Seam Hexa Adhesives
This realization creates a continuous or discontinuous hexa weld with a predefined pattern.
For Abaqus, this realization uses the prop_abaqus_acm.tcl property script. For Nastran and OptiStruct, prop_nastran_acm.tcl is used.
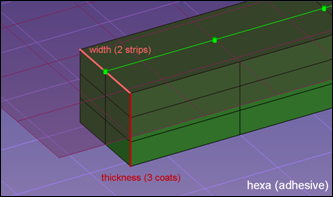
Seam Hexas are created from the Seam panel.
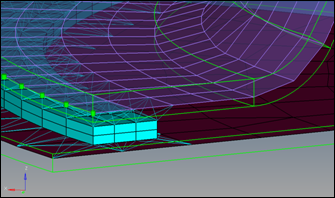
For OptiStruct and Nastran solvers, the HEXA elements are tied to a shell using RBE3s at locations where the HEXA nodes and shell nodes are non-coincident. If the HEXA nodes and shell nodes are coincident then RBE2s will be used to tie them.
This realization type is intended to work on meshes, both shells and solids.
- The length of a hexa is predefined by the distribution of the test points along the seam connector. This is defined by spacing or density during the connector creation.
- The width of the single hexa depends on the number of strips and the defined total width of the seam, which is measured perpendicular to the seam direction.
- The thickness of a single hexa depends on the number of defined coats and the selected thickness option.
- shell gap
- The seam completely and exactly fills the gap between the two shells. Shell
thicknesses and offsets are not considered.Figure 3.
- maintain gap
- The seam is positioned in the exact middle between the shells. The seam
thickness is adjusted, that on both sides the gap between shell and seam
fits the defined gap size. Shell thicknesses and offsets are not
considered.Figure 4.
- (t1+t2)/2
- The seam thickness is calculated by averaging both shell thicknesses. On the
left side the offsets and thicknesses are taken into account, so that the
seam is positioned around the middle of the air gap. On the right side the
seam is just positioned around the middle of the shell positions.Figure 5.
- midthickness
- On the left side the exact air gap is determined and filled with the seam.
On the right side the seam thickness is calculated by subtracting half the
thickness of both shells from the total distance of the shells.Figure 6.
- const. thickness
- The thickness of the seam is predefined for both; on the left side the seam
is positioned around the middle of the air gap, on the right side around the
middle of the two shells.Figure 7.
- Anything with "edge"
- Snapping to edge activated when using any of the hexa position options that refer to an “edge”. This is to ensure that the connector can identify an “edge” to realize to.
- Midpoint to connector
- The connector realization will follow the connector line until the connector line is in space (Figure 8). At which point it will try to realize at the closest projections within tolerance (Figure 9). Once the connector is outside of the tolerance it will fail (Figure 10).
The following options are available for Adjust Width:
- None
- Allows the hexa to self-intersect.
- Reduce Width
- Reduces the inner width to find a position where the mesh is not intersecting.
- Move Hexa
- Performs the same operation as the previous option by reducing the inner width to find a position where the mesh is not intersecting. This will then add the removed width back to the outer diameter to maintain the specified width.