複合材破壊モデル
- /FAIL/HASHIN
- /FAIL/PUCK
- /FAIL/LAD_DAMA
- /FAIL/CHANG
複合材材料は、2種類の材料からなります(マトリックスと補強繊維)。各材料の破壊挙動は異なります。Radiossでは、同一複合材要素内でマトリックスと繊維に異なる破壊モデルを使用できます(TYPE11、TYPE16、TYPE17、TYPE51、PCOMPP、またはTYPE22というプロパティを持つ要素の場合)。たとえば、繊維破壊に/FAIL/HASHIN、マトリックス破壊に/FAIL/PUCK、層またはプライ間の剥離に/FAIL/LAD_DAMAを使用できます(複合材に複数の層またはプライが定義されている場合)。
上記の一般的な複合材破壊モデルに加えて、/FAIL/FLD(ガラスのような、層(プライ)内の等方性脆性複合材材料に使用されます)、/FAIL/ENERGY、/FAIL/TBUTCHER、および/FAIL/TENSSTRAINを使用して、複合材の層(プライ)の破壊を表現することもできます。
/FAIL/HASHIN
- 繊維モード: 引張時の繊維破断または圧縮時の繊維座屈が原因で、複合材が破壊します。したがって、/FAIL/HASHINでは、引張 / せん断繊維モード、圧縮繊維モード、およびクラッシュモードは繊維モードです。方向1が繊維方向である場合、平面23が繊維モードの主な破壊平面となります。
- マトリックスモード: 繊維からのマトリックス亀裂が原因で、複合材が破壊します。破壊マトリックスモード(またはせん断破壊マトリックスモード)と剥離モードはどちらもマトリックスモードです。マトリックスモードの破壊平面は繊維と平行であり、応力σ11はこのモードでは考慮されません。
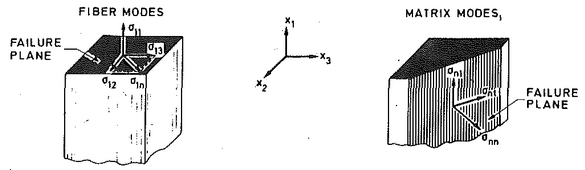
一方向薄層モデル | 繊維薄層モデル | |
---|---|---|
損傷基準 | D=1の場合は、破壊。 0≤D<1、Dの場合は、破壊なし。 ここで、 D=Max(F1,F2,F3,F4) |
D=1の場合は、破壊。 0≤D<1、Dの場合は、破壊なし。 ここで、 D=Max(F1,F2,F3,F4) |
引張 / せん断繊維モード | F1=(〈σ11〉σt1)2+(σ212+σ213σf122) | F1=(〈σ11〉σt1)2+(σ212+σ213σfa2) F2=(〈σ22〉σt2)2+(σ212+σ223σfb2) ここで、 σfa=σf12 , σfb=σf12σt2σt1 |
圧縮繊維モード | F2=(〈σa〉σc1)2 ここで、 σa=−σ11+〈−σ22+σ332〉 |
F3=(〈σa〉σc1)2 ここで、 σa=−σ11+〈−σ33〉 F4=(〈σb〉σc2)2 ここで、 σb=−σ22+〈−σ33〉 |
クラッシュモード | F3=(〈p〉σc)2 ここで、 p=−σ11+σ22+σ333 |
F5=(〈p〉σc)2 ここで、 p=−σ11+σ22+σ333 |
せん断破壊マトリックスモード | F6=(σ12σm12)2 | |
破壊マトリックスモード | F4=(〈σ22〉σt2)2+(σ23S23)2+(σ12S12)2 ここで、 S12=σm12+〈−σ22〉tanϕS23=σm23+〈−σ22〉tanϕ |
|
剥離モード | F5=S2del[(〈σ33〉σt3)2+(σ23˜S23)2+(σ13S13)2] ここで、 S13=σm13+〈−σ33〉tanϕ˜S23=σm23+〈−σ33〉tanϕ |
F7=S2del[(〈σ33〉σt3)2+(σ23S23)2+(σ13S13)2] ここで、 S13=σm13+〈−σ33〉tanϕ˜S23=σm23+〈−σ33〉tanϕ |
/FAIL/HASHINでは、材料強度σt1,σt2,σt3,σc1,σc2は、複合材の引張 / 圧縮試験から得られます。
破砕強度σcと繊維せん断強度σf12は、準-静的パンチせん断試験(QS-PST)から得ることができます。6 サポートスパン径対パンチ径比率(SPR)からの破砕強度σcは0であり、SPRからの繊維せん断強度σf12は1.1です。
ϕ はクーロン摩擦角です。複合材が(引張ではなく)圧縮も受けている場合は、複合材のせん断強度が高まることが確認されています。その原因は、マトリックスと繊維間の摩擦です。
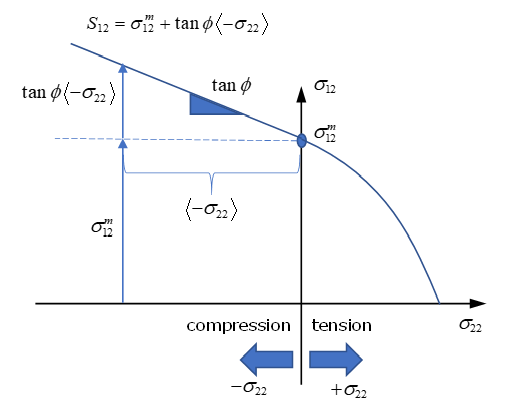
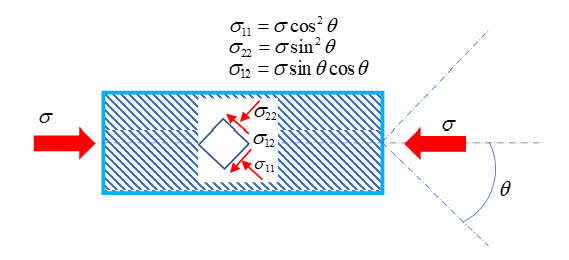
σm12,σm13,σm23 は、3方向のマトリックスせん断試験から得ることができます。
Sdel は、剥離基準のスケールファクターです。これは、実験で剥離破壊を損傷領域と相関付けるための複合材剥離実験データによってフィッティングできます。
/FAIL/PUCK
- 繊維破壊: 繊維が引張強度または圧縮強度の限界に達することにより、複合材が破壊します。
- 繊維間破壊(IFF): 繊維マトリックスの亀裂が原因で、複合材が破壊します。
損傷基準 | D=1の場合は、破壊。 0≤D<1の場合は、破壊なし。 ここで、 D=Max(ef(tensile),ef(compression),ef(ModeA),ef(ModeB),ef(ModeC)) |
繊維部破壊 | 引張繊維破壊モード: σ11>0 ef(tensile)=σ11σt1 |
圧縮繊維破壊モード: σ11<0 ef(compression)=|σ11|σc1 |
|
繊維間破壊(IFF) 2 | モードA(σ22>0の場合):![]() ef(ModeA)=1ˉσ12[√(ˉσ12σt2−p+12)2σ222+σ122+p+12σ22] |
モードC(σ22<0の場合):![]() ef(ModeC)=[(σ122(1+p−22)ˉσ12)2+(σ22σc2)2](σc2−σ22) |
|
モードB: ![]() ef(ModeB)=1ˉσ12(√σ212+(p−12σ22)2+p−12σ22) |
繊維間破壊では、モードAは横繊維方向(繊維方向に対して直角)の引張がかかった状態の破壊を示し、この場合、せん断荷重によって破壊限界が引き下げられる可能性があります。
横繊維方向の圧縮がかかっている場合、最初は圧縮が増大すると、複合材のせん断荷重も増大します(モードB)。圧縮が増大し続けると、せん断荷重は減少に転じます(モードC)。
入力パラメータ
繊維破断破壊の場合、繊維強度σt1,σc1は、繊維方向の引張および圧縮の複合材試験から得られます。
繊維間破壊の場合、強度σt2,σc2は、横繊維方向の引張および圧縮の複合材試験から得られます。
せん断強度ˉσ12は、純せん断試験(σ2=σ1=0)によって得られます。
σt2,σc2,ˉσ12を使用して、モードBとモードCのp−22とp−12が求まります。
σt2,ˉσ12と、横繊維方向の追加の引張-せん断試験により、p+12が求まります。横繊維方向の追加の引張-せん断試験では、等しい引張-せん断(σ22=σ12による)荷重を使用できます。
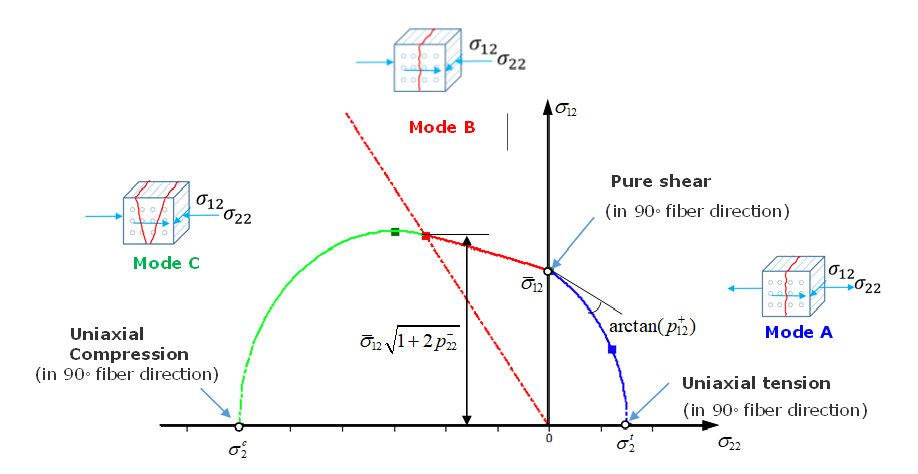
p+12,p−12,p−22パラメータについて3。カーボンファイバー複合材の場合はp+12=0.35,p−12=0.3,p−22=0.2を使用し、グラスファイバー複合材の場合はp+12=0.3,p−12=0.25,p−22=0.2を使用します。
/FAIL/LAD_DAMA
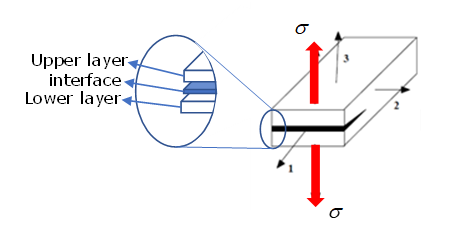
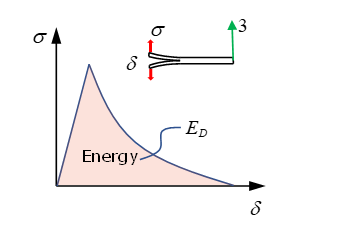
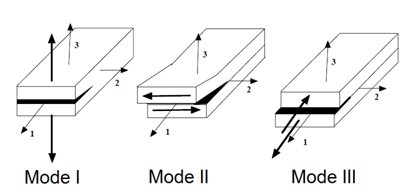
- t
- 仮想インターフェースの板厚。これは、層厚の5分の1と想定できます。
- G13、G23、 E33
- 上層または下層から。
- di
- 損傷変数(i=1,2,3)。
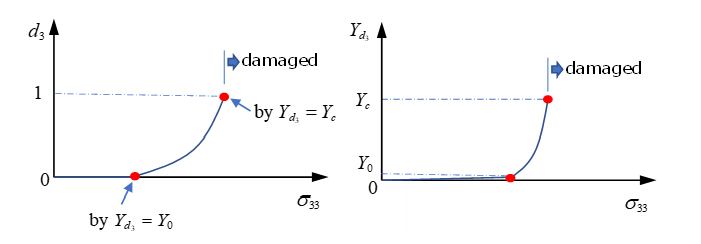
Y0に達すると、損傷変数は増加し始め、1に達すると、d3=1となります(この時点の熱力学的な力Yd3は臨界損傷Ycになります)。複合材は完全に剥離したと見なすことができ、複合材を直ちに削除するか、応力を小さくすることができます。Radiossでは、オプションτmaxを使用して指数関数的な応力減少をシミュレートし、Ycにおける応力はσd(tr)となります(損傷時の応力減少)。
- d≥1の場合、 d=1
- d<1の場合、dはYの関数(損傷評価則):
(4) d=w(Y)=〈√Y−√Y0〉√Yc−√Y0 Y=Yd3+γ1Yd1+γ2Yd2 ここで、 Ydi|t=supYdi|τ≤t
ここで、γ1,γ2は他の2つの剥離モードを考慮するためのスケールファクターです。これは実験によって検証できます(DCBとENFの試験体試験5)。
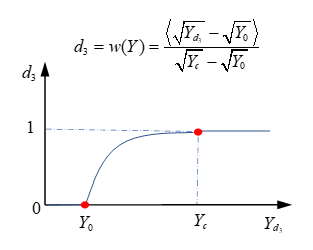
- d=1であれば、 ˙d=const.
- d<1であれば、 ˙d=ka[1−exp(−a〈w(Y)−d〉)]
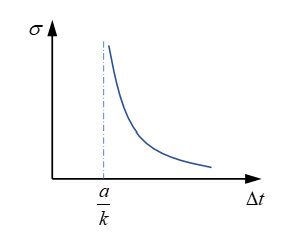
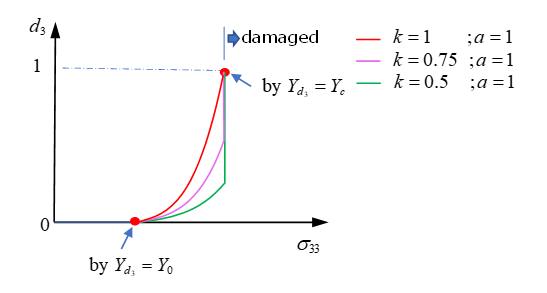
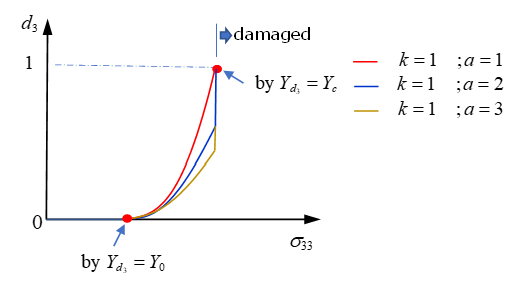
/FAIL/CHANG
- 繊維モード: 引張時の繊維破断または圧縮時の繊維座屈が原因で、複合材が破壊します。
- マトリックスモード: 引張時または圧縮時のマトリックス破壊が原因で、複合材が破壊します。
損傷基準 | D=1の場合は、破壊。 0≤D<1の場合は、破壊なし。 ここで、D=Max(ef2,ec2,em2,ed2)。 |
|
繊維破損 | 引張繊維モード σ11>0 | ef2=(σ11σt1)2+β(σ12ˉσ12)2 |
圧縮繊維モード σ11<0 | ec2=(σ11σc1)2 | |
マトリックス亀裂 | 引張マトリックスモード σ22>0 | em2=(σ22σt2)2+β(σ12ˉσ12)2 |
圧縮マトリックスモード σ22<0 | ed2=(σ222ˉσ12)2+[(σc22ˉσ12)2−1]σ22σc2+(σ12ˉσ12)2 |
- 方向1
- 繊維方向。
- σt1,σc1
- 繊維の引張 / 圧縮強度。
- σt2,σc2
- マトリックス強度。
- ˉσ12
- 複合材プライ平面のせん断強度。
- β
- せん断スケールファクター(実験によって特定できます)。
損傷時の応力減少
- HASHIN:
D=Max(F1,F2,F3,F4)≥1
- PUCK:
D=Max(ef(tensile),ef(compression),ef(ModeA),ef(ModeB),ef(ModeC))≥1
- LAD_DAMA:
d≥1
- CHANG:
D=Max(ef2,ec2,em2,ed2)≥1
ここで、 t≥tr
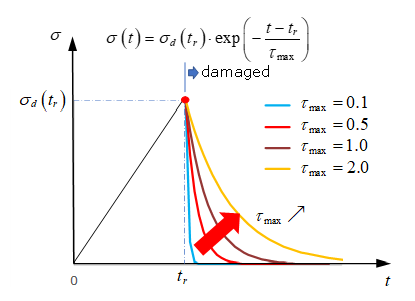
- σd(tr)
- 損傷がD≥1に達したときの応力成分。
- tr
- σd(tr)の時間。
- τmax
- 動的緩和の時間。