シーム溶接疲労解析
シーム溶接疲労解析は、シーム溶接された構造の疲労解析を容易にするために使用できます。この解析では、シーム溶接ジョイントにおける疲労破壊をシミュレートして、対応する疲労破壊特性(損傷や寿命など)を評価できます。
HyperLifeで実装されているVolvo法は、M. Fermér、M Andréasson、およびB Frodinによって発行された研究論文Fatigue Life Prediction of MAG-Welded Thin-Sheet Structuresに基づいています。この方式は、薄いメタルシートに適用可能なホットスポット応力アプローチです。ホットスポット応力は溶接線における節点力から計算されます。この方法は、シート厚がが1.0 mm~3.0 mmの実験結果と十分な一致を示しています。この方法では通常、2 つのSNカーブが必要です。1つは曲げ応力による曲げS-N曲線で、もう1つは膜応力による膜S-N曲線です。
インプリメンテーション
モデリング要件
- シーム溶接疲労を解析する溶接部は、可能な限り、CQUAD4要素でメッシュする必要があります。回避できない場合や溶接線を終端させる場合は、必要に応じて、コーナー溶接にCTRIA3要素を使用できます。他の要素タイプは、現在、シーム溶接疲労に対してサポートされていません。
- 溶接は、1列または2列のCQUAD4要素でモデリングする必要があります。両側フィレットをモデリングする場合は、3列目のCQUAD4を使用できます。
- 溶接要素の厚みは有効スロート厚と同じです。
- 溶接の周りのメッシュサイズはできるだけ均一にする必要があります。この方式はメッシュサイズの影響をあまり受けませんが、Fermér、Andréasson、およびFrodinによれば、約10mmのメッシュサイズが妥当です。この論文では、均一なメッシュの場合、12mmと5mmのメッシュサイズの間に大きなホットスポット応力の違いがないことが示されています。
- 溶接要素には、セット / パートを介して参照することが可能です。HyperLifeでのユーザー定義のセット作成におけるCustom Zones補助
- 溶接要素の法線方向は、溶接ルート部ではなく、溶接トウ部に向くように外側に向ける必要があります。溶接要素の法線方向は、溶接のベースで検証する溶接トウとサーフェスを決定する際に重要な役割を果たします。
溶接の基本
- フェイス
- トウ
- スロート
- ルート
- レッグ
Figure 1. 基本溶接構造
溶接設計の優れた実践方法
この項では、溶接構造内の応力集中の基本的な概要と優れた溶接設計のための推奨事項について説明します。この項は、溶接設計の推奨事項を網羅しているわけではないため、完全な溶接設計ガイドとして見なさなでください。
- 溶接形状ベースの応力集中:Figure 2 は、溶接のトウにおける応力集中を示しています。その大きさは、フランク角、局所溶接トウ半径rおよびプレート板厚tで決まります。溶接金属が増える、つまりフランク角が大きくなると、実際に応力集中が増大することが確認できるため、溶接補強という概念は誤りです。
Figure 2. シーム溶接疲労に関する応力集中と溶接半径およびプレート板厚の関係 - 溶接設計ベースの応力集中:
2つ目の応力集中はジョイント設計からもたらされます。構造内で剛性が変化すると必ず応力集中が発生します。これは、剛性の増加または減少に起因します。たとえば、プレートの穴は、プレートに追加された剛体ボスとほぼ同じ応力集中を示します。ここで、溶接ジョイント例を優れた設計と不良な設計で比較して示します。
まず、曲がったビームに溶接されたカバープレートについて考えます。カバープレートの端では、剛性が大きく変化するため、大きな応力集中が発生します。剛性が段階的に変化する良好な設計を右側に示します。
Figure 3. (a) 間違った溶接設計 (b) 正しい溶接設計: 段階的剛性勾配2つ目の応力集中の発生源は、非対称形状によって引き起こされる不測の曲げ応力です。左側の設計では、右側のダブルラップジョイントより大きな曲げ応力が発生します。
Figure 4. (a) 間違った溶接設計 (b) 正しい溶接設計:ダブルラップジョイント対称形状厚みまたは幅が異なるプレートの溶接には問題がつきものです。上と同様に、最も簡単な溶接形状で最も大きい応力集中が発生します。必ず、溶接は構造内の応力の少ない領域に移動するよう考慮し、Figure 5(b)に示すジョイントのように剛性を段階的に移行させる必要があります。
Figure 5. (a) 間違った溶接設計 (b) 正しい溶接設計:段階的剛性移行
サポートされている溶接タイプ
HyperLifeは、シーム溶接疲労解析用に特定の溶接タイプをサポートします。
- 溶接フェイス要素または溶接レッグのいずれかに対して定義できる要素の列は1つのみです。
- 損傷計算位置は、溶接タイプに基づいて自動的に選択されます(フィレットを参照)。スロート損傷位置を除いて、ルートとトウの両方の損傷位置が、溶接要素に隣接する対応する要素で発生する節点力とそれに続く応力に基づいて評価されます。スロート損傷の場合は、溶接要素の節点力とそれに続く応力が直接考慮されます。
- HyperLifeは、現在、以下の溶接タイプをサポートしています。
フィレット
Figure 6. (a) フィレット溶接の構造; (b) Tジョイントシーム溶接要素の表現
HyperLifeは、溶接要素がCQUAD4の場合に、ルートとトウでの損傷を評価します。CTRIA3が溶接要素として使用されている場合は、トウのみが評価されます。
Tジョイント
- 片側1列片側1列のTジョイントの場合は、溶接要素の法線方向を溶接トウに向ける必要があります。溶接要素の節点は溶接トウと一致します。長さは、溶接要素の実際の寸法(一般的には、L=T1+T2)で決定する必要があります。
Figure 7. 1列のCQUAD4要素による片側Tジョイントフィレット溶接の表現溶接要素の厚みは、実効溶接スロート(通常はL/1.414)です。
- 片側2列溶け込みが大きく、一般的に溶接によって2つのプレート間の接触の基礎が形成される溶接の場合は複数列をお勧めします。このような溶接は、溶け込みが小さい溶接よりも剛性が高くなるため、挙動を捕捉するには溶接シェル要素の追加の列が必要となります。Figure 8では、Figure 7よりも溶接が溶け込んでいます。片側2列のTジョイントの場合は、2つの溶接要素の法線方向を溶接トウに向ける必要があります。長さは、溶接要素の実際の寸法(一般的には、L=T1+T2)で決定する必要があります。
Figure 8. 2列のCQUAD4要素による片側Tジョイントフィレット溶接の表現溶接要素の厚みは0.35*Lに設定することをお勧めします。
- 両側2列両側2列のTジョイントの場合は、溶接要素の法線方向を、対応する溶接トウに向ける必要があります。溶接要素の節点は対応する溶接トウと一致します。長さは、溶接要素の実際の寸法(一般的には、L=T1+T2)で決定する必要があります。
Figure 9. 2列のCQUAD4要素による両側Tジョイントフィレット溶接の表現溶接要素の厚みは、個別の実効溶接スロート(標準は1.414*L)です。
- 両側3列
クロスジョイント
- 片側1列片側1列のクロスジョイントの場合は、溶接要素の法線方向を、対応する溶接トウに向ける必要があります。
Figure 11. 各1列のCQUAD4要素による片側クロスジョイントフィレット溶接の表現 - 片側2列
溶け込みが大きく、一般的に溶接によって2つのプレート間の接触の基礎が形成される溶接の場合は複数列をお勧めします。このような溶接は、溶け込みが小さい溶接よりも剛性が高くなるため、挙動を捕捉するには溶接シェル要素の追加の列が必要となります。Figure 12では、Figure 11よりも溶接が溶け込んでいます。片側2列のクロスジョイントの場合は、溶接要素の法線方向を、対応する溶接トウに向ける必要があります。垂直溶接要素の法線も、対応する溶接トウに向ける必要があります。
Figure 12. 各2列のCQUAD4要素による片側クロスジョイントフィレット溶接の表現 - 両側2列両側2列のクロスジョイントの場合は、溶接要素の法線方向を、対応する溶接トウに向ける必要があります。
Figure 13. 各2列のCQUAD4要素による両側クロスジョイントフィレット溶接の表現 - 両側3列
溶け込みが大きく、一般的に溶接によって2つのプレート間の接触の基礎が形成される溶接の場合は複数列をお勧めします。このような溶接は、溶け込みが小さい溶接よりも剛性が高くなるため、挙動を捕捉するには溶接シェル要素の追加の列が必要となります。Figure 14では、Figure 12よりも溶接が溶け込んでいます。
両側3列のクロスジョイントの場合は、溶接要素の法線方向を、対応する溶接トウに向ける必要があります。垂直溶接要素の法線は、各側の溶接トウのいずれかに向けることができます。
Figure 14. 各3列のCQUAD4要素による両側クロスジョイントフィレット溶接の表現
オーバーラップまたはレーザーエッジオーバーラップ
Figure 15. オーバーラップ溶接の構造
メッシングルールはフィレット溶接と同じです。溶接要素の法線方向は溶接トウに向ける必要があります。溶接節点は溶接トウのラインに沿っている必要があります。溶接要素の厚みは実効溶接スロートにする必要があります。レーザー溶接では、溶接スロートにおける損傷が溶接トウや溶接ルートと同様に評価されます。
2列オーバーラップ
溶け込みが大きく、一般的に溶接によって2つのプレート間の接触の基礎が形成される溶接の場合は複数列をお勧めします。このような溶接は、溶け込みが小さい溶接よりも剛性が高くなるため、挙動を捕捉するには溶接シェル要素の追加の列が必要となります。溶接要素の標準的な長さは、L=T1+T2です。
Figure 16. 2列オーバーラップ溶接の表現
1列オーバーラップまたは1列レーザーエッジオーバーラップ
Figure 17. 1列オーバーラップ溶接またはレーザーエッジオーバーラップ溶接の表現
1列オーバーラップまたは1列レーザーエッジオーバーラップ(代替)
Figure 18. 1列オーバーラップまたはレーザーエッジオーバーラップの代替アプローチの表現
レーザーオーバーラップ
Figure 19. レーザーオーバーラップ溶接の表現
損傷評価
損傷評価ポイントは、溶接タイプによって異なります。
Figure 20. エンティティを適切に識別するための属性
フィレット
ホットスポット応力
HyperLifeは、トウ / ルート要素の節点力に基づいてホットスポット応力を計算します。
Fermér、Andréasson、Frodinが提案しているオリジナルのアプローチでは、目的の要素にかかる節点力が“調整”なしで直接使用されます。後の研究(P. FranssonとG. Pettersson、2000年)によって、節点力を平均化すると、節点力のメッシュ感度が下がることがわかっています。
- HyperLifeは、溶接トウ、溶接ルート、溶接スロート、およびそれらの評価サーフェスにおける潜在的な損傷位置を溶接要素の位置と法線方向から特定します(前項を参照)。
- 対応するルート損傷位置とトウ損傷位置(隣接要素内)に対して、およびスロート(溶接要素内)内で、局所座標系が構築されます。局所X軸は、溶接線上の隣接要素の中心にある対応する溶接要素フェイスに垂直に離れる方向に構築されます(X軸は隣接要素の平面内に配置されます)。局所Y軸は、隣接要素の平面内のこのX軸に垂直に構築されます。
Figure 23. シーム溶接応力計算の例 - 節点力は、溶接線に沿った隣接要素(2)のグリッド(QとR)で計算されます。節点力には、隣接要素に結合された要素(1と3)が寄与します。 節点力は次の式で計算されます:
(1) (2) モーメントは次のように表されます:(3) (4) - 溶接線上に配置された隣接要素の各節点(と)では、溶接トウのライン上の隣接要素と結合要素の長さで重み付けされた節点力 / モーメントの平均が計算されます。重み付けされた力は次のように表されます:
(5) (6) 重み付けされたモーメントは次のように表されます:(7) (8) - 線力とモーメントは、重み付けされた節点力とモーメントに基づいて計算されます。溶接線上の隣接要素の両端の線力とモーメントが平均化され、その中間点()での線力とモーメントが生成されます。線力は次の式で計算されます:
(9) (10) 線モーメントは次の式で計算されます:(11) (12) 要素2の中間点における平均化された線力と線モーメントは、次のようになります:(13) (14) - その後、中間点における線力と線モーメントがステップ2で構築された局所座標系で解析され、それぞれ、とが生成されます。この力とモーメントのペアから、溶接線に対する隣接要素内の引張応力と曲げ応力が導かれます。これらが応力の計算に使用される力です。
- その後、応力がこの力とモーメントのペアから隣接要素の溶接線に垂直に計算されます。応力はシェル要素の上部と下部の両方に対して計算され、溶接のタイプに応じて、そのどちらかまたは両方が疲労計算に使用されます。これが、さらなるS-N疲労損傷評価に使用される最終的なホットスポット応力です。追加の情報については、応力-寿命(S-N)アプローチをご参照ください。
(15) (16)
疲労特性
疲労挙動を制御可能なシーム溶接疲労解析に関連したいくつかの疲労特性があります。
曲げ率
Figure 24. 例:曲げ支配構造と薄膜支配構造の応力振幅と疲労寿命ログ(N)の比較
上側の曲線と下側の曲線は、それぞれ、曲げSN曲線と膜SN曲線と呼ばれます。膜SN曲線は要素内で膜応力が支配的な場合に使用し、曲げSN曲線は曲げ応力が支配的な場合に使用することをお勧めします。曲げ支配の度合いに応じて2つの曲線の間で補間が行われる場合もあります。
- 右記と等しい最大曲げ応力;
- 右記と等しい最大膜応力;
- は、損傷が計算されるシェル要素i(つまり、ルート、トウ、またはスロートシェル要素)の上面の最大応力の二乗
- シェル要素の曲げ率
は、
補間係数()は次のように定義されます:
--右記の場合;
--右記の場合;
Figure 25. 例:曲げ支配構造と薄膜支配構造の応力振幅と疲労寿命ログ(N)の比較
厚み補正
厚み補正プロセスは寸法効果補正用です。SN曲線は、特定の寸法の試験体によるテスト結果に基づきます。実際には、応力と寿命曲線は標本サイズによって異なる場合があります。そのため、厚み補正パラメータをこの効果の補正に使用できます。これは、疲労計算を考慮した各シェル要素(つまり、トウ、ルート、またはスロート要素)の厚みに基づいて適用されます。計算は次のように行われます:
の場合、厚み補正は行われません。
これにより、疲労寿命が縮まり、設計がより安全側になります。TREFとTREF_NはAssign Materialダイアログ内の対応するフィールド経由で定義できます。デフォルト値は、それぞれ25と0.2です。デフォルトはmmです。
シーム溶接疲労解析用に、Fatigue Moduleダイアログ内の対応する厚み補正フィールドを使用してのオンとオフを切り替えることができます。
平均応力補正
FKM平均応力補正がシーム溶接疲労に対してサポートされています。応力感度はFatigue MFKMMSSoduleダイアログの欄を介して定義できます。シーム溶接疲労の平均応力補正は、Seam Weld Fatigue Moduleダイアログを介して有効にすることができます。
FKM平均応力修正の詳細については、単軸S-N疲労の下のFKMセクションをご参照ください。
入力 / 出力
シーム溶接疲労解析をアクティブにするには、Fatigue ModulesのWeldsアイコンが選択されていなければなりません。

Figure 26.
疲労要素
現時点で、シーム溶接の計算には、シェル要素(望ましくはCQUAD4)がサポートされています。
疲労パラメータ
Seam Weld Fatigueダイアログで、FE Model Units、Mean Stress Correction、Certainty of Survival、Thickness Correctionの手法が定義されます。
FKM平均応力修正の詳細については、単軸S-N疲労の下のFKMセクションをご参照ください。
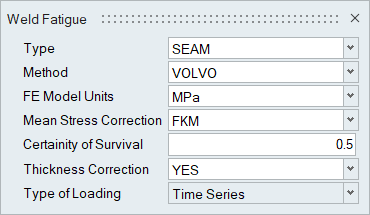
Figure 27.
疲労材料
- パート / セットへの材料の割り当てとSNカーブの定義を補助するMaterialツール。
- ユーザー定義の材料を生成、またはSN材料データベースから選択することが可能です。
Figure 28.
- BRATIO
- 臨界曲げ率
- TREF
- 板厚効果考慮のための参照板厚
- TREF_N
- 板厚効果考慮のための指数
疲労荷重
- 荷重履歴(チャンネル)をインポート、またはBlockシーケンス載荷を作成できます。
- イベントは、FEAサブケースと荷重履歴のペアリングを定義します。
出力
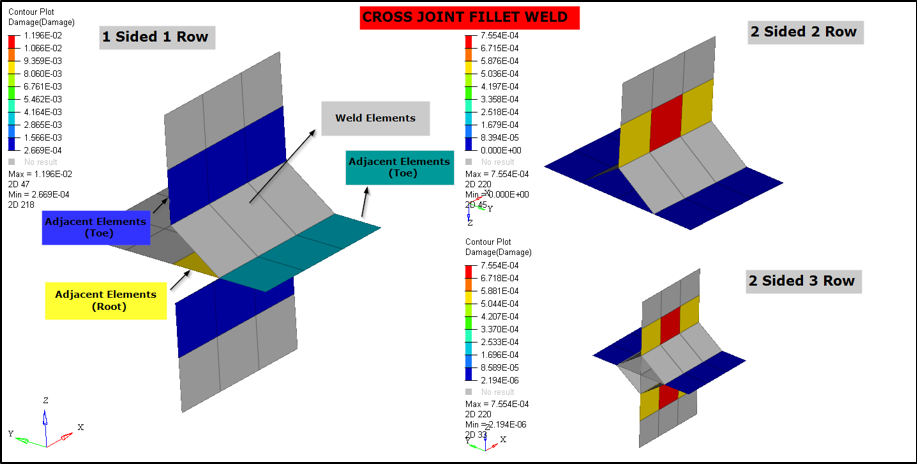
Figure 29. クロスジョイントフィレット溶接の損傷の出力例
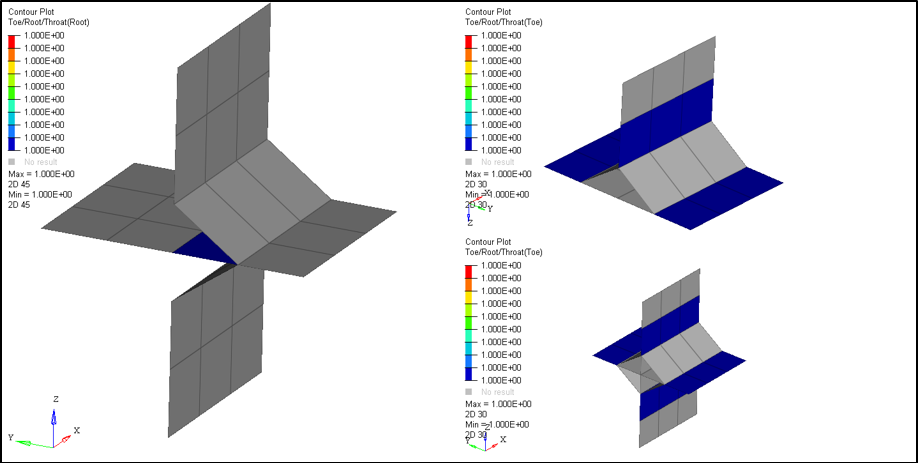
Figure 30. クロスジョイントフィレット溶接のトウ / ルート / スロート要素の出力例