ACU-T: 3204 Radiation Heat Transfer in a Simple Headlamp using the Discrete Ordinate Model
Prerequisites
This tutorial introduces you to setting up a radiation heat transfer problem using the Discrete Ordinate radiation model in HyperWorks CFD. Prior to starting this tutorial, you should have already run through the introductory tutorial, ACU-T: 1000 Basic Flow Set Up, and have a basic understanding of HyperWorks CFD and AcuSolve. To run this simulation, you will need access to a licensed version of HyperWorks CFD and AcuSolve.
Prior to running through this tutorial, click here to download the tutorial models. Extract ACU-T3204_headlamp.x_t from HyperWorksCFD_tutorial_inputs.zip.
Problem Description
Figure 1.
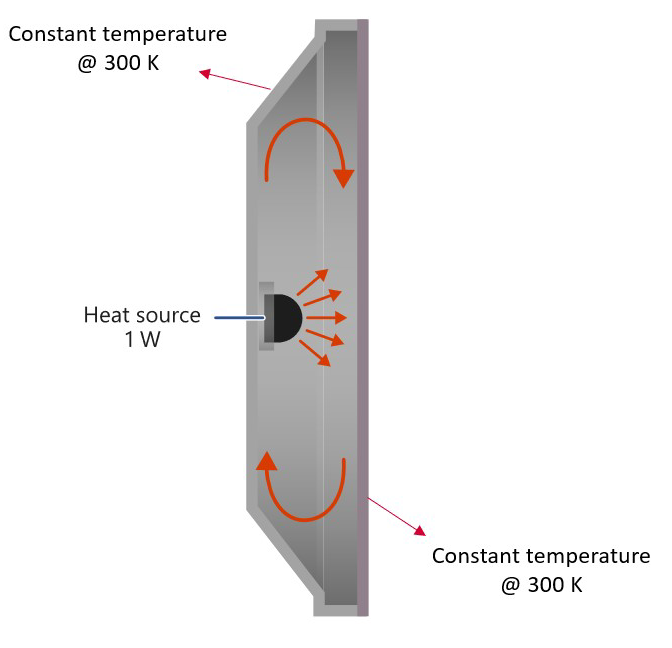
Figure 2.
Absorption Coefficient | Refractive Index | |
---|---|---|
Air | 0 | 1.0 |
Lens | 900 | 1.57 |
Surface Type | Radiation Surface Type |
---|---|
Participating medium - Participating medium Interface | Radiation Interface - Internal |
Participating medium - (Non- Participating) medium Interface | Wall |
External boundaries of Participating medium | Radiation Interface - External or Wall |
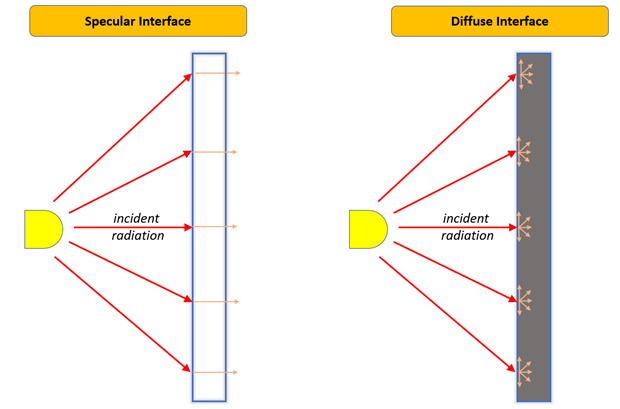
Figure 3.
Start HyperWorks CFD and Create the HyperMesh Model Database
Import and Validate the Geometry
Import the Geometry
Validate the Geometry
Set Up Flow
Set the General Simulation Parameters
Define the Material Models
Assign Material Properties
Define the Heat Source
Define Flow Boundary Conditions
In this problem, all the surfaces are walls and will therefore be assigned the default wall boundary condition. The outer walls of the headlamp will be given a no-slip wall boundary condition with a constant temperature.
Set Up Radiation
In this step, you will specify the parameters related to the thermal radiation setup.
Define Radiation Model Settings
Define the Emissivity Models
Define the Participating Media Radiation Models
Assign Participating Media Models
Assign Surface Finish Models
Define the Radiation Interfaces
Since the lens and air are defined as semi-transparent media, the interface between the two will be modeled as a specular interface of type: internal. Accordingly, the outer surfaces of the lens will be modeled as external interface radiation surface.
Generate the Mesh
In this step, you will define the mesh controls and then generate the mesh.
Define the Surface Mesh Controls
Define the Boundary Layer Controls
Define the Volume Mesh Controls
Since the thickness of the housing and the lens solids are small, you will use the thin layer meshing tool so that when the volume mesh is generated, there will be two layers across the thickness of those solids.
Generate the Mesh
Run AcuSolve
Post-Process the Results with HW-CFD Post
Summary
In this tutorial, you learned how to set up and solve a radiation heat transfer problem in a headlamp using the discrete ordinate radiation model in HyperWorks CFD. You started by importing and cleaning up the geometry and then set up the flow, thermal, and radiation boundary conditions. Once the solution was computed, you processed the results using the Post ribbon where you created contour plots of temperature and incident radiation.