Tutorial: Tool Deflection Analysis
Run a tool deflection analysis to determine where and how the tool is likely to deform during the extrusion process and help the die designer make corrections in the tool components accordingly.
Use tool deflection analysis to determine where and how the tool is likely to deform during the extrusion process and help the die designer make corrections in the tool components accordingly.
- Through coupled flow, thermal and stress analysis
- By writing a .fem file that contains tool mesh, material data, and BCs which can be submitted to OptiStruct solver for stress analysis
- Using the Tool Analysis Wizard in Inspire Extrude
The Tool Deflection Analysis Wizard has several advantages. The flow analysis and tool deflection analysis can be performed independently which helps in preventing the problem before it becomes too large. The analysis can be set up in a few steps.
- In the form of assumed temperature and pressures/forces on the
surfacesNote: Assumed pressure loads can be constant or vary linearly along the extrusion direction
- By mapping loads from a .hmascii file written by HyperXtrude while performing the flow analysis
Load Model
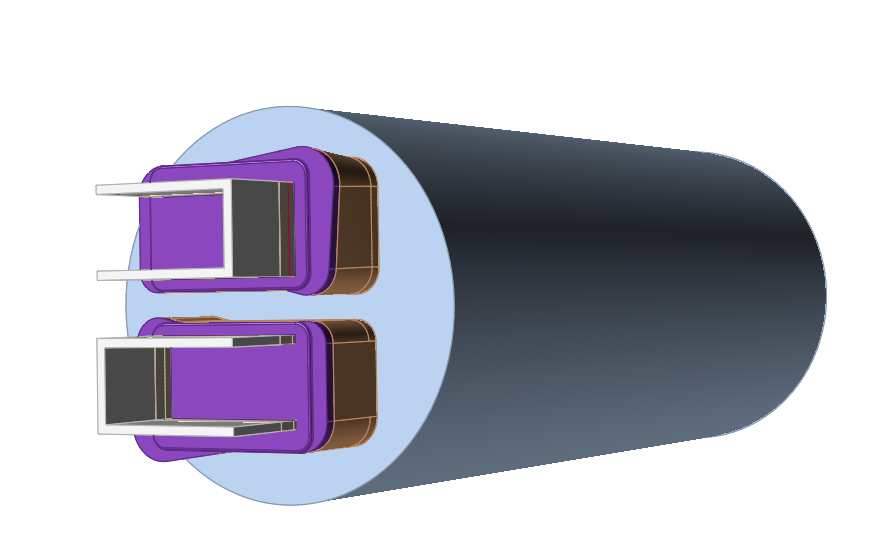
Delete Workpiece Components
This model contains two tool components, the feeder plate and die plate, as well as workpiece components that are not required for tool deflection analysis. Those components should be deleted before proceeding.
Organize Tool Components
This model contains two tool components, the feeder plate and die plate, which need to be organized.
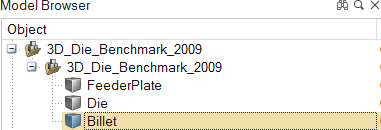
Simplify Geometry
The Simplify tools can be used to clean up problem areas in the geometry before running an analysis. They are used to delete extraneous lines, surfaces, and other components in the model and to remove unnecessary features such as holes used for instrumentation. This simplifies meshing and reduces the mesh size.
Create Load Faces
Create load faces where the material touches the tool geometry.
Workpiece material flowing inside the die exerts a load on tool surfaces and faces which are common between the workpiece and tool bodies. These are called load faces. Surfaces such as pin holes and relief regions are not in contact with the workpiece and should not be part of the load faces.
Create Constraints
The BCS tool is used to manually create constraints on appropriate surfaces.
Select the Material
Specify Process Parameters and Simulate
Status after submitting the job |
![]() |
Status after meshing is completed |
![]() |
Status when job is running in the solver |
![]() |
View Simulation Results
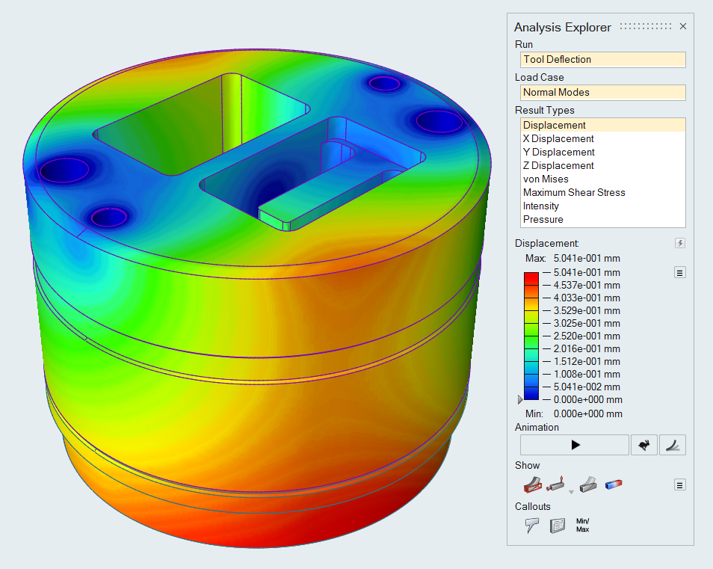
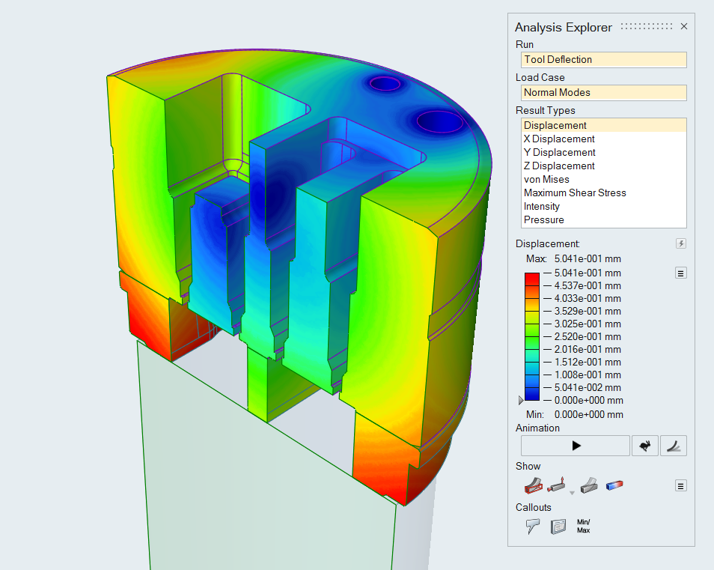
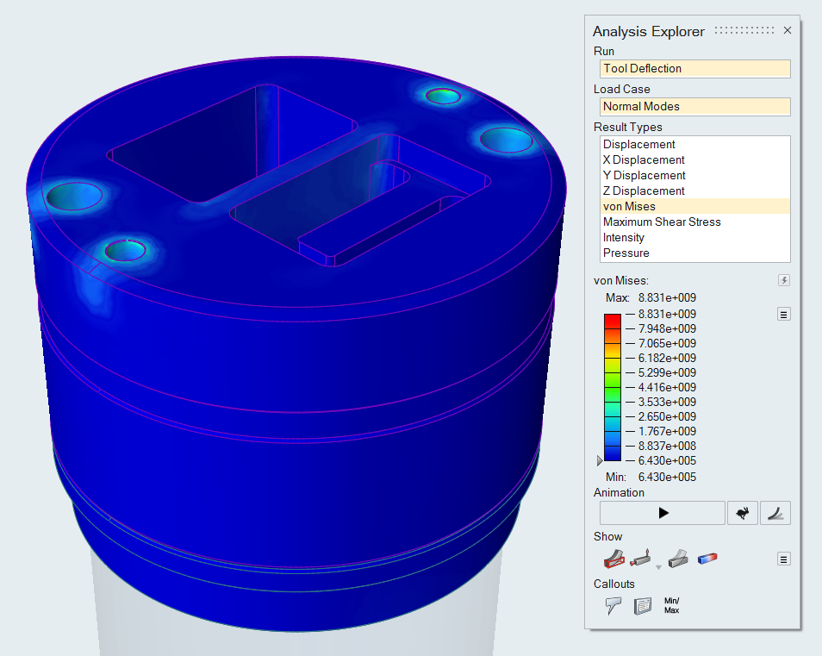