how to build a finite element model.
Morph the shape of your finite element model.
Setup an Optimization in Engineering Solutions.
Convert finite element models to another solver format.
Study relationships between data vectors in results files.
Learn how to use post-processing functions.
HyperWorks offers high quality tools for CFD applications enabling the engineer to perform modeling, optimization and post-processing tasks efficiently.
Engineering Solutions offers a wide range of tools enabling you to perform CFD modeling in an efficient manner.
Engineering Solutions offers several meshing algorithms for lines/edges (1D), surfaces (2D) and volumes (3D) which can be accessed via the Mesh menu.
Engineering Solutions provides several CFD volume meshing schemes to generate high quality grids in an automated manner.
If the flow domain is split into several parts and each part is meshed independently, you need to ensure that the mesh is consistent/matching at the interfaces.
If the flow domain is split into several parts and each part is meshed independently, you need to ensure that the mesh is consistent/matching at the interfaces.
© 2022 Altair Engineering, Inc. All Rights Reserved.