Building AutoTire Test Rig using the Assembly Wizard
Using the Tire Test Rig, you can test the tire component of you model by running it under various conditions of Lateral slip, Longitudinal slip, and vertical loads.
Among the various objectives of the test rig, one of them is to cross-check the performance of the tire models against their property files.
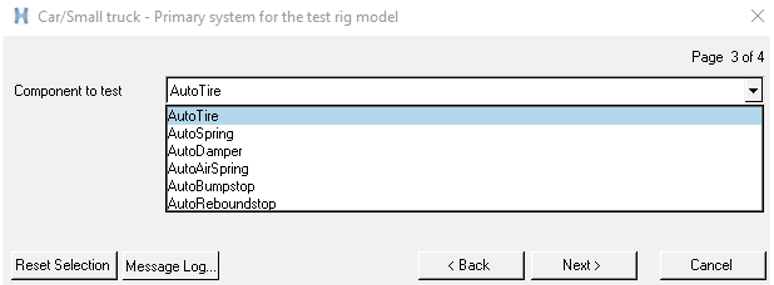
Figure 1. Building a Tire Test Rig
Topology
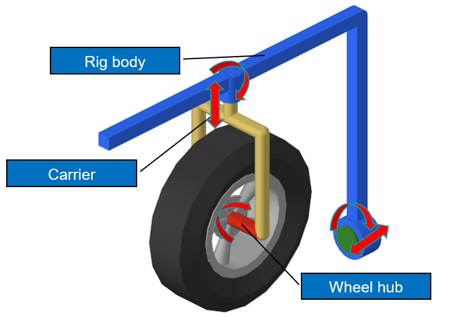
Figure 2. Test Rig Topology
- Rig body: This is the main structure that supports the tire. This is also the part that forces translational and camber motion to the tire.
- Carrier: The carrier holds the hub and can impose toe/steer and vertical motion to the tire.
- Wheel hub: The AutoTire is attached to this part. Wheel hub acts as the spindle for the tire and this is mounted on the carrier with a revolute joint. Spin motion on the tire is imposed using this revolute joint.
Dimensions of the Test Rig
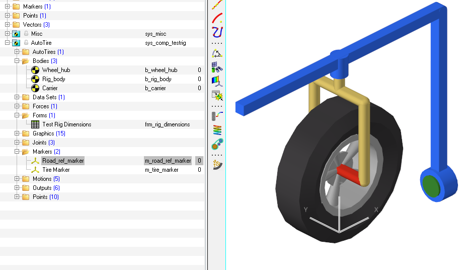
Figure 3. Road_ref_marker
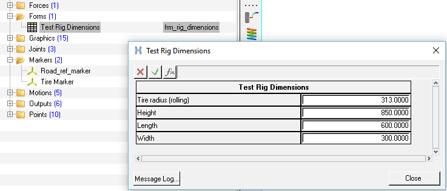
Figure 4. Editing Test Rig Dimensions
Choosing a Tire Model to Test
You can test any tire model that is supported in MotionSolve.

Figure 5. Choosing a Tire/Road Property File