FEMFAT
FEMFAT spotwelds are a particular realization type that conforms to the specifications outlined in the FEMFAT fatigue software.
Naming Conventions
Item | Name |
---|---|
Components | FEMFAT_Spot_Inner_Nugget_Comp_(parent comp ID) |
FEMFAT_Spot_Outer_Nugget_Comp_(parent comp ID) | |
FEMFAT_SPOT_BAR_Dia_xx(Diameter value)_Comp | |
Materials | Inner_Nugget_Mat_(self ID) -151 |
Outer_Nugget_Mat_(self ID) - 152 | |
Properties | FEMFAT_Spot_Inner_Nugget_Comp_(parent comp ID)_Prop |
FEMFAT_Spot_Outer_Nugget_Comp_(parent comp ID)_Prop | |
FEMFAT_SPOT_BAR_Dia_(Diameter value)_prop | |
System Collectors | FEMFAT_Spot_Center_Node_(System ID) |
FEMFAT_Spot_Inner_Nugget_Nodes_(System ID) - 115 | |
FEMFAT_Spot_Outer_Nugget_Nodes_(System ID) - 120 | |
FEMFAT_Spot_Outer_Nugget2_Nodes_(System ID) – 125 |
Item | Name |
---|---|
Components | FEMFAT_Spot_Inner_Nugget_Comp_(parent comp ID) |
FEMFAT_Spot_Outer_Nugget_Comp_(parent comp ID) | |
FEMFAT_SPOT_BAR_Dia_xx(Diameter value)_Comp | |
Materials | MAT(self ID) |
MAT(self ID) | |
Properties | FEMFAT_Spot_Inner_Nugget_Comp_(parent comp ID)_Prop |
FEMFAT_Spot_Outer_Nugget_Comp_(parent comp ID)_Prop | |
FEMFAT_SPOT_BAR_Dia_xx(Diameter value)_prop | |
Sets | MAT151 (ELSET which contains elements which has MAT151) |
MAT152 (ELSET which contains elements which has MAT152) | |
C115 (NSET contains nodes assigned to coordinate system 115) | |
C120 (NSET contains nodes assigned to coordinate system 120) | |
C350 (NSET contains nodes assigned to coordinate system 350) | |
System Collector | C_(System ID) |
C_(System ID) | |
C_(System ID) |
Material
- The material ID created for inner and outer nuggets should be based on the
interpretation of the base material. Note: If base material E > 150,000 N/mm2, then the material is considered as steel. In this case, follow these rules:
- Inner Nugget Material ID should be 151
- Outer Nugget Material ID should be 152
Note: If base material E < 150,000 N/mm2, then the material is considered as aluminum. In this case, follow these rules:- Inner Nugget Material ID should be 154
- Outer Nugget Material ID should be 155
- Inner Nugget should have mat ID = 151/154. Young's modulus of Mat 151/154 is calculated as 40 * Base sheets young's modulus.
- Outer Nugget should have mat ID = 152/155. Young's modulus of Mat 152/155 is equal to the surrounding sheet.
- Beam element is assigned Mat ID =152.
- If Young’s modulus is different for links, then the average Young’s modulus is used.
- If mat ID already exists in the session, it will be reused.
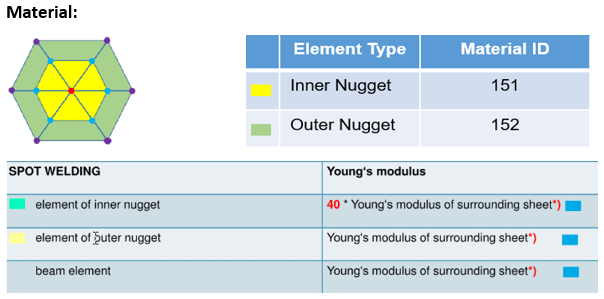
Figure 1.
Property
Profile | Description |
---|---|
Nastran and OptiStruct | PSHELL property with thickness derived from parent property. |
Abaqus | SHELLSECTION property with thickness derived from parent. |
Profile | Description |
---|---|
Nastran and OptiStruct | PBAR property is created and assigned a beam section (standard Rod section). The diameter of the rod should be the same as that of the FEMFAT weld diameter. |
Abaqus | BEAMGENSECTION property is created and a generic beam section is assigned. |
Diameter
Router = Input Diameter
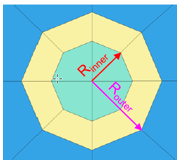
Figure 2.
System ID
- If total dia < 2.5, the System ID = 300. If total dia > 9.9, the System ID = 300.
- If diameter is in range 2.5-9.99, then create system between 325-399.
- Simple approach would be 300 + (Dia *10).
- If Dia = 2.5, the System ID = 325. If Dia = 9.9, the System ID = 399.
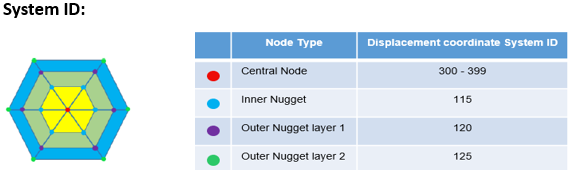
Figure 3.