OS-E: 3030 Plate in Torsion
Demonstrates the power of topography optimization.
Model Files
Refer to Access the Model Files to download the required model file(s).
The model file used in this example includes:
twistplate.fem
Model Description
- A specific part of the structure is to be loaded in torsion (Figure 1).
- The part is to be formed using a stamping process.
- Only the shape of the plate can be changed, the thickness cannot be changed.
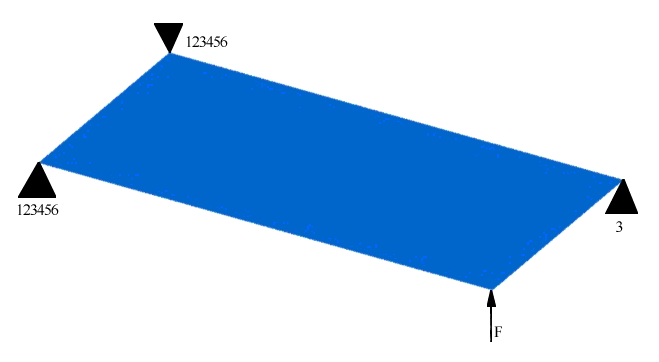
Figure 1. Loads and Constraints
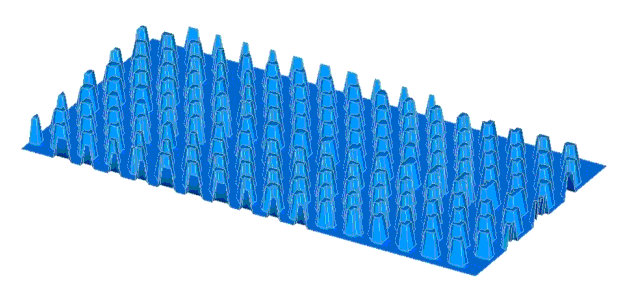
Figure 2. Inner Portions of the Shape Variables for the Plate
The potential reinforcement pattern can be any combination of these variables deflected at any height between zero and the user-defined maximum height. OptiStruct creates a reinforcement pattern of any shape by manipulating the 174 discrete shape variables. The pattern could resemble an X, an oval, a series of straight beads, or any number of the millions of potential designs. By setting various parameters, you can ensure that any design OptiStruct creates is manufacturable.
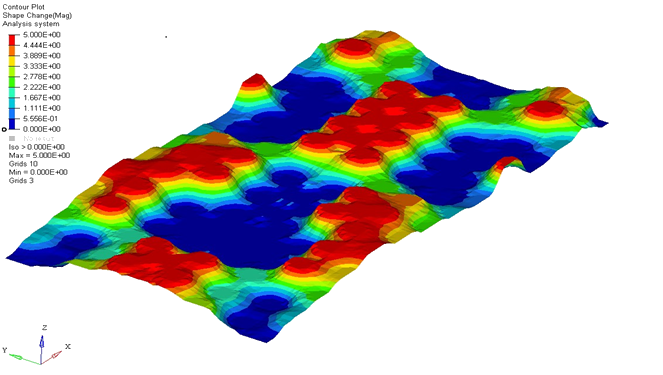
Figure 3. OptiStruct Bead Reinforcement Pattern for a Plate in Torsion
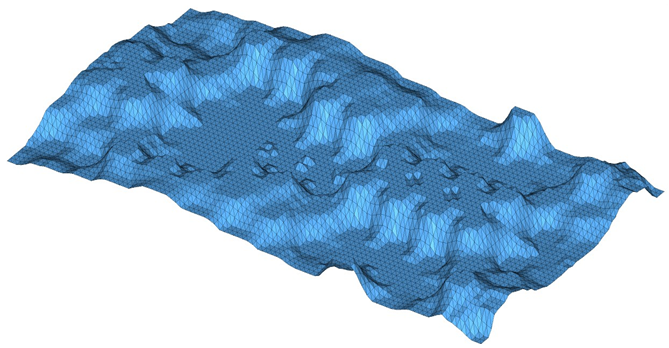
Figure 4. Finite Element Model Built from OptiStruct Results
The face of the plate is covered with X-shaped cross-beads that work well in torsion. None of the beads run completely across the plate in a straight line which would reduce their effectiveness. Finite element analysis of the plate revealed a well distributed stress pattern and low deflection at the load point.
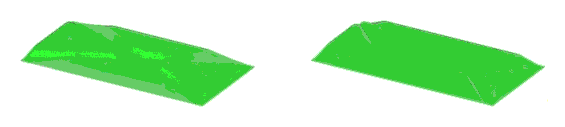
Figure 5. Common Bead Reinforcement Patterns for a Plate in Torsion
Results
The plate generated by OptiStruct using topography optimization is far stiffer than both of the conventional plates shown in Figure 5. Peak deflection for the topography plate is 0.83mm. For the conventional plates, the peak deflections are 1.27mm for the one on the left and 6.47mm for the one on the right. The plate developed with OptiStruct is 35% stiffer than a good conventional design and far better than a poor one. The poor design, while following the conventional wisdom of using an X-shaped reinforcement pattern, uses beads that run completely across the plate in a straight line which are susceptible to kinking when loaded. Such design mistakes are caught and corrected by OptiStruct during the optimization process allowing it to yield a superior design.