Spot Weld Fatigue (FPM) using S-N Method
Spot weld fatigue can only be applied to spot welds between two shells. The spot weld location is defined by three attributes, sheet 1, sheet 2, and the nugget. The sheets are defined by shell elements, and the nugget is defined by CWELD, CBAR, CBEAM, or CHEXA elements. The nugget can be directly connected to the shells or RBE2/RBE3 elements can be used to connect the nugget to the shells.
The following file found in the optistruct.zip file is needed to perform this tutorial. Refer to Access the Model Files.
SpotWeld_CbarNugget.fem
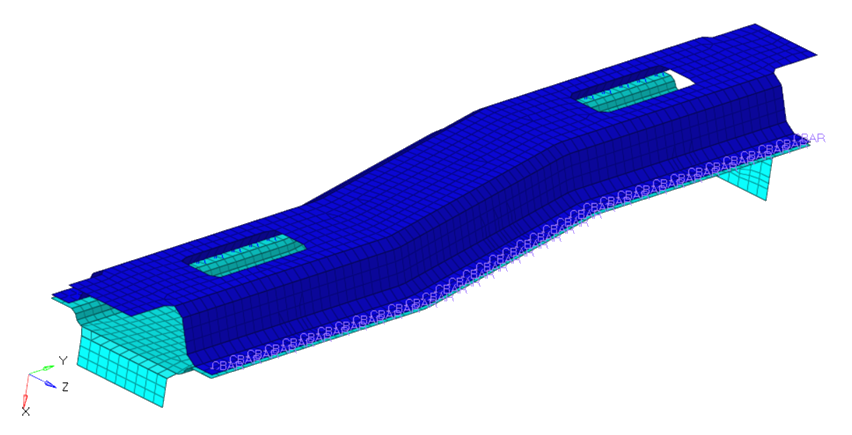
Figure 1. Spot Welds Modeled between Two Frame Sections
- Launch Fatigue Process Manager
- Import a model
- Create fatigue subcase
- Define fatigue analysis parameters
- Define fatigue elements and S-N properties
- Define load-time history and loading sequence
- Submit the job
- View results summary and launch HyperView for post-processing
Launch HyperMesh and Set the OptiStruct User Profile
The model being used for this exercise is that of an automotive frame (Figure 1). The input file consists of 3 static loadsteps to which the frame is subjected to – Frontal torsion, Rear torsion and the Vertical bending.
Import the Model
Set Up the Model
Create a Fatigue Subcase
Define Fatigue Parameters
Add Fatigue Elements and Materials
Make sure the task Elements and Materials is selected in the Fatigue Analysis tree.
Define PFATSPW Property
- In the Model Browser, right-click and select .
- For Name, enter PFATSPW.
- For Card Image, select PFATSPW.
- Set SPTFAIL to All.
- Set ALPHA to 3.5.
- Set TREF to 1.0.
- Set TREF_N to 0.2.
- Set SF to 1.0.
- Click Close.
Define FATDEF Load Collector
Apply Load-Time History
Load Sequences
Submit the Job
Make sure the task Submit Analysis is selected in the Fatigue Analysis tree.