RD-V: 0230 Fabric Tensile and Compression
Simple fabric material behavior analysis under in plane tensile and compression loading.
The subject of this study is to analyze the behavior of the simple fabric material /MAT/LAW19 under in plane deformation.
Options and Keywords Used
Input Files
Model Description
Units: kg, ms, mm, GPa
Rectangular coupon is meshed with 4 noded and 3 noded shell elements.
One end of the coupon is clamped using a rigid body and a boundary condition.
The other end is set in a rigid body with an imposed displacement to model tensile and compression. The other degrees of freedom are fixed using a boundary condition.
- Property
- Value
- Density
- 8E-7 kg/mm3
- Elastic modulus direction 1 (E11)
- 0.3 GPa
- Elastic modulus direction 2 (E22)
- 0.5 GPa
- Shear modulus (E12)
- 0.05 GPa
- Compression stiffness reduction factor
- 0.1
- Poisson’s ratio
- 0 (for an easier computation of the theoretical value)
- Material direction 1 in the tensile direction
- Material direction 1 normal to the tensile direction
- Material direction 1 is oriented by 45 degrees to the tensile direction
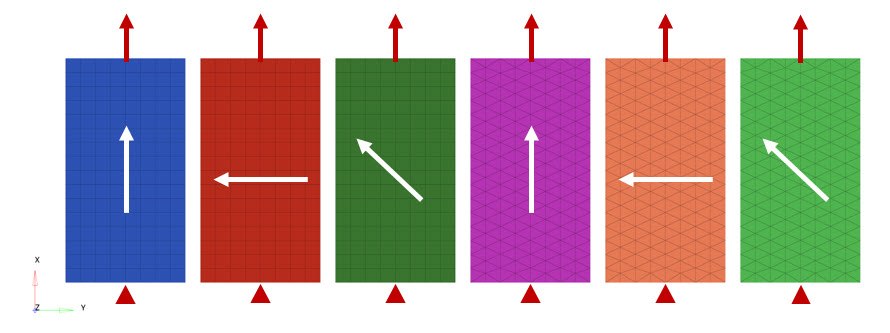
Results
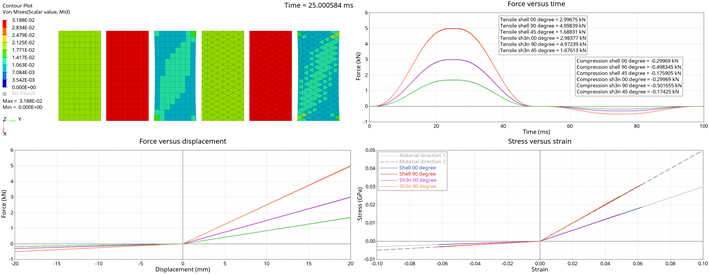
- Tensile 0 degrees = 3kN
- elongation (20) / initial length (320) * E11 (0.3) * width (160) * thickness (1)
- Tensile 90 degrees = 5kN
- elongation (20) / initial length (320) * E22 (0.5) * width (160) * thickness (1)
- Compression 0 degrees = 0.3kN
- RE (0.1) elongation (-20) / initial length (320) * E11 (0.3) * width (160) * thickness (1))
- Compression 90 degrees = 0.5kN
- RE (0.1) elongation (-20) / initial length (320) * E22 (0.5) * width (160) * thickness (1))
Results with Reference State
During the fabric seaming and/or folding process (airbag, seatbelt, seat cushion, etc.), the initial shape of the fabric component is usually smaller (or bigger) than the reference one, (the one before assembling). This reference shape can be stored in the reference state as /XREF (node based) or /EREF (element based).
From the previous model, the initial size of the sample is reduced by around 10% and the reference shape is stored in an /XREF card.
The imposed displacement is shifted by the distance to recover the reference state (+32mm).
- Around 0.1% of mass damping: alpha = 0.001 / time step = 0.851
- Around 1% of stiffness damping: beta = 0.01 * time step
In the results, there is no force (only small force from mass effect, inertia and stability numerical damping) until the displacement reaches 32mm because of the flag ZEROSTRESS=1 in the fabric material.
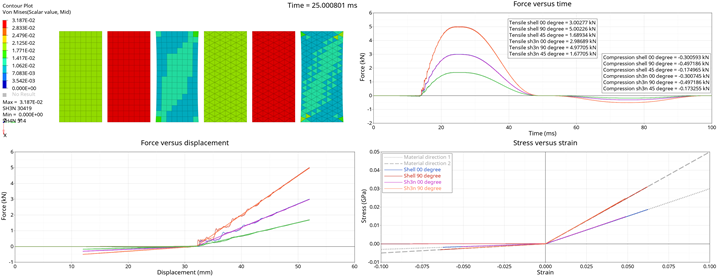
The initial compression strain (10%) can be seen in the stress strain curve.
There are elastic vibrations when the reference state is recovered because the material is bilinear without smooth transition between tensile and compression.
Conclusion
These models show the expected behavior for the tensile, compression and shear behavior. The reference state is correctly handled and the stresses are correctly canceled during the transition between initial shape and reference one.