Turbulent Wake
At the low Reynolds number, the downstream flow of the cylinder has a symmetric flow pattern and produces near zero pressure drag.
When flow reaches Re ~ 100,000 vortices begin to shed from each side of the cylinder. This particular shedding pattern is called a Von Kármán vortex street. When the Reynolds number is about 1,000,000 a turbulent wake begins to form behind the cylinder. It is generated by the adverse pressure gradient at the peak position of the cylinder. This forms a large separation region where vortical structures interact and decay downstream. As the Reynolds Number increases the size of the turbulent wake decreases which in turn results in the reduction of the drag. This mainly attributes to the turbulent boundary formation on the cylinder, delaying the flow separation as it has a higher momentum near the cylinder than laminar flow.
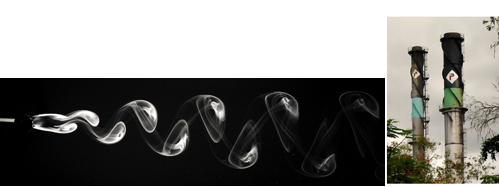
Figure 1. Vortex Shedding Formation Downstream of a Cylinder (left) and Chimney with Spirals (right)
Blunt bodies experience strong pressure drag compared to skin friction. This occurs due to the pressure imbalance between the front cross-section of the blunt bodies and the downstream cross-section. This pressure imbalance is attributed to the formation of downstream turbulent wakes, which reduces the local pressure. The high-pressure drag is a determinant factor of the flying range of a ball. As an example, it is common practice to make dimples on the surface of golf balls so that turbulent boundary layers form on the surface of a ball. This results in delayed flow separation and consequently reduces the size of the turbulent wake. Since the reduction of turbulent wake induces the smaller pressure drag, the golf ball with dimples should fly for a longer range when compared to the smooth ball.
Compared to the sphere in an airfoil at a low angle-of-attack (AOA) produces a smaller wake size, which results in the reduction of pressure drag. That is why the total drag is smaller for the airfoil than the ball, although the friction (viscous) drag is higher on the airfoil. Consequently, designers focus on the friction drag reduction by employing smooth surfaces. This is contrary to a ball with dimples for long flying range. However, since the turbulent wake size increases for high AOA, designers will shift their focus on reducing wake size by controlling flow on the airfoil suction side where it separates. Several methods are available, including a leading-edge extension, a vortex generator and a flow injection method.