Solution Settings
Summary of the settings available for refining SimSolid solutions.
SimSolid employs a proprietary adaptive technology to automatically refine the solution in the areas where it is necessary to achieve the highest accuracy. Multiple solution passes are performed and with each pass, accuracy measures are created and equations are enriched locally as required. All that needs to be specified by the user are the maximum number of solution passes along with a small set of optional settings.
Settings can be applied globally to the entire assembly or locally to individual groups of parts. This allow the user to first determine the overall system response, then quickly “drill-in” to specific areas of interest.
Settings are specified independently for each analysis. This provides a convenient method to do analysis comparison and solution convergence studies.
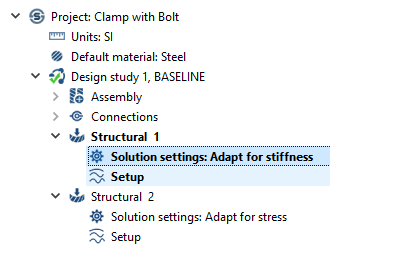
- Adapt for stiffness
- Use this objective for general load path prediction, modes and/or thermal analysis. This uses 3 adaptive passes and is typically the fastest solution method. No Adapt to features or Adapt to thin solids. Only uses global adaption
- Adapt for stress
- Use this objective for general stress calculation. This uses 4 adaptive passes and activates additional logic (Adapt to features and Adapt to thin solids) to more accurately refine in areas of high stress. Only uses global adaption.
- Custom
- This is the most general objective. All controls can be individually set. To improve the accuracy over the entire assembly, increase the number of adaptive solution passes. This is a primary control to increase solution refinement. Rarely needs to be set higher than 6. Use part local adaption to refine furthe
Individual Setting Controls
- Adapt to features – Uses special logic that has more aggressive adaptivity for stress gradient areas at local features. Applies only to structural linear and nonlinear statics. This is not used in modal or thermal analyses.
- Adapt to thin solids – provides special functions for a more accurate representation in thin curved solid sections. A best practice is to use this locally on a part by part basis.
- Refinement level – increases the refinement level locally
for a group of parts. Three levels are possible – standard, increased and
high.Important: Solution settings define a strategy of solution adaptation and are applied at the scale of the selected part group.
Global solution settings define the solution refinement strategy on the whole assembly assuming that accuracy requirements are approximately equal on all parts. Global solution settings scale is the size of the whole assembly. Local solutions setting define the solution refinement strategy on a part or group of parts. The scale of the settings is the size of the parts in the group.
Therefore, the same solution settings applied to the whole assembly or to a specific part will have different effects on the accuracy. The local settings are always more aggressive on the given set of parts because the scale is smaller. This facilitates the ability to do Global-local analysis and to focus the adaptive refinement on particular areas of interest.
Solution Settings Usage Roadmap
- Find overall system load path
- Use the Adapt for stiffness objective.
- Considerations for overall stress studies
- Use the Adapt for stress objective.
- Examine overall solution convergence
- Increase the number of adaptive passes and rerun the model. Number of passes can be set between 3 and 9, but this value is rarely set above 6.
- Considerations for local stress studies
- Use local part groups. Remember: Part group settings are done at the part group local scale.
- Considerations for thin curved solids
- Select the Adapt to thin solids check box. This is best done on a part-by-part basis using local part groups.