Boundary Condition Sensitivity
This section discusses and illustrates the effects of the location of your model boundaries and the boundary conditions you apply on your CFD solution.
- Proximity of the boundary conditions with respect to the results of interest from the simulation.
- In the discussion of the geometric sensitivity of the model it is mentioned that the boundaries must be modeled far away from the region of interest to prevent any interference on the results due to proximity to the boundary. To understand the possible reasons behind this interference it is important to understand that the boundary conditions impose a constraint on the solution. This constraint is an assumption about the behavior of the flow. If the boundary is placed too close to a location in which the results are of interest it is possible that the solution will be impacted drastically by the constraint applied at the boundary.
- Realism of the constraints.
- Determining appropriate boundary conditions to apply to CFD simulations is often very challenging. This is particularly true when considering inflow conditions. You should consider the suitability of the constraints that are applied to the simulation. For example, analysts need to evaluate the suitability of applying constant values for velocity and turbulence variables at inlet conditions as opposed to specifying boundary layer profiles. These types of decisions can have a significant impact on the realism of the model and introduce errors into the simulation. If there is a separation location downstream of the inlet, the thickness of the incoming boundary layer is a critical parameter and needs to be considered when assigning the location and constraints to apply.
- Presence of reverse flow at outlet conditions.
- When modeling complex flows it is important to take into consideration the behavior of the flow at the outlet. Most CFD codes do not apply any constraints at outflow conditions that force the flow to exit the domain. If the flow is recirculating and entering back into the domain it is indicative that the boundary is poorly located. If repositioning the boundary is not possible you need to ensure that any flow quantities re-entering the domain are properly bounded. For example, in the case of a turbulent thermal flow that is re-entering the domain at an outlet boundary, it is necessary to assign a constraint on the temperature and turbulence quantities that are being convected back into the domain. Each CFD solver may handle this situation differently, so it is up to you to determine if this situation is acceptable.
The Backward Facing Step Case
- Proximity of the boundary conditions with respect to the results of interest from the simulation. If the boundaries in the backward step facing case are placed too close to the step it will have an adverse effect on the solution. If the outlet is too close to the step the presence of outlet constraints may interfere with the solution, preventing accurate representation of the recirculation zone and the reattachment point.
- Realism of the constraints. Two cases are presented to demonstrate the effect of inlet condition sensitivity on the solution of the backward facing step problem. The first case uses a constant value of velocity and turbulent eddy viscosity at the inlet. This case is derived from Mesh_4 from Mesh Sensitivity uses the same setup as mentioned in that section. The second case provides the inlet variables as a profile similar to the one used in an experimental study of the same problem. Figure 1 shows the profiles with boundary layer definition for the second case.
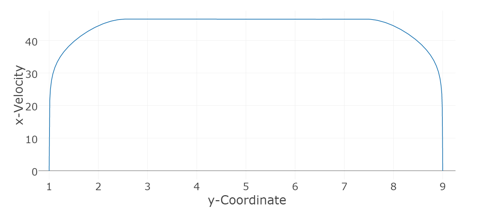
Figure 1. Inlet Velocity Profile
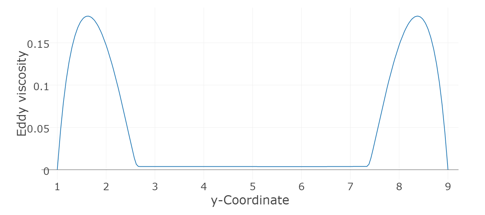
Figure 2. Inlet Turbulent Eddy Viscosity Profile for Inlet Boundary Condition Definition
The inlet velocity profile shows the presence of boundary layers at the edges while the eddy viscosity profile shows a concentrated presence of eddy viscosity in the boundary layer.
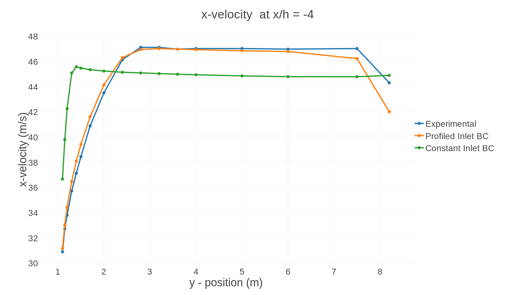
Figure 3. Velocity Profiles at x/h=-4 for Profiled and Constant Inlet Boundary Conditions Compared Against Experimental Data at the Same Location
You can see from the above comparison that using a boundary condition specification that resembles the real physics is much more likely to provide a correct solution to the problem.
Inlet condition type | Reattachment Length (m) |
---|---|
Constant | 5.73 |
Velocity profile with boundary layer definition | 5.96 |
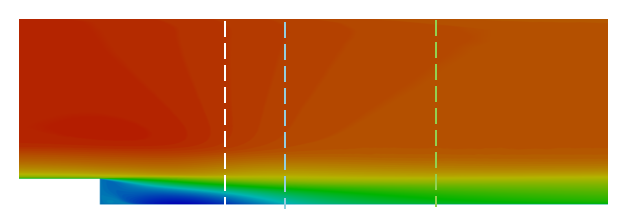
Figure 4. Candidate Locations for an Outlet Boundary on the Backward Facing Step Model