Test
The Test component is required to define the options in the Test Properties section.
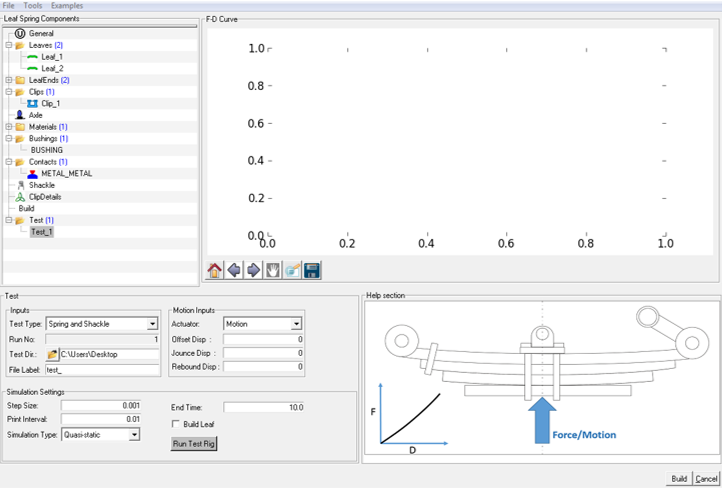
Figure 1. Test Component in Leaf Builder
Inputs
- Test Type
- Defines the type of test to execute the test process. There are two types: “Spring and Shackle” and “Spring only (SAE j510)”.
- Testing Directory
- Defines the folder location, where all the test files will be generated such as .mdl, .xml, .plt, and so on.
- File Label
- The field used to enter the required test file label.
Spring and Shackle - Force/Motion Inputs
- Actuator
- Depending on the type of Test Rig selected for the deflection option, it can be a force or applied motion.
- Offset force/displacement
- This field is used to set the initial force/displacement value before load cycle is started. Offset is relative to initial load/position of model.
- Jounce force/displacement
- Enter the increment of force or displacement relative to the initial force of displacement for jounce. The sum of the offset force and jounce force give the maximum force applied to the spring, if the actuator is force. Likewise, the sum of the offset displacement and jounce displacement give the maximum displacement applied to the spring, if the actuator is motion.
- Rebound force/displacement
- Enter the decrement (positive value) of force or displacement relative to the offset force or displacement for rebound. For a force actuator, the difference between the offset force and rebound force gives the minimum force applied to the spring. For example, if the initial force is 1000 N and the rebound force is 1000 N, then the minimum force in the test is zero (free position). For a motion actuator, the difference between the offset displacement and rebound displacements gives the minimum spring displacement.
Spring-only (SAE J510) - Motion Inputs
- Curb
- Displacement to push the system to the curb position.
- Design
- Displacement to push the system to the design position.
- Metal-Metal
- Displacement to push the system to the maximum deflection position.
Simulation Settings
- Print Interval
- This field is used to set a print interval for the output .plt file.
- Step Size
- This field is used to set the step size for the solver.
- Simulation Type
- Defines the Simulation type: Quasi-static or Transient.
- End Time
- Define the cycle time for force deflection.
- Build Leaf
- The tag that defines if the MDL is to be built when the Run Test Rig button is clicked.
- Run Test Rig
- Click the Run button to run the test event on the leaf spring.
Test Block for Leaf Property File (*lpf)
$----------------------------TEST_RIG
[TEST_RIG]
(TEST_1)
BUILDLEAF = 'FALSE'
CURB = 0.0
DESIGN = 0.0
DIRECTORY = 'C:\USERS\DESKTOP'
ENDTIME = 10.0
FORCEJOUNCE = 0.0
FORCEOFFSET = 0.0
FORCEREBOUND = 0.0
METALTOMETAL = 0.0
MOTIONJOUNCE = 0.0
MOTIONOFFSET = 0.0
MOTIONREBOUND = 0.0
OPTION = 'MOTION'
OUTPUTFILELABEL = 'TEST_'
PRINTINTERVAL = 0.01
RUNNO = 1.0
SIMULATIONTYPE = 'QUASI-STATIC'
STEPSIZE = 0.001
TESTTYPE = 'SPRING AND SHACKLE'
- Block Name = 'Test_Rig' (Required)
- Sub-block name = 'TEST_1' (Required)
-
Attributes Type Valid Value Required BUILDLEAF - ‘TRUE’, 'FALSE'
CURB Real FORCEJOUNCE Real FORCEOFFSET Real FORCEREBOUND Real METALTOMETAL Real MOTIONJOUNCE Real MOTIONOFFSET Real MOTIONREBOUND Real ENDTIME Real PRINTINTERVAL Real STEPSIZE Real DIRECTORY String OPTION 'MOTION', 'FORCE'
OUPUTFILELABEL String RUNNO Integer SIMULATIONTYPE 'QUASI-STATIC', 'TRANSIENT'
TESTTYPE 'SPRING AND SHACKLE', 'SPRING ONLY (SAE j510)'